|
|
Joined: March 2007 Posts: 698
Location: Cork, Ireland | My Applause has been in its case for a few years unplayed. All it needed was a new nut but I've also added a Strat pickup across the soundhole! Action is a bit high but quite playable with electric strings tuned down whole tone. Saddle is shaved down as far as it can go I am considering a bowl bend but nervous about doing so. How risky is that repair? I've had it so long it would be a shame to mess it up for good.
https://imgur.com/PlY5wGZ
https://imgur.com/bP2nEoM
Edited by sycamore 2018-11-16 1:49 AM
|
|
|
|
 Joined: June 2012 Posts: 2330
Location: Pueblo West, CO | Let's just say that bowl bends aren't for the faint of heart. It takes a certain amount of intestinal fortitude to take a heat gun to the bowl of your Ovation (Applesauce) with the intention of warping it.
That being said, the most important aspect is that you want to keep the neck inline with the bridge. Because you're heating the bowl with the intention of warping you want to take steps to make sure you don't introduce any twist or skew of the neck while the resin of the bowl is in a softened state.
I accomplished this by building a jig to clamp the neck and bowl so they remained in alignment with each other while I heated the bowl.
I also worked slowly so I could sneak up on the neck angle I wanted. I heated it, warped it a little, let it cool, then checked the angle. I repeated this process until the neck angle was acceptable.
You'll need to get the bowl up to a temperature of ~200° F. The areas you want to concentrate on heating is the sides of the upper bout. Don't worry about heating the lower bout at all. It sounds scary, but actually the bowl won't turn into a potato chip unless you really overheat it. (~300° F) In fact, you'd have a really, really tough time doing that with a heat gun because of how quickly the bowl cools when you move the heat source away from it. If anything, you'll have a harder time keeping it heated enough to get the task done. If you want more details, I suggest a few theads:
1967 Balladeer Rebuild...
Bowl Bending Attempt An Early 1615 Rescue Mission Lastly, here's search on the BFLG forum for 'bowl bend': Search Results: Bowl Bend
Edited by DanSavage 2018-11-16 5:19 PM
|
|
|
|
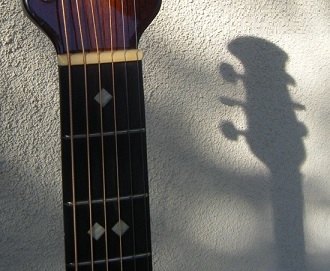 Joined: February 2016 Posts: 1846
Location: When?? | Ya just can't get any more Ovation/Adamas/Applause than using a term like "bowl bending" Life must be pretty boring on other guitar sites. Here's wishing you a good outcome should you undertake this adjustment. Please let us know how it turns out. |
|
|
|
Joined: March 2007 Posts: 698
Location: Cork, Ireland | Hmm. I've had her so long I dunno if I'm ready to take the risk. I knew you guys would have some good advice. |
|
|
|
Joined: April 2003 Posts: 608
Location: Caribou, ME | Is this a US Applause or Korean? If it's a US Applause, it has a bolt on neck and a bowl bend is totally unnecessary. |
|
|
|
 Joined: June 2012 Posts: 2330
Location: Pueblo West, CO | ^^^
What ksdaddy said.
Edited by DanSavage 2018-11-17 9:46 AM
|
|
|
|
Joined: November 2002 Posts: 3646
Location: Pacific Northwest Inland Empire | I found the bowl material makes a difference in this endeavor, also. Had better results with the hand-laid fiberglass bowl, than the molded Lyrachord variety. Also, the fiberglass bowl was on an 1113 Classical, & the Lyrachord was on a CC257 Applause, with steel strings (higher tension). |
|
|
|
 Joined: June 2012 Posts: 2330
Location: Pueblo West, CO | Yeah. The hand-laid bowls are what's known as a room-temperature lay-up, meaning the resin is allowed to cure at room temperature. Naturally.
The SMC bowls are molded in hot compression molds at 350° F.
The reason why we're able to effect a bowl bend a relatively low temp of 200° F is because of a characteristic of epoxy resin known as Tg, or glass transition temperature. The Tg is the temperature at which the resin reverts from a glassy state to a rubbery state. At this point the resin can be reshaped and when allowed to cool it will hold this new shape.
You could do this to SMC, too, but you'd have to heat it up to something over 400° F, which is too hot to deal with in a hobby setting.
Generally speaking most epoxies that use room temperature lay-ups have a Tg of about 180° F or so. You can perform a post-cure cycle which will gradually raise the temperature of the molded piece along a pre-determined schedule as it cures. The purpose of this is to raise the Tg so the final molded piece has a better tolerance to higher temperatures.
|
|
|
|
Joined: November 2002 Posts: 3646
Location: Pacific Northwest Inland Empire | Thanks, Dan!
That was very educational, as usual, & perhaps a bit esoteric to all of us "unwashed shadetree luthiers". It does explain well the experience & relative success I achieved with the old bowl, versus the newer one. So, the scenario is, basically, like my aging joints- they're low-tech now, too, & need some moderate encouragement.... |
|
|