|
|
Joined: November 2002 Posts: 3647
Location: Pacific Northwest Inland Empire | "Only Hope remained there in an unbreakable home within under the rim of the great jar, and did not fly out at the door; for ere that, the lid of the jar stopped her, by the will of Aegis-holding Zeus who gathers the clouds."
So, releasing the evils from the container, and maintaining the prospect of beauty & grace. I have some work to do. I have given the guitar a cursory examination. It appears to be functional, in its present state, and will require adjustments to the playability. The strings are pretty dead, though the instrument has quite a bit of punch & depth, though presently a bit muddy in the bass end. The highs are clear. Sustain is pretty good.
The nut has been replaced & there is a compensated saddle in the bridge. The neck fills my hand real well, and there are no cracks. The peghead still has both ears intact. Everything needs a good scrubbing- tuners & fretboard, especially.
As I surmised, the paint is awful, and the binding is a mess. The bridge appears sound, and will need a bit of paint removal, also.
First plan of action is to scrape off all that paint & see what the top looks like. The upper, bass end of the x-brace is loose, but everything else is secure. It looks like the MOP from the rosette is still on the guitar, so there needs to be a plan for the soundhole decoration. It looks like the rosette was recessed into the top, also.
So Paul, I may be able to save the top. That will be a major coup.
And Dave, you were correct. It is x-braced. With the A-918 serial #, the guitar was apparently made in late 1968.
Okay, so a few images to start this saga:
(1127 front view- smaller image.jpg)
(back view- smaller image.jpg)
(label 1.jpg)
(scraped top with binding pattern- small image.jpg)
Attachments ----------------
1127 front view- smaller image.jpg (87KB - 1 downloads)
back view- smaller image.jpg (84KB - 0 downloads)
label 1.jpg (81KB - 1 downloads)
scraped top with binding pattern- small image.jpg (82KB - 1 downloads)
|
|
|
|
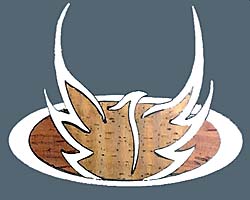 Joined: June 2002 Posts: 6202
Location: Phoenix AZ | Good luck Chris. Can't wait to see how this turns out. I meant to send you a new rosette for it, but mistakenly sent it to another member who has offered to forward it to you. Small cosmetic improvement, but I guess every little bit helps. Keep us posted. |
|
|
|
Joined: November 2002 Posts: 3647
Location: Pacific Northwest Inland Empire | I shall! And our generous fellow compatriot has contacted me. Thanks, Al! I will need all the help I can get. It is inherently a fine instrument, and deserves refurbishment. It has seen a long life, and its playability was maintained. I think it was gigged a long time. There is a name on the folded paper, used as a shim under the saddle, which I will pursue further.
What are the suggestions for that torn label? Should I just varnish it in place, or attempt to replace it? |
|
|
|
Joined: November 2002 Posts: 3647
Location: Pacific Northwest Inland Empire | Sent a request to GEWA about a graphic file for an age-appropriate paper label, since they have the legal rights to Ovation copyright and materials. See what develops from that.
I have a date with my cabinet scraper, probably extend into next week. Lotta nasty blue paint to remove. The lacquer thinner and citrus remover options look messy and tedious. Then, make some serious decisions about soundboard and neck angle issues. I think the neck may need to come off to install the replacement rosette, unless someone has clever means to accomplish the task, without major surgery. |
|
|
|
Joined: March 2002 Posts: 15674
Location: SoCal | If it was built in late 68, then it was probably one of the very early GCDB's. I believe in an older thread here we postulated (with Beal's help) that there were maybe 50 built all total. A really wonderful guitar with a short run at the factory..... |
|
|
|
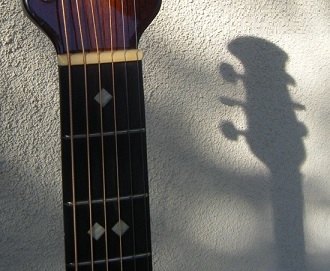 Joined: February 2016 Posts: 1846
Location: When?? | @seesquare - >>>What are the suggestions for that torn label?<<<
Hopefully GEWA will participate. If not, then perhaps a suitable duplicate can be made using your own graphic platform and printer. Then there is always DaveKell if you want something custom to represent the project-- as in the very cool "BBurg" label he made for Bernie's Viper creation.
Does the autograph signature on the top appear as anyone we may recognize?
Edited by Love O Fair 2022-01-08 3:27 PM
|
|
|
|
Joined: November 2002 Posts: 3647
Location: Pacific Northwest Inland Empire | That signature is illegible to me. And, it isn’t even close to the name on the saddle shim. So, just someone’s self-expression. The tuners get a good cleaning next. Really funky. |
|
|
|
Joined: November 2002 Posts: 3647
Location: Pacific Northwest Inland Empire | The tuners have been cleaned. A question for conjectural analysis. What is the optimal lubricant for repacking the gears? Got a supply of Vaseline, but wondered if there was something better.
(tuners 3- smaller image.jpg)
(clean tuner parts 2- smaller image.jpg)
(clean tuner parts 1- smaller image.jpg)
Attachments ----------------
tuners 3- smaller image.jpg (60KB - 0 downloads)
clean tuner parts 2- smaller image.jpg (92KB - 0 downloads)
clean tuner parts 1- smaller image.jpg (74KB - 0 downloads)
|
|
|
|
 Joined: October 2005 Posts: 4065
Location: Utah | seesquare - 2022-01-09 12:27 PM
The tuners have been cleaned. A question for conjectural analysis. What is the optimal lubricant for repacking the gears? Got a supply of Vaseline, but wondered if there was something better.
Just an amateur opinion, but I'd use a very tiny amount of gun grease. Oils eventually evaporate. Gun greases seem to stay in place for a long time. Use as little as possible.
Shooter's Choice makes a good grease in a syringe style applicator.
Another option is a food grade lithium grease. This is what I use on my guns because it works and it is cheaper than gun-specific products.
You can probably get away with no lube at all. idk. |
|
|
|
 Joined: June 2012 Posts: 2332
Location: Pueblo West, CO | seesquare - 2022-01-08 11:50 AM
I think the neck may need to come off to install the replacement rosette, unless someone has clever means to accomplish the task, without major surgery.
If you are using a rosette with a raised one, I've replaced them with the neck installed several times.
If you're inlaying one, then that's going to be a bit more trouble.
|
|
|
|
Joined: November 2002 Posts: 3647
Location: Pacific Northwest Inland Empire | Thanks for the input! I just figured, since the tuners come lubricated, I will repack them with some type of lubricant. How about some aerosol silicone? Doesn’t constitute much mass, but has great slippery properties. And it will get inside the tuner housing pretty well. Doesn’t attract dirt, either. |
|
|
|
Joined: November 2002 Posts: 3647
Location: Pacific Northwest Inland Empire | Thanks Dan. I will play it by ear for now. Will have to evaluate my options, as this project progresses. I’m just not relishing the idea of pulling the neck, if I don’t have to. Kinda depends on what I find after scraping the top. |
|
|
|
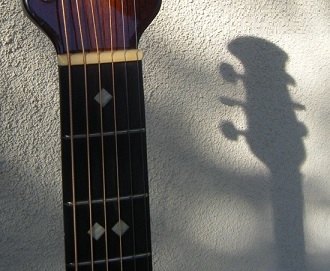 Joined: February 2016 Posts: 1846
Location: When?? | +1 on the Shooter's Choice with the injector. A little dab'll do ya and it's great stuff to have around for other uses as well. |
|
|
|
Joined: November 2002 Posts: 3647
Location: Pacific Northwest Inland Empire | Thanks for the suggestion and product endorsement. I will put it on my shopping list. |
|
|
|
Joined: November 2002 Posts: 3647
Location: Pacific Northwest Inland Empire | Well, at least the tuners are looking better.
(finished tuners 1- smaller image.jpg)
(finished tuners 4- smaller image.jpg)
Attachments ----------------
finished tuners 1- smaller image.jpg (86KB - 0 downloads)
finished tuners 4- smaller image.jpg (66KB - 0 downloads)
|
|
|
|
Joined: March 2002 Posts: 15674
Location: SoCal | Heck, you practically have the entire guitar done!
|
|
|
|
Joined: November 2002 Posts: 3647
Location: Pacific Northwest Inland Empire | Thanks for the optimism, Paul.
My date with the scraper is arriving soon.
Perhaps, in the current set of expectations, I also need to construct a long-throat clamp for that fissure below the bridge. Needs to be about a foot long to reach the end of the body. Heck, probably gonna need one about 9 inches, too. Gots lots of 3/4-inch square tube laying around from all my pedalcraft fabrications- piece-o'-cake. |
|
|
|
Joined: November 2002 Posts: 3647
Location: Pacific Northwest Inland Empire | Got a response from Ovation Customer Service. No label graphics available. They gave me some interesting history, related to that issue, also.
"Additionally, in the mid/late 1990's, in the early days of internet sales and businesses selling online, we discovered a large quantity of counterfeit guitars being offered for sale-coupled with weekly calls for "replacement" labels and headstock appliques that we decided we would not produce or provide reprints for any requests for these "parts" as it was obvious to us that most of the requests were to correct these counterfeit guitars."
So, the search will continue. |
|
|
|
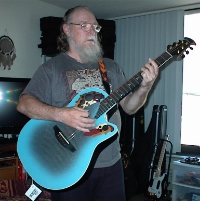 Joined: September 2006 Posts: 10777
Location: Keepin' It Weird in Portland, OR | Yeah.... Bullshit.
Because during THIS century, John Budny send me stickers and tuners and saddles and preamps (no rosettes).
Did you tell them that you probably know more about Ovation history than they do?
|
|
|
|
Joined: October 2014 Posts: 270
| He sent me a rosette. |
|
|
|
Joined: November 2002 Posts: 3647
Location: Pacific Northwest Inland Empire | I understand what “not available “ means. Whether the current support crew is accurate or even motivated is conjecture, at best. As Blanche DuBois opined, “I depend on the kindness of strangers.” |
|
|
|
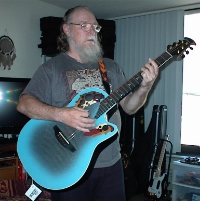 Joined: September 2006 Posts: 10777
Location: Keepin' It Weird in Portland, OR | Yeah. I am not trying to be rude to them.
They probably just don't HAVE all of the stuff that JB had.
Sadly, a bunch of stuff went into that dumpster.
|
|
|
|
Joined: November 2002 Posts: 3647
Location: Pacific Northwest Inland Empire | S'OK. Jonmark is probably right, "We are nerds". Albeit, passionate & devoted. The world keeps spinnin' & times (and resources) change. I don't need to ask often if we're having fun, yet. That's cool. |
|
|
|
 Joined: May 2006 Posts: 4231
Location: Steeler Nation, Hudson Valley Contingent | Yep! Gonna be checking in on this one regularly.... Apparently I'm a nerd too. |
|
|
|
Joined: November 2002 Posts: 3647
Location: Pacific Northwest Inland Empire | Thanks for swelling the gallery, Patch! This is going to be a cooperative enterprise, & any conjecture, wild guesses, or ***-forbid, real science & accurate facts, are welcomed & expected. I will be the chief-cook-&-bottlewasher & attempt to cobble together a decent restoration of the GCDB.
So then, more progress. Got the top scraped & found several areas in need of significant repair. Answered a few of the prior concerns, i.e., the rosette was inlaid in the soundboard, and there was no repair to the top, before that awful blue goo was slathered onto the soundboard. Actually, I am fortunate Ovation put a thick epoxy topcoat on their instruments. The paint removal required a little less, let's term it "precision", to accomplish the task. I have discovered the binding was lost at the bottom of the guitar, and based on the backlighted photo, it appears there is no kerfing in that vicinity, though a lot of (probably epoxy) filler was used to secure the bottom edge of the soundboard to the bowl. That may be a challenge to remedy, after the top is cleated & flattened, since there won't be anything to reglue the top to, or glue the replacement binding onto.
OK, enough already. Here's some current photos:
(Scaping- treble side- smaller image.jpg)
(Scraped top 1- smaller image.jpg)
(scraped soundhole- smaller image.jpg)
(scraped fissure- smaller image.jpg)
(lighted fissure 3- smaller image.jpg)
Attachments ----------------
Scaping- treble side- smaller image.jpg (92KB - 0 downloads)
Scraped top 1- smaller image.jpg (86KB - 0 downloads)
scraped soundhole- smaller image.jpg (67KB - 0 downloads)
scraped fissure- smaller image.jpg (88KB - 0 downloads)
lighted fissure 3- smaller image.jpg (55KB - 0 downloads)
|
|
|
|
Joined: March 2002 Posts: 15674
Location: SoCal | You going to hydrate that thing and see if the wood closes up? |
|
|
|
Joined: November 2002 Posts: 3647
Location: Pacific Northwest Inland Empire | It's a pretty wide crack. I will soak the top, below the bridge, and determine how much it will close, and also how flat I can get the soundboard. It will probably not move much, since it is still glued to the crossbrace. Maybe, put a clamp across the lower bout & see if that might close it up while its being reglued. It will never be perfect, but it IS the original top, so I will do whatever I can to salvage it.
Gonna start making my long-throat clamps tomorrow.
|
|
|
|
Joined: October 2014 Posts: 270
| At some point you're going to have to make a decision as to whether you want a playable guitar or a nice-looking and playable guitar. Personally, I'd go for playable and decide later if I want to venture into re-topping territory. Guitars don't have to be pretty. Ask Willie Nelson.
In any case, I'm looking forward to following your project.
Edited by BCam 2022-01-13 8:33 AM
|
|
|
|
Joined: March 2005 Posts: 12759
Location: Boise, Idaho | Looks like it had a pretty rough life, probably dropped on the end at least once, or possibly used as a club, hopefully in self-defense. Too bad someone tried to hide the damage with that hideous blue paint. I'd like to see if you can save the top. You could make it look a lot better than Willie Nelson's. |
|
|
|
Joined: November 2002 Posts: 3647
Location: Pacific Northwest Inland Empire | Thanks Guys! I have to agree with BCam, at this point. I'm pretty sure this will be a nice-playing, great-sounding instrument, after whatever restoration efforts are accomplished. As for Willie Nelson, he gets a lot of notoriety with Trigger, and reflects the dedication, and probably the adventures, of his marvelous career. There are a couple of videos at Stew-Mac of Dan Erlewine's brother doing the maintenance on Trigger. I'm sure the Martin Guitar company has offered Willie a replacement several times!
Back to the subject, next referendum: Should the bottom brace be pried loose, to see if that crack can be reduced? I was thinking of carefully cleaning up the edges of the fissure and possibly gluing in a splinter of spruce. It isn't like I am going to be fooling anyone into believing this is a new instrument, anyway. |
|
|
|
 Joined: June 2012 Posts: 2332
Location: Pueblo West, CO | I'd glue in a splinter of spruce rather than remove the brace.
For the missing kerfing, I'd order some kerfing from Stewmac and glue that into place. |
|
|
|
 Joined: October 2005 Posts: 4065
Location: Utah | My vote is to embrace the aesthetics of the hard life this guitar has had. Make it structurally secure and easy to play. I wouldn't try to cover up the wear and tear too much. Dan's advice sounds good to me, splice in a bit of spruce to the open crack and repair the kerfing. Rehab the neck as required. |
|
|
|
Joined: November 2002 Posts: 3647
Location: Pacific Northwest Inland Empire | Thanks for the input. Yep, I think the splinter option is the best. I don't see the neck as requiring refretting, so that's a relief. The wires are a trifle thin, but still functional. And, the rosette from Dave, routed through Al, just arrived. Thank you so much for that contribution. One less dilemma to resolve. Probably will need to shim under it a bit, but it should fit very nicely!
(new rosette- smaller image.jpg)
Attachments ----------------
new rosette- smaller image.jpg (93KB - 0 downloads)
|
|
|
|
Joined: November 2002 Posts: 3647
Location: Pacific Northwest Inland Empire | Yes, Dan, I have some kerfing in the supply closet. The trick will be gluing it in. I guess, after the top is fixed & the binding channel is recut.
So, back to the welding shop to make my deep-throat clamps. |
|
|
|
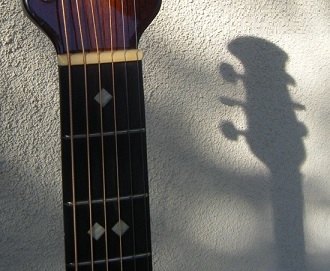 Joined: February 2016 Posts: 1846
Location: When?? | That backlighted shot looks like something from a 70's sci-fi movie.. but the top wood looks better than I thought it would. Like squeezing the air out of one end of a balloon it can only go to the other end, so too much hydrating and compressing could take an unexpected toll elsewhere. Experimenting with the splinter patch to start with may behoove the future since if you can't get one to fit and match to your liking you can always scrap the plan and be no worse off than back to square one (sorry to dwell on the obvious).
PS thought-- On re-examination of the top wood appearance, I kinda like the look of it with the blue streaks and chips the way it is. Sand smooth and shoot with Eastwood. My mom the artist used to do that with painted antique furniture and most of her pieces ended up to be quite pretty and unique for those who are into such an appearance.
Edited by Love O Fair 2022-01-13 3:01 PM
|
|
|
|
Joined: November 2002 Posts: 3647
Location: Pacific Northwest Inland Empire | Dwelling on the obvious is what I need. Maintaining some perspective is what I depend on from my esteemed colleagues. Much appreciated! |
|
|
|
Joined: March 2002 Posts: 15674
Location: SoCal | This is so cool...... |
|
|
|
Joined: November 2002 Posts: 3647
Location: Pacific Northwest Inland Empire | It sure is, Paul. I am having a blast with this project. The input has been great, and nobody is directing me to the local landfill with my prize! |
|
|
|
Joined: November 2002 Posts: 3647
Location: Pacific Northwest Inland Empire | Cut my thumb on a drillbit last night. Might have to take the day off. Probably won't save me from the Friday vacuuming, though! |
|
|
|
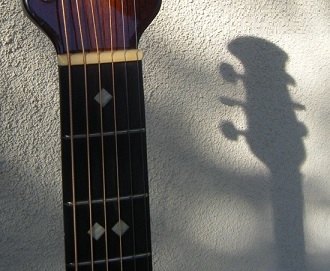 Joined: February 2016 Posts: 1846
Location: When?? | Condolences to the thumb.. and don't forget that spot behind the sofa. |
|
|
|
Joined: November 2002 Posts: 3647
Location: Pacific Northwest Inland Empire | Testimony to good recuperative powers & persistence. Pressing on!
(Clamp 5- smaller image.jpg)
Attachments ----------------
Clamp 5- smaller image.jpg (62KB - 0 downloads)
|
|
|
|
Joined: November 2002 Posts: 3647
Location: Pacific Northwest Inland Empire | And I determined why the bottom edge of the bowl glows. The kerfing is actually impregnated fiberglass cloth, bonding the bowl to the top. Without the binding in place, light shines through the fiberglass strip. It does look like some of it is missing, likely from falling on its butt one-too-many-times. So, I might be able to paste in a small section of cloth & resin to provide a surface for the binding channel, at least.
That crossbrace noted in the backlighted photo is only a hair-thin strip of wood that has puckered & separated from the soundboard about 1 inch from the right side of the crack in the top. That entire strip can't be providing much support, but it also shouldn't interfere too much with the crack repair. I suppose the idea of a strip of wood crossways was to limit the separation in the soundboard grain structure.
Edited by seesquare 2022-01-14 11:05 PM
|
|
|
|
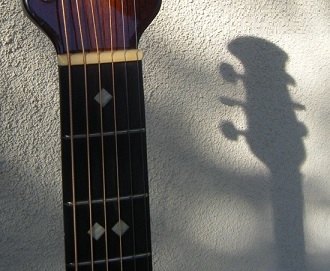 Joined: February 2016 Posts: 1846
Location: When?? | @seesquare - >>>With the A-918 serial #, the guitar was apparently made in late 1968.<<<
This build is extra interesting for me in that you and I both took delivery of a 1968 Deluxe during the same week 54 years later.. though mine is not a Campbell (see recent sell listing from Standingovation). It's nice to be able to see some of the guttery of how these were built since this is the first one I have owned from the A-series. Anyway.. mine is serial number A 042, so assuming the numbering sequence stayed chronological when it went into the Campbell models, mine must have been built around July/August.. and your's as late as November (dpending on how many A-series were built overall). The number stamped inside the bowl on the neck heel for mine is 3013.. but still not certain what that means. Does yours have a number on there?
Edited by Love O Fair 2022-01-15 2:29 AM
|
|
|
|
Joined: November 2002 Posts: 3647
Location: Pacific Northwest Inland Empire | Nope. Clean-as-a-whistle.
(neck block 3- smaller image.jpg)
Attachments ----------------
neck block 3- smaller image.jpg (93KB - 0 downloads)
|
|
|
|
Joined: March 2002 Posts: 15674
Location: SoCal | Looking at the pics of the GCDB, I thought that something looked slightly off on the neck inlays. Going back to old pictures of GCDB's, including mine (now residing in Iowa), I realized there there are no inlays at the 17th fret. There should be 2 diamond inlays there. Found a picture and you can see what I mean.
I have learned that some interesting variations came out of the factory back in the 60's and 70's......
(GC_Deluxe_Balladeer_04.jpg)
Attachments ----------------
GC_Deluxe_Balladeer_04.jpg (68KB - 0 downloads)
|
|
|
|
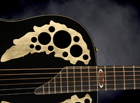 Joined: October 2012 Posts: 1077
Location: Yokohama, Japan | Off to a great start seesquare (except the thumb injury, of course)! Is it just me or does that neck block look really unusual? |
|
|
|
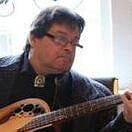 Joined: August 2002 Posts: 633
Location: Ottawa, Ontario, CANADA | Hello, seesquare,
Your persistence through injury is very encouraging to me, and as of this writing, my injured 3rd finger is about 95% healed, and I should be able to play when my friend, Bruce arrives again this week. I am not a luthier/repairman at all, and seeing all the great work that the BFLG does is fascinating, for sure. The neck block is a bit of a mystery to me, too, but, alas, I know nothing about such things, as I said. I rarely get to see the inside of an Ovation, except for this forum. Your bandage is much tidier than mine was, and is a badge of honour for your hard work thus far.
Mike S.
Ottawa, ON.,
CANADA.
|
|
|
|
Joined: November 2002 Posts: 3647
Location: Pacific Northwest Inland Empire | Thanks Mike. Yeah, I seemed to bleed a lot more out of the top of my thumb. It has knitted together well & I have been working on the clamps to glue in the patch under that crevice below the bridge. I need to revamp my design to have a taller clamp, cuz the 12" throat, with only a 3-1/2" opening, doesn't make it into the guitar. Had to cut off about 3"-of-the-12" to clear the back edge of the soundhole. Have made some cauls to align the patch piece & flatten out the distortion in the crack edges.
As to the shape of the neck block- yep, its different than the others I've seen.
Y'know, Paul, you have a keen eye. I had to go look at the guitar. Yerright, it doesn't have inlays at the 17th fret. It would be interesting to know if they were left off, due to later manufacture date.
Also, I managed to remove that thin cross rib intact. Scraped off the old glue & am flattening it out. I will glue it back in after I get the center patch repair done.
Edited by seesquare 2022-01-15 3:26 PM
|
|
|
|
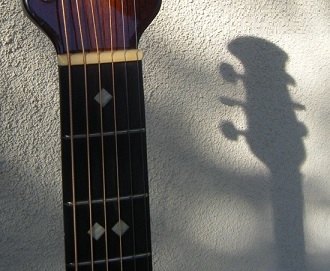 Joined: February 2016 Posts: 1846
Location: When?? | I see that it arrived with an upper strap button.. but my standard'68 DB does not have one.. nor does it appear that Paul's GC does. Some pics of others do, and some don't. You suppose those that do were owner-added after production.. or did the factory only put them on some?? (I am going to install one upon the next string change.) As for comparing neck inlays on the GC Deluxe vs. the standard Deluxe, my standard has one on the 15th fret and no inlays beyond that. Pandora II's inlays appear like something of a hybrid between the two.
Edited by Love O Fair 2022-01-15 4:46 PM
|
|
|
|
Joined: March 2002 Posts: 15674
Location: SoCal | Owner added. I put one on mine/Howard's...... |
|
|
|
Joined: November 2002 Posts: 3647
Location: Pacific Northwest Inland Empire | Made another clamp. This one is 7” tall, with a 12” throat. Should get all the way to the end of the bowl from the sound hole. Work on the splint patch tomorrow. |
|
|
|
 Joined: June 2012 Posts: 2332
Location: Pueblo West, CO | seesquare - 2022-01-14 8:53 PM
And I determined why the bottom edge of the bowl glows. The kerfing is actually impregnated fiberglass cloth, bonding the bowl to the top. Without the binding in place, light shines through the fiberglass strip. It does look like some of it is missing, likely from falling on its butt one-too-many-times. So, I might be able to paste in a small section of cloth & resin to provide a surface for the binding channel, at least.
Yes. In the early bowls, the kerfing was molded fiberglass, not unlike the suspension ring used later on Adamas.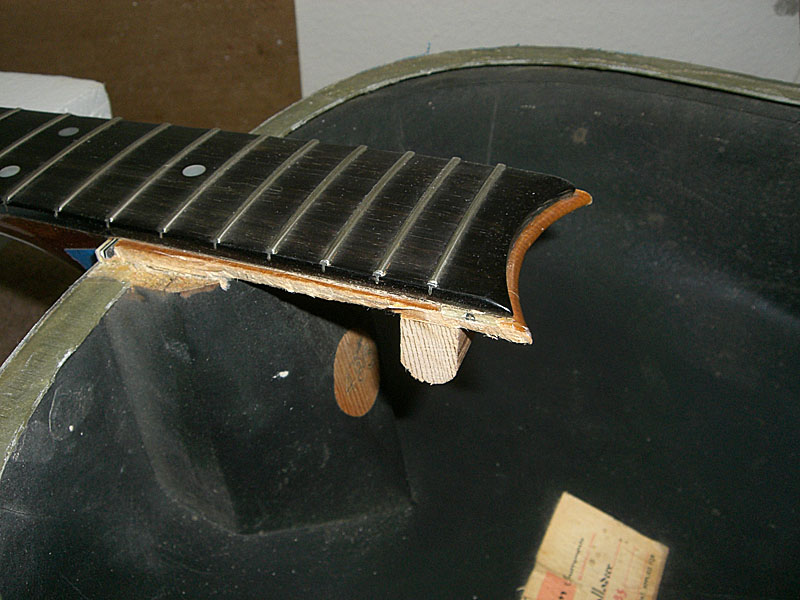
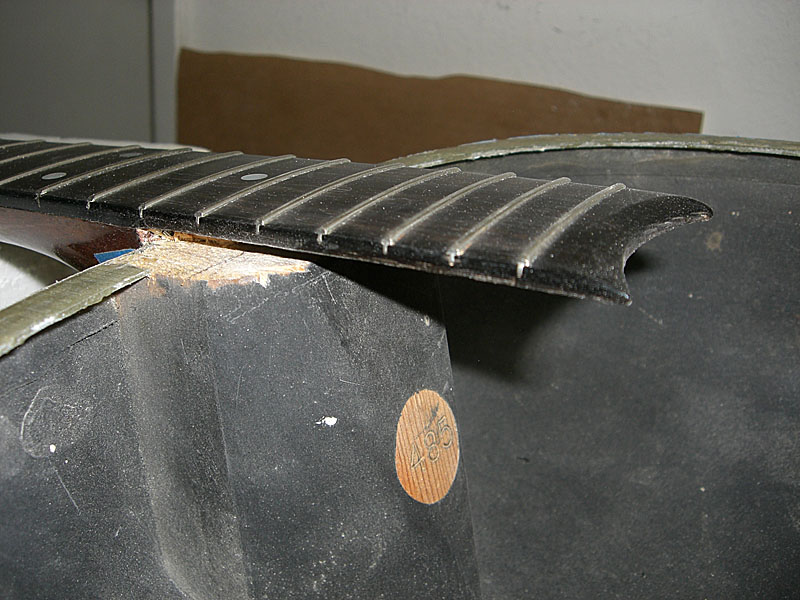
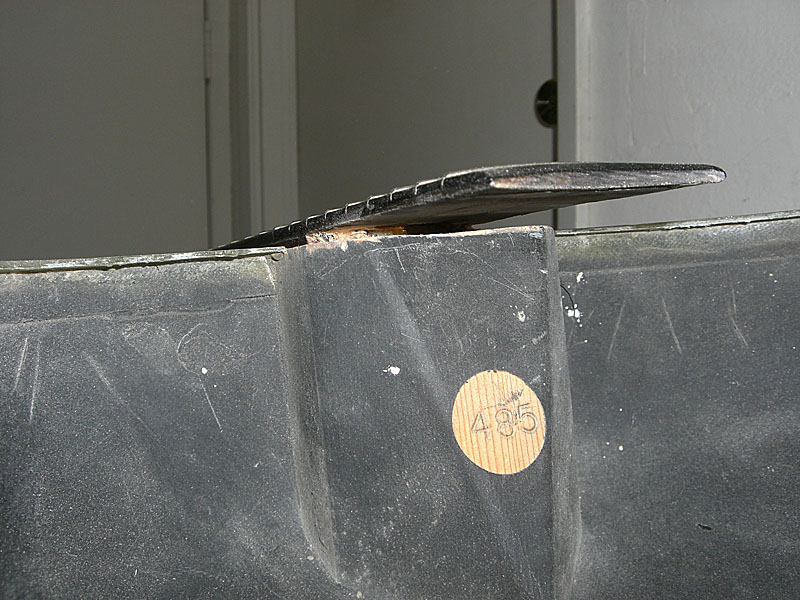
Edited by DanSavage 2022-01-16 12:15 AM
|
|
|
|
Joined: November 2002 Posts: 3647
Location: Pacific Northwest Inland Empire | Wow, that is some archive you have there, Dan. Thanks for the info. Interesting to evidence the evolution of materials & building techniques, as the product line was developed. I am currently humidifying the guitar to determine the extent the crack will resolve. I think I will have to clean the edges & glue in the splint, before applying the repair strip below the bridge.
(mondoclamp- smaller image.jpg)
Attachments ----------------
mondoclamp- smaller image.jpg (89KB - 0 downloads)
|
|
|
|
Joined: November 2002 Posts: 3647
Location: Pacific Northwest Inland Empire | I see the crack closed up a bit with the hydration experience. I'm going to forego the splint scenario, for now. Damn the torpedoes........... |
|
|
|
Joined: November 2002 Posts: 3647
Location: Pacific Northwest Inland Empire | Crossing my fingers. Wish me luck!
(patch glued 1- smaller image.jpg)
(patch glued 2- smaller image.jpg)
Attachments ----------------
patch glued 1- smaller image.jpg (66KB - 1 downloads)
patch glued 2- smaller image.jpg (62KB - 0 downloads)
|
|
|
|
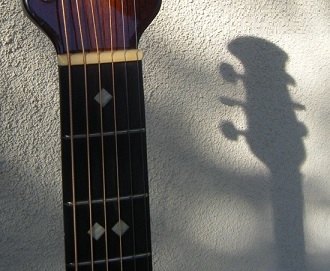 Joined: February 2016 Posts: 1846
Location: When?? | And to think I considered patching dry rot around the laundry room plumbing to be a teetering endeavor. Mere child's play compared to the great clamp rig you fabricated there! Your pieces & parts ingenuity gets better with every project and post. |
|
|
|
Joined: November 2002 Posts: 3647
Location: Pacific Northwest Inland Empire | Daily progress report. The center fissure has been significantly reduced (yippee-skippy!), and filled with some epoxy. Will scrape it flat tomorrow. put a patch under the crack near the soundhole on the treble-side. Replaced the binding at the fret extension arch. Currently, gluing in a patch under the bass-side lower bout edge. I have decided to go with wood bindings- mahaogany, walnut & basswood. I was tempted to get some herringbone strips, but that would be too "busy".
(left lower crack repair 1- smaller image.jpg)
Attachments ----------------
left lower crack repair 1- smaller image.jpg (99KB - 1 downloads)
|
|
|
|
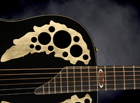 Joined: October 2012 Posts: 1077
Location: Yokohama, Japan | WOW! Maestro seesquare that is impressive work. Love your homemade clamps. Hope you keep that retro-look because in this case it's not just a 'look'! Beautiful!
Edited by arumako 2022-01-18 7:56 PM
|
|
|
|
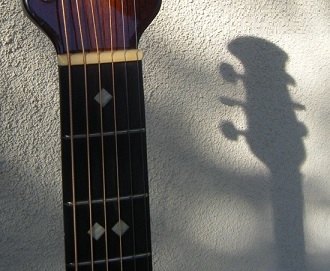 Joined: February 2016 Posts: 1846
Location: When?? | What is the wire going into the sound hole? |
|
|
|
Joined: November 2002 Posts: 3647
Location: Pacific Northwest Inland Empire | I guess that's the concensus, Ken- "warts-&-all". Been drop-filling 6 cracks in the top today with Superglue (yeah, the actual brand). Slow process, but it will eventually get the top smoothed out. Probably be at this for a couple of days, I imagine. Also found the tip of the upper, bass-side x-brace needed a spot of glue, so that got done.
(dropfill 1- smaller image.jpg)
Attachments ----------------
dropfill 1- smaller image.jpg (85KB - 0 downloads)
|
|
|
|
Joined: November 2002 Posts: 3647
Location: Pacific Northwest Inland Empire | Uh, yeah, the wire. That is a small droplight I use to help line up the gluing cauls & clamps. There is also a mirror in there that is about 7x8-inches, unfolded. |
|
|
|
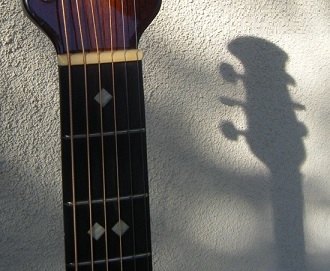 Joined: February 2016 Posts: 1846
Location: When?? | How are the nicks and nacks on the bowl? I remain curious as to how well a shiny bowl can be buffed out when any abrasive and/or otherwise intrusive actions may have to be taken upon said nicks and nacks. |
|
|
|
Joined: November 2002 Posts: 3647
Location: Pacific Northwest Inland Empire | Pretty much got the cracks filled & went over the top with some 150-grit sandpaper. This is probably as good as it gets, related to the oxymoronic "relieved distress". I will start the removal of the binding & cleaning up the channels soon. Another excuse to go to the hardware store- need some new router bits for both the 1/8" Dremel & the 1/4" Craftsman.
(sanded top 2- smaller image.jpg)
(sanded top 1- smaller image.jpg)
(bottoms up view- smaller image.jpg)
(side view 2- smaller image.jpg)
Attachments ----------------
sanded top 2- smaller image.jpg (67KB - 0 downloads)
sanded top 1- smaller image.jpg (59KB - 0 downloads)
bottoms up view- smaller image.jpg (55KB - 0 downloads)
side view 2- smaller image.jpg (66KB - 0 downloads)
|
|
|
|
Joined: November 2002 Posts: 3647
Location: Pacific Northwest Inland Empire | Sorry, forgot to address the shiny bowl issue. I'm not sure how to approach any refurbishment on the scars, gouges & dings. The Mr. Clean Magic Eraser did a good job on the white paint scuffs, at least. I have quite a bit of work to do, before the bowl finish rises to the top of the restoration agenda. |
|
|
|
Joined: November 2002 Posts: 3647
Location: Pacific Northwest Inland Empire | Managed to get a few images inside the bowl of the gluing repairs. Those little cameras are pretty tricky! There are a total of 3 patches- center-below-bridge, treble-side-by soundhole, & bass-side-lower-bout.
Edited by seesquare 2022-01-19 4:18 PM
(bass x-brace end- smaller image.jpg)
(soundhole patch 2- smaller image.jpg)
Attachments ----------------
bass x-brace end- smaller image.jpg (20KB - 0 downloads)
soundhole patch 2- smaller image.jpg (16KB - 0 downloads)
|
|
|
|
Joined: November 2002 Posts: 3647
Location: Pacific Northwest Inland Empire | Glued in the lower cross strip in the bottom end (I hesitate to call it a brace, it's so thin). Used a couple of my welding magnets & flat steel strips to clamp it in place. Fabricated a new saddle- boy, that is REALLY time-consuming! Since it is black, I surmise I am committed to making the nut black, also.
That's about it for the day. Makin' progress.
Addendum: I'm not real sure what the saddle material is. It doesn't smell like bone, and had a faint odor like rubber, at times. Is that micarta? There is no grain structure to it, either. Apparently, has some flexibility, but it isn't soft. Needs some more finishing & polishing, to-be-sure.
Edited by seesquare 2022-01-20 9:02 PM
(interior crossbrace gluing- smaller image.jpg)
(new saddle 1- smaller image.jpg)
(saddle & bridge 1- smaller image.jpg)
(new saddle 4- smaller image.jpg)
Attachments ----------------
interior crossbrace gluing- smaller image.jpg (78KB - 0 downloads)
new saddle 1- smaller image.jpg (92KB - 0 downloads)
saddle & bridge 1- smaller image.jpg (84KB - 0 downloads)
new saddle 4- smaller image.jpg (98KB - 0 downloads)
|
|
|
|
Joined: November 2002 Posts: 3647
Location: Pacific Northwest Inland Empire | So, whaddya think? Does this look acceptable for the replacement? I have limited graphics expertise, so this is essentially a cut-&-paste job.
On other fronts, the peghead scars & dents have been addressed, with a bit of Truoil to touch up the sanded areas. 3 coats, so far. I will see if I can iron out a few of the dents in the neck, itself. A little hot steam may do wonders on a few of those dents.
(new label 1- smaller image.jpg)
Attachments ----------------
new label 1- smaller image.jpg (52KB - 0 downloads)
|
|
|
|
Joined: March 2002 Posts: 15674
Location: SoCal | Lookin' good Billy Ray.......
Edited by moody, p.i. 2022-01-21 11:48 PM
|
|
|
|
Joined: November 2002 Posts: 3647
Location: Pacific Northwest Inland Empire | Feeling good, Louis! |
|
|
|
Joined: November 2002 Posts: 3647
Location: Pacific Northwest Inland Empire | So, Esteemed Colleagues, and others with an opinion, what approach & process would you suggest in refinishing the bowl? I'm thinking a careful wet-sanding with about 600->1200-grit paper, then shoot it with some gloss black enamel. Not sure lacquer would mate well with the present finish. Some of the scratches are bordering on gouges, so some moderate filling may be required. There is evidence the bowl was repainted, at some time, as the sides are dead-smooth & truly shiny, while the bottom surface has a slight orange-peel pattern, like it was shot with a rattle can.
Addendum: Yes, there is a small hole in the upper, bass-side bowl area. I have no idea what that was designed to do. I may try to fill it, as the whole bowl is being refinished, anyway.
Edited by seesquare 2022-01-22 2:24 PM
(lower bowl scuffs- smaller image.jpg)
(upper bowl scuffs- smaller image.jpg)
(whole bowl scuffs- smaller image.jpg)
Attachments ----------------
lower bowl scuffs- smaller image.jpg (75KB - 0 downloads)
upper bowl scuffs- smaller image.jpg (71KB - 0 downloads)
whole bowl scuffs- smaller image.jpg (74KB - 0 downloads)
|
|
|
|
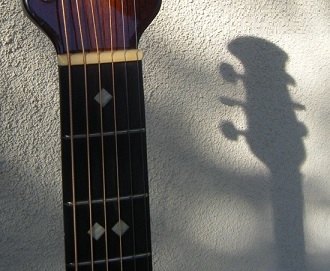 Joined: February 2016 Posts: 1846
Location: When?? | It seems the label looks as good as any you're going to find. Maybe you could experiment with different types of paper if you're interested in the aged look or something more custom than straight white. I am a paper collector, so let me know if you want me to ship you some of anything I... may... have here to suit. By what has been seen from your bench in the past I'm sure we all have faith that you and your skills can prep the bowl to a very nice surface. What type of spray rig do you have to use at your place? Recall when Patch sent a guitar to an auto body shop for a finish-up. My parents also once had a refrigerator shot at a body shop for a custom color and high gloss which turned out perfect to what they wanted. Just a thought should you be accepting of outside hands on your project.
Edited by Love O Fair 2022-01-22 3:14 PM
|
|
|
|
Joined: November 2002 Posts: 3647
Location: Pacific Northwest Inland Empire | Thanks for the input, Al! In keeping with the spirit of the "primal" BFLG, I am economizing on everything, as evidenced by the crude tools & fabrications. I expect I will shoot the bowl with a good grade of rattle can gloss black. I wish I did have a good paint rig & dedicated spray booth! I just close up the workspace overnight, let all the dust settle, then shoot the 1st coat, first-thing-in-the-morning. Leave it at least 24 hours, sand it out, and recoat. Repeat 'til I'm happy with the finish. Then, not touch it for about a week. Same plan for the top, too. Except that will be a clearcoat. Haven't decided if it will be a gloss or semi-gloss, at this juncture.
BTW, the clothes iron & wet rag did a pretty decent job of lifting the dents in the neck. I have drop-filled a few of the more recalcitrant dings, leveled it out with 320 emery cloth, and now working it over with some 1200-grit, dry. Should be applying the clearcoat pretty soon. Another aspect that gets redone, then not touched for a while, 'til the finish hardens up pretty well.
As y'all can see, I'm procrastinating on the binding replacement.
Oh, and thanks for the paper suggestion. SWMBO is a greeting & holiday cardmaker, of an accomplished nature, and definitively the resident artist in this abode. She has almost an unlimited variety of paper goods to choose from. Too bad she couldn't reproduce the Ovation logo for the label.
Edited by seesquare 2022-01-22 8:40 PM
|
|
|
|
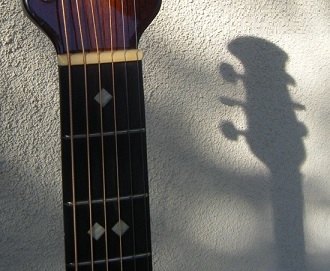 Joined: February 2016 Posts: 1846
Location: When?? | "recalcitrant" - Dang. Had to look that one up. |
|
|
|
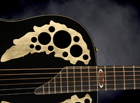 Joined: October 2012 Posts: 1077
Location: Yokohama, Japan | seesquare - 2022-01-22 10:33 AM
I expect I will shoot the bowl with a good grade of rattle can gloss black. I wish I did have a good paint rig & dedicated spray booth! I just close up the workspace overnight, let all the dust settle, then shoot the 1st coat, first-thing-in-the-morning. Leave it at least 24 hours, sand it out, and recoat. Repeat 'til I'm happy with the finish. Then, not touch it for about a week. Same plan for the top, too. Except that will be a clearcoat. Haven't decided if it will be a gloss or semi-gloss, at this juncture.
Making really good progress seesquare! Thanks for sharing. I'm no finishing wizard, but polyurethane car paint has worked really well for me (especially on fiberglass parts) and it can be polished to a sparkly sheen with automotive waxing compounds. I know what you mean about keeping your work within a BFLG-ish budget; but IMHO, if you can get access to air brushing equipment that would really increase your chances of succeeding with a gloss finish. Gloss or not, she's gonna be a killer restoration! |
|
|
|
Joined: November 2002 Posts: 3647
Location: Pacific Northwest Inland Empire | Okay Ken, I might be open to investing in some airbrush equipment. As my sainted father always instructed, "There's no substitute for the right tool."
Do you have any suggestions or recommendations? I do have a 3-gal compressor for an air source. In keeping with the "BFLG-ish" budget constraints, of course!
Edited by seesquare 2022-01-23 6:45 AM
|
|
|
|
 Joined: June 2012 Posts: 2332
Location: Pueblo West, CO | Another possibilty for the bowl re-spray is Eastwood 2K Urethane Gloss Black in a rattle can. At $29.99 per can it's a little pricey, but you end up with a true catalyzed finish like what was used originally. It willl be a lot tougher finish than gloss enamel. 
|
|
|
|
Joined: November 2002 Posts: 3647
Location: Pacific Northwest Inland Empire | Thanks for the suggestion, Dan. Actually, I am getting a basic airbrush, single-action, siphon-bottle, and the necessary parts to connect to my little compressor. Been watching several Youtube videos, thus far, and gotten a pretty good idea what I'm in for. I will practice & experiment a bit with different paints, pressures, & thinning before shooting the bowl, proper. I should be able to find some decent black gloss urethane to use, if that gives a tougher & more durable finish. When you really evaluate where a guitar gets the most " normal abuse", it's probably on the back, next to your body, hence "buckle rash".
So, put a couple of coats of Truoil on the neck, and have plugged that little hole on the bowl with some epoxy. Got a fresh batch of 500-weight wet-or-dry to sand out the scratches on the bowl, and planning on a couple of hours of messy dermabrasion.
(bowlhole- smaller image.jpg)
Attachments ----------------
bowlhole- smaller image.jpg (91KB - 0 downloads)
|
|
|
|
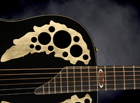 Joined: October 2012 Posts: 1077
Location: Yokohama, Japan | seesquare - 2022-01-23 9:38 PM
Actually, I am getting a basic airbrush, single-action, siphon-bottle, and the necessary parts to connect to my little compressor. Been watching several Youtube videos, thus far, and gotten a pretty good idea what I'm in for.
You're on the move there seesquare; but yeah, for the kind of work required on a guitar finish, you don't need anything complicated or super powerful - sounds like you're well on your way. Since you were saying some of the gouges are deep, you might want to use the rattle can black poly that Dan suggests to fill the gouge areas; sand them down nicely and use the air brush for your final gloss coats. Sometimes even gloss black can be tricky to color match; so you might need to airbrush the whole bowl; but you all have all kinds of excellent polyurethane products in the States including waxing compounds; so you're in good shape! Carry on, carry on! |
|
|
|
Joined: November 2002 Posts: 3647
Location: Pacific Northwest Inland Empire | Yes, the whole bowl is getting refinished. I was planning on priming the surface to fill some minor scratches & provide a better foundation for the gloss coats.
This is the 1st session of remediation. Have some work left to do. 500-grit is slow, but effective. I can determine where the repainting occurred, and where the original fiberglass structure lies.
Edited by seesquare 2022-01-24 11:21 AM
(bowl sand 1- smaller image.jpg)
(bowl sand 2- smaller image.jpg)
(bowl sand hole 1- smaller image.jpg)
Attachments ----------------
bowl sand 1- smaller image.jpg (70KB - 0 downloads)
bowl sand 2- smaller image.jpg (63KB - 0 downloads)
bowl sand hole 1- smaller image.jpg (47KB - 0 downloads)
|
|
|
|
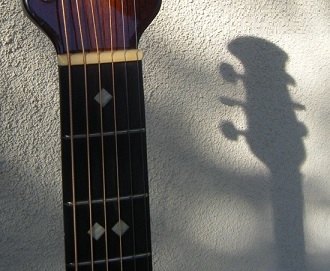 Joined: February 2016 Posts: 1846
Location: When?? | Looking at the photo on the hole patch, the bowl looks like textured lyrachord. I realize that it isn't, and wondered if it was because of the intensity of the camera light.. thinking maybe they all look like that under intense light.. so I shined a bright light on my shiny and saw nothing alike. Now I see that your next post post came in while I was typing [now editing]... the bowl was painted? Is that what we were seeing there? Orange peel?
@arumako - >>>but you all have all kinds of excellent polyurethane products in the States including waxing compounds<<<
Sorry a bit topical-astray.. but that's the part I don't get. Not that I doubt you. At all. It is what it is. And for importing your own stuff we understand how you use sunglasses with suave and debonair charm on the gushing gate agent at LAX who thinks you're a rock star with heavy luggage. I'm just wondering why street beggars like me cannot easily acquire excellent thane & wax there. Can you order specific product from the USA online.. or is it not allowed to import? Heck, let me know what you need and I will gladly FedEx it inside a caramel fudge cake.
Edited by Love O Fair 2022-01-24 11:56 AM
|
|
|
|
Joined: November 2002 Posts: 3647
Location: Pacific Northwest Inland Empire | After another coupla-hours of sanding, I got the repaint coating eradicated. So, what you see now is the 500-grit surface of the original fiberglass. There are still a few speckles left, but the scratches have been sanded out, and the primer will fill those specks, I'm sure.
(sand bowl 1- smaller image.jpg)
(sand bowl 2- smaller image.jpg)
(sand bowl 4- smaller image.jpg)
Attachments ----------------
sand bowl 1- smaller image.jpg (51KB - 0 downloads)
sand bowl 2- smaller image.jpg (48KB - 0 downloads)
sand bowl 4- smaller image.jpg (69KB - 0 downloads)
|
|
|
|
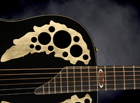 Joined: October 2012 Posts: 1077
Location: Yokohama, Japan | seesquare - 2022-01-24 6:26 AM
After another coupla-hours of sanding, I got the repaint coating eradicated. So, what you see now is the 500-grit surface of the original fiberglass. There are still a few speckles left, but the scratches have been sanded out, and the primer will fill those specks, I'm sure.
WOW seesquare! That is some excellent work! Looks really really good. With a surface like that, the primer is obviously going to take to its job effectively. With this kind of patience, you're definitely going to have a vintage "shiny" bowl! NICE!
Edited by arumako 2022-01-25 12:59 AM
|
|
|
|
Joined: December 2003 Posts: 852
Location: Canada | Wow what a labour of love. As someone who is totally not handy and who has to hire someone for the most mundane tasks I am in awe of the BFLG threads. Thanks for sharing the journey. |
|
|
|
Joined: November 2002 Posts: 3647
Location: Pacific Northwest Inland Empire | Thanks Guys! I'm really enjoying this project, & sharing my neurosis. As one of my colleagues in the behavioral health biz once demanded in a staff meeting, "Your clinical presentation case needs to have a high EQ, and a low KI." As we were intrigued, curious & befuddled, he spelled it out, That's Entertainment Quotient, and Knucklehead Index."
Hopeful, I am maintaining the criteria for high EQ.
So, today's progress. I removed the old, brittle binding & rerouted the channels. I have a 4-part wood-strip binding pattern to be installed- basswood, walnut, basswood & mahogany (inside-to-outside). I broke out my heated bender gizmo to do the initial contours for fitting the binding strips to the body. The trick is to not overstress the strips & have them break, before they get glued in. They are soaking overnight to get them pliable. Should be some fun at oh-dark-thirty tomorrow!
Also bought some black acrylic airbrush paint & clear topcoat, 2 kinds of thinners, & cleaner (which is apparently just rubbing alcohol in a small, fancy bottle). Assembled the parts- oil/H2O filter, brass nipple & quick-connector- to connect to my compressor, & still waiting for the airbrush kit to arrive.
BTW, that disaster at the bottom edge of the bowl is not as bad as it looks, really. The binding will sit in the routed channel & will hide all that glarp used to patch the historic bottom trauma. There will still be some old paint showing at the binding border, but it shouldn't be too awful (as I cross my fingers & gaze prayerfully skyward).
Edited by seesquare 2022-01-25 8:47 PM
(binding channel- full view- smaller image.jpg)
(binding channel- bottom- smaller image.jpg)
(binding channel- neck joint- smaller image.jpg)
(binding channel- width- smaller image.jpg)
(binding bender 1- smaller image.jpg)
(binding bender 2- smaller image.jpg)
Attachments ----------------
binding channel- full view- smaller image.jpg (87KB - 0 downloads)
binding channel- bottom- smaller image.jpg (73KB - 0 downloads)
binding channel- neck joint- smaller image.jpg (73KB - 0 downloads)
binding channel- width- smaller image.jpg (78KB - 0 downloads)
binding bender 1- smaller image.jpg (60KB - 0 downloads)
binding bender 2- smaller image.jpg (59KB - 0 downloads)
|
|
|
|
Joined: November 2002 Posts: 3647
Location: Pacific Northwest Inland Empire | As planned, got the wooden bindings bent & installed. Will wait a full day before unmasking the mess. I want that glue to be fully set up before yanking the tape off. Then, a bit of careful sanding & leveling, and I can work on shooting the bowl!
(binding taped 1- smaller image.jpg)
(binding taped pattern- smaller image.jpg)
Attachments ----------------
binding taped 1- smaller image.jpg (94KB - 0 downloads)
binding taped pattern- smaller image.jpg (88KB - 0 downloads)
|
|
|
|
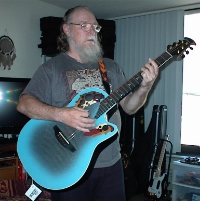 Joined: September 2006 Posts: 10777
Location: Keepin' It Weird in Portland, OR | Oooo! Nice binding.
|
|
|
|
 Joined: June 2012 Posts: 2332
Location: Pueblo West, CO | The binding looks real purdy... |
|
|
|
Joined: October 2014 Posts: 270
| I continue to be impressed with your work and the fact you don't let any grass grow under your feet. Your progress is inspiring. |
|
|
|
Joined: November 2002 Posts: 3647
Location: Pacific Northwest Inland Empire | Thanks again, Guys! I am a bit “driven”. I want to get the work done, but I also want to savor the experience. It has been a fairly busy two weeks. I just hope the critter plays well. It certainly will have better structural integrity and appearance. Next update in about 12 hours. I am an early riser. |
|
|
|
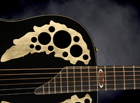 Joined: October 2012 Posts: 1077
Location: Yokohama, Japan | seesquare - 2022-01-25 10:26 AM
...I have a 4-part wood-strip binding pattern to be installed- basswood, walnut, basswood & mahogany (inside-to-outside). I broke out my heated bender gizmo to do the initial contours for fitting the binding strips to the body. The trick is to not overstress the strips & have them break, before they get glued in. They are soaking overnight to get them pliable. Should be some fun at oh-dark-thirty tomorrow!...
Woohoo! seesquare, you are a man on a mission! Love the understated look of the binding. Hope you don't mind my asking, but how long did you have to wait until the soaked binding was all dried out? I'm assuming you're super-gluing the bindings in place? Again, really nice work!
@LOF - Really appreciate your kindness! Wanted to get some of the Hysol 0151(#?) made famous on the BFLG by Dan just before the pandemic and called Loctite Japan, and they made it very clear with no uncertain terms that licenses to handle dangerous chemicals was needed to import any of their products here. Fortunately many of their super-glues are available now, but specialized products like their epoxies are (for them) not worth applying for the import license. Spray cans are flammable; so no retail outlet can ship directly to Japan - including Stewmac. All one can do is dream and wait (or try local substitute products)! |
|
|
|
Joined: November 2002 Posts: 3647
Location: Pacific Northwest Inland Empire | Thanks again, Ken. I used Elmer's WoodGlue to secure the wet bindings to the channels. It has worked out well in the past and holds well to the wood tops. The assembly is a bit tricky, as the top & sides of the guitar body have to be dry for the tape to hold. Getting the pieces to line up & lay evenly, initially, is kinda awkward. Like, a third hand would be nice!
As to getting supplies to Japan, are there restrictions on what you may receive privately? I understand the retail thing, due to governmental regulation.
(Elmer- smaller image.jpg)
Attachments ----------------
Elmer- smaller image.jpg (78KB - 0 downloads)
|
|
|
|
Joined: November 2002 Posts: 3647
Location: Pacific Northwest Inland Empire | Binding is installed. Looks pretty decent. Never underestimate the power of prayer! "Clean livin' & right thinkin'".
Needed to re-sand the bowl after installing the binding. It looks better, too!
Edited by seesquare 2022-01-27 4:09 PM
(body binding installed- smaller image.jpg)
(binding bottom edge- smaller image.jpg)
(binding bottom- smaller image.jpg)
(sanded bowl after binding- smaller image.jpg)
Attachments ----------------
body binding installed- smaller image.jpg (86KB - 0 downloads)
binding bottom edge- smaller image.jpg (99KB - 0 downloads)
binding bottom- smaller image.jpg (88KB - 0 downloads)
sanded bowl after binding- smaller image.jpg (57KB - 0 downloads)
|
|
|
|
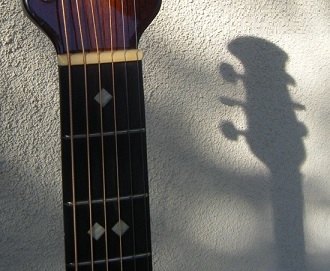 Joined: February 2016 Posts: 1846
Location: When?? | @seesquare - >>>"Clean livin' & right thinkin'<<<
Well I guess that counts me right out.. but..
I just looked back at photos of the original blue blunder, then back to current photos, and am beaming in pride to be of your association and EQ! Congratulations also on your new toolage acquisition.. and that's a very nifty heater bender gizmo, too! Looks somewhat McMurphy-ish.. like maybe something left over from your behavioral health lab. Did the eBay seller happen to mention if they were the one who painted it? Sure to be bowled over (pun intended) when they see your outcome of actual potential!
Edited by Love O Fair 2022-01-27 5:49 PM
|
|
|
|
Joined: November 2002 Posts: 3647
Location: Pacific Northwest Inland Empire | The instrument was sold by a pawnshop in San Diego. Who knows how many hands it has passed through?! And, thanks again for the positive vibes & compliments. I launch into these fiascoes & fly-by-the-seat-of-my-pants, hoping for a good outcome. "Luck is potential skill". |
|
|
|
Joined: March 2002 Posts: 15674
Location: SoCal | May fortune favor the foolish...... |
|
|
|
Joined: November 2002 Posts: 3647
Location: Pacific Northwest Inland Empire | So true, Dear Brother! Once more into the breach, eh wot?
And, it appears the work is grinding to a halt, for a few days. I am awaiting the arrival of the airbrush kit, due in about Thursday, Feb. 3, according to the tracking system. I am also looking for a suitable hardshell case for the refurbished critter. Probably easier to find a kidney donor these days. Just missed one that's headed to Canada, apparently. Has to be a deep-bowl (6-1/2" , and 42" inside-length, probably like the ones for Pacemakers. If anyone has some leads or sources, lemme know. I am not buying one from Japan for $450.00! This IS the BFLG, after all. |
|
|
|
Joined: November 2002 Posts: 3647
Location: Pacific Northwest Inland Empire | A little off-topic, or maybe not. We just had a Guitar Center open up here (Yakima, WA). It's a full-size, well-stocked store, with teaching facilities. I hope they do well, as we had limited retailing & music services over the past 20 years. Didn't ask about luthiery services. They might have a large case I could use for this project. Figure there is about a 250K population in a 50-mile radius to support their venture. Well, that's capitalism, I guess.
And, not a single Ovation, Celebrity, or Applause in the whole joint. Merde!
Edited by seesquare 2022-01-28 5:54 PM
|
|
|
|
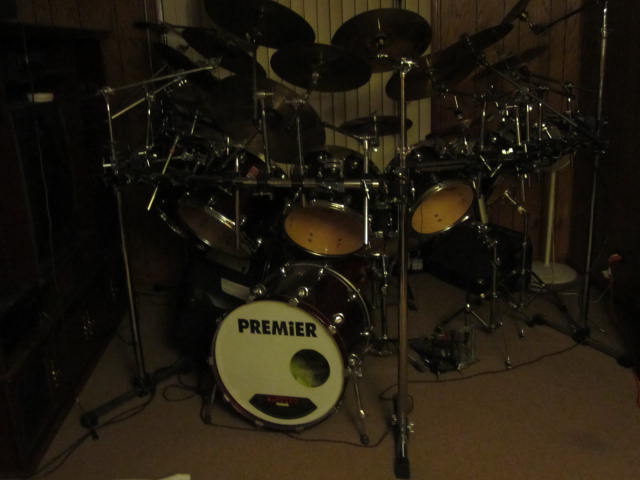 Joined: February 2014 Posts: 714
Location: moline,illinois | Al Pepiak at lost art vintage has used ovation cases,the brown one should be a good fit
http://www.lostartvintage.com/Categorys.aspx?categoryid=11&category...
|
|
|
|
Joined: November 2002 Posts: 3647
Location: Pacific Northwest Inland Empire | Geez, thanks 2WD! I was not sure Al had any more cases. I will give him a call! |
|
|
|
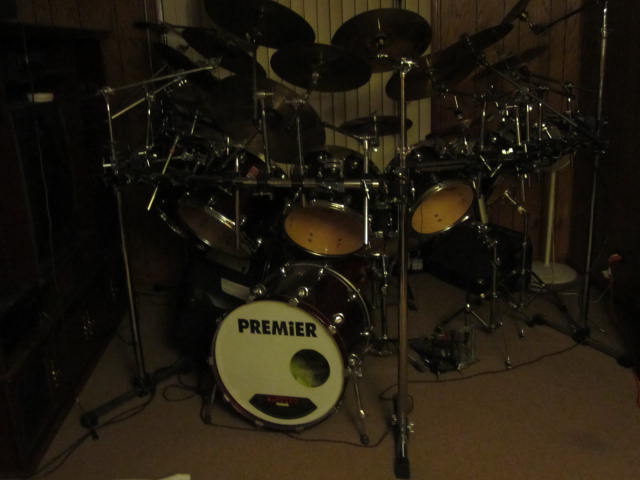 Joined: February 2014 Posts: 714
Location: moline,illinois | seesquare - 2022-01-29 5:58 AM
Geez, thanks 2WD! I was not sure Al had any more cases. I will give him a call!
Your Welcome,Al's probably your best shot for a period correct case,
I saw one on feebay the other day but it looked like as much of a project as the guitar LOL
Love your work just been watching the progress from the sidelines
|
|
|
|
Joined: November 2002 Posts: 3647
Location: Pacific Northwest Inland Empire | "Those who stand & wait, also serve". Thanks for the support 2WD! I called & emailed Al about a case. Hopefully, we make connection fairly soon. "Period-correct" may be an illusion of choice here. That may be all that's available for these models, anyway. And, I have put Bondo on old cases, in the past.
And, as evidenced by my prior gizmo fabrications, I could probably make some jigs for straightening & aligning a case, as well.
Edited by seesquare 2022-01-29 2:16 PM
|
|
|
|
Joined: October 2014 Posts: 270
| What's going on? No progress or photos since 1/27? You're slacking off.  |
|
|
|
Joined: November 2002 Posts: 3647
Location: Pacific Northwest Inland Empire | Sorry for the sloth, fellas. The air brush rig is due for arrival on Tuesday. Crossing my fingers, anyway. Worked on leveling some spots on the top this AM.
Should have some new images of paint samples soon.
Had a reply from Al, too. He will get back with some cases info in a couple of weeks.
Edited by seesquare 2022-01-30 4:28 PM
|
|
|
|
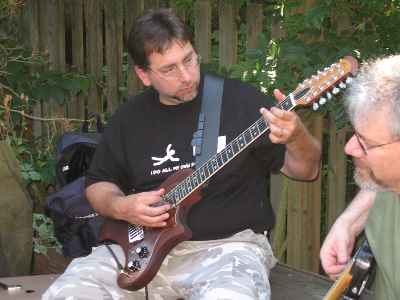 Joined: December 2003 Posts: 13996
Location: Upper Left USA | You can never have too many tools! Looking good! |
|
|
|
Joined: November 2002 Posts: 3647
Location: Pacific Northwest Inland Empire | High praise, indeed! Thanks, Mike. Glad to have you aboard! |
|
|
|
Joined: October 2014 Posts: 270
| MWoody - 2022-01-30 5:52 PM
You can never have too many tools! Looking good!
Especially clamps! |
|
|
|
Joined: November 2002 Posts: 3647
Location: Pacific Northwest Inland Empire | "Especially clamps". I'm hip. Like, ones that have a 12" reach, too! I think my current count is hovering around 400. 'Course, that includes the clothespins. |
|
|
|
Joined: November 2002 Posts: 3647
Location: Pacific Northwest Inland Empire | OK, I'm back in business. Got the new tool & will be practicing awhile. Bought some special additive for the paint which makes it stick to plastic better.
(airbrush- smaller image.jpg)
Attachments ----------------
airbrush- smaller image.jpg (92KB - 0 downloads)
|
|
|
|
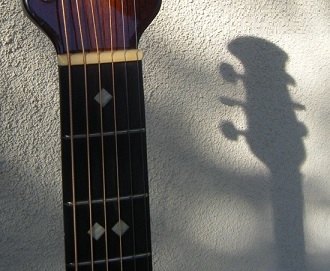 Joined: February 2016 Posts: 1846
Location: When?? | Oh, my. You just used the "p" word. |
|
|
|
Joined: November 2002 Posts: 3647
Location: Pacific Northwest Inland Empire | Okay, “non-wood” surfaces. Is that more palatable? We do have some sensitivity about that issue. My bad. Mea culpa.
The first couple of test pieces look pretty good, anyway. |
|
|
|
 Joined: June 2012 Posts: 2332
Location: Pueblo West, CO | If you want to sound really fancy, call the "non-wood" pieces, "composite."
Ooh... Ahhh... |
|
|
|
Joined: March 2002 Posts: 15674
Location: SoCal | Do what Kaman did and make up a name -- Lyrachord...... |
|
|
|
Joined: November 2002 Posts: 3647
Location: Pacific Northwest Inland Empire | Shot the first couple of black acrylic on the bowl. Got a couple of sags to be sanded out. Generally, going pretty well. Will shoot some clearcoat over the black. Then, cut & buff. Should be almost back to original, pretty soon.
(1st airbrush coat 1- smaller image.jpg)
(1st airbrush coat sags- smaller image.jpg)
(1st airbrush coat top end- smaller image.jpg)
Attachments ----------------
1st airbrush coat 1- smaller image.jpg (61KB - 0 downloads)
1st airbrush coat sags- smaller image.jpg (63KB - 0 downloads)
1st airbrush coat top end- smaller image.jpg (72KB - 0 downloads)
|
|
|
|
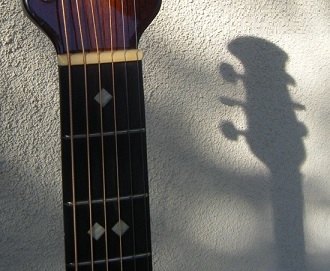 Joined: February 2016 Posts: 1846
Location: When?? | That looks very nice! Definitely a strange shape to work with from every angle. What type of cut & polish pad/wheel will you use.. as in bench-mount vs. hand-held? |
|
|
|
Joined: November 2002 Posts: 3647
Location: Pacific Northwest Inland Empire | Hand-held. I have some mild orange peel in the overall surface, and it will be unacceptable. I will sand it smooth again, and adjust the airbrush setting. I tried some small areas of clear finish, but didn’t remedy the problem. Persevere. |
|
|
|
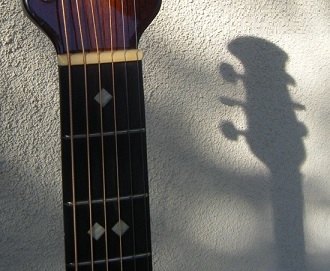 Joined: February 2016 Posts: 1846
Location: When?? | Just a suggestion if you haven't gone there yet with the re-sand.. have you considered using green pad to rescue light orange peel? And I mean the light texture green pad like you find on the back of the little yellow cleaning sponges, NOT the coarse weave type like you get when buying just the green pad alone (you can buy the sponges in the grocery store cleaning aisle). We refinished an antique stove some time back that had light to moderate orange peel using rattle can epoxy appliance paint, and the light weave green pad knocked it down quite well prior to the final coat. It does not remove as much of the paint's base as sanding does if you meter the pressure oh-so lightly in circular motion. It's best if used damp-to-wet, and work the pad a bit first to soften it up.
Edited by Love O Fair 2022-02-03 10:16 PM
|
|
|
|
Joined: November 2002 Posts: 3647
Location: Pacific Northwest Inland Empire | Thanks for the suggestion, Al. I have already sanded off most of the offending surface but will get some of those light texture green pads. I really don't want this to take forever, i.e., "How many times do you have to put your hand on a hot burner?!" |
|
|
|
Joined: November 2002 Posts: 3647
Location: Pacific Northwest Inland Empire | Greetings,
I may need some advice here from experienced airbrush artists. The paint I airbrushed had some orange peel surface, likely my fault- either paint too thick/thin or not correct air pressure. As I was sanding it off with 1200-grit, the paint came off mighty fast & easily. My question being, is this paint too soft, and should I be using another paint type, like a solvent-based enamel, or even lacquer? I have had fairly good results with rattle-can enamels in the past, which were solvent-based aerosols, and set up fairly hard in about 3 days. Did I sand off the acrylic too quickly?
As I noted previously, I really don't want to repeat this fiasco. Einstein was probably right.
And, another issue. This acrylic didn't have a very glossy finish. Is that what I can expect with this type of paint product? I used the proper thinner, too.
Edited by seesquare 2022-02-04 1:24 PM
(airbrush paint front label- smaller image.jpg)
(airbrush paint rear label- smaller image.jpg)
Attachments ----------------
airbrush paint front label- smaller image.jpg (92KB - 0 downloads)
airbrush paint rear label- smaller image.jpg (87KB - 0 downloads)
|
|
|
|
 Joined: June 2012 Posts: 2332
Location: Pueblo West, CO | Acrylic paint, like all water-based paint is pretty soft. There's not too much you're going to be able to do that will 'harden' it.
Even solvent-based one-part paint (enamel) can be pretty soft. Generally speaking solvent-based paint will 'harden' up as the solvent out-gasses. Like lacquer, you need to let it rest for at least a month.
Orange peeling can be caused by several factors. It could be the area was too cold, the paint was too thick, (excessive viscosity) too thin of a coat that prevented the paint from self-leveling or was sprayed from too far away from the surface.
I would suggest trying again, but on a practice surface.
Knowing that you'll have to level and polish the surface requires quite a build-up of paint to prevent burning through the finish.
I apply paint to guitars slightly different than what the instructions say. The instructions call for a light dusting coat, let the solvent flash off for 5-10 minutes. Apply another dusting coat, let it flash. Then, spray on a final wet coat. This method can lead to orange peel.
I spray on a wet coat and let it flash. This usually comes out pretty level. Then I spray another wet coat, which orange peels. Finally I spray on a heavy wet coat to level the surface again. The final coat fills most of the orange peel from the second coat. Even though I sprayed three actual coats of paint, I consider this to be a 'coat.'
When I was spraying with Minwax Polyurethane, I would spray on a 'coat' in the morning, let it dry until the afternoon, then sand it level to prep for another 'coat' the next morning. I would usually lay on 7-8 'coats' of paint, which would be the equivalent of 21 coats done the conventional way.
As I say, it takes about a month for the solvents to out-gas and the paint to harden.
I like using Eastwood 2K paints because they get really hard, really quickly. Since it's 2-part finish, there are no solvents to out-gas, so the finish doesn't really shrink like 1-part paint.
Lacquer is a good, hard finish, but the coats go on really thin. You'll need to put on about 15-20 coats, then let it rest for a month. One of the nice thing about lacquer is there's no need to sand between coats because the new coats melt into the previous coats. The problem with lacquer is that it's chemically delicate. Lots of modern plastics and rubbers will out-gas solvents that 'melt' the finish.
Edited by DanSavage 2022-02-04 5:28 PM
|
|
|
|
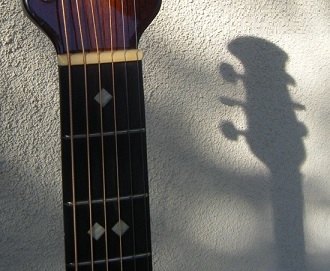 Joined: February 2016 Posts: 1846
Location: When?? | @Dan - >>>I like using Eastwood 2K paints <<<
Since the first time I saw you use an Eastwood 2K finish I have researched it and seen photos that others have posted of Eastwood product results. The stuff seems to be the Cadillac of spray cans (oxymoron, I know) and I have seen and read nothing but good about it. I had intended to use it on a 5' table top, but it is a bit pricey and tongue-in-cheek for such a large surface spray application, and opted instead for brush-on.. so my post here may be a lot to say for someone who has yet to actually use it on anything, but I tend to trust the reviews and photos when they are all so positive. |
|
|
|
Joined: November 2002 Posts: 3647
Location: Pacific Northwest Inland Empire | Hmmmmm.........the Eastwood 2K looks like a good product. What I'm curious about is whether the can is a one-time use, after you release the activator agent in the can. It covers 10-to-16 sq. ft, which will be plenty. Pot life is 48 hours, per product description. So, do you shoot a couple of coats within that 48 hours?
I have used the Minwax Poly in the past, for a clear coat on guitar tops. My protocol has been similar to yours. A couple of coats, let it set up a couple of days, sand it level, shoot a couple more coats, sand, and then (usually) a finish coat.
I think I may be barking up the wrong tree with the acrylic. It is easy to use & clean up, but it really isn't going to get me the finish I desire. |
|
|
|
Joined: November 2002 Posts: 3647
Location: Pacific Northwest Inland Empire | Yeah, the bowl surface was probably too cold, also. I probably am not willing to wait until April for warmer weather, either. |
|
|
|
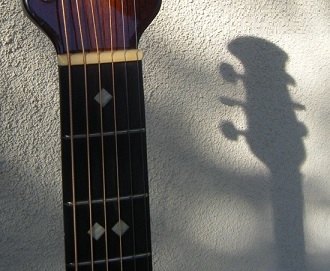 Joined: February 2016 Posts: 1846
Location: When?? | @seesquare - >>>I probably am not willing to wait until April for warmer weather, either.<<<
Uh-oh. Now you're sounding like I do when it comes to hurry-up anxiety on projects like this.. which, realizing my own history, is definitely not a good thing. You know.. haste and waste and stuff. And certainly not intending to wag an amateur finger at a seasoned crafter.. but.. I know someone with a career in human behavioral matters, so let me know if you want their number and maybe they can talk you into waiting. Either that or fire up your nifty heater bender gizmo and warm the shop for a day or two. Another option is to wait for wife to go out, then quickly mask off the kitchen and take chances with lingering odor and brow beatings by said wife (been there, too). |
|
|
|
Joined: November 2002 Posts: 3647
Location: Pacific Northwest Inland Empire | Thanks for the reality check. Actually, SWMBO asked if there was somewhere inside the house I could paint. As I will probably switch to another type of paint, which will probably stink up the joint, probably not an option. And, I have been guilty of rushing projects, with less than ideal outcomes.
I suppose waiting a few weeks for better weather might be the best option. I know, my viewers will be disappointed with a delay. But, it may be the right choice for now. Actually, it will afford an opportunity to get the instrument set up and find out what it’s playability issues are. |
|
|
|
 Joined: June 2012 Posts: 2332
Location: Pueblo West, CO | seesquare - 2022-02-04 6:34 PM
Hmmmmm.........the Eastwood 2K looks like a good product. What I'm curious about is whether the can is a one-time use, after you release the activator agent in the can. It covers 10-to-16 sq. ft, which will be plenty. Pot life is 48 hours, per product description. So, do you shoot a couple of coats within that 48 hours?
Yes, it's a one-time use. But there are caveats.
You can extend the pot-life of the activated urethane by putting it into your refrigerator between uses. The low temps will retard the catalyzing process.
What I do is to get the guitar ready to spray -- sanded, de-greased & tack-ragged. Activate the finish and spray my three-coat regimen in the morning. Then, put the can into a zip-lock baggie and into the fridge. That afternoon, level the finish and clean with naptha.
Next morning, pull the paint can out of the fridge and into a small container of hot water to heat the finish in the can to room temperature. Once it's warm, give the guitar a quick swipe with a tack rag, then repeat the three-coat regimen and stash the paint can back into the fridge when I'm done spraying.
I'll repeat this process until I'm happy with the thickness and look of the finish.
I've had a can of finish last for a couple of weeks this way. Even in the fridge it will eventually catalyze, but you will have had plenty of time to finish a guitar. |
|
|
|
 Joined: June 2012 Posts: 2332
Location: Pueblo West, CO | seesquare - 2022-02-05 6:06 PM
Actually, SWMBO asked if there was somewhere inside the house I could paint. As I will probably switch to another type of paint, which will probably stink up the joint, probably not an option.
Yeah, if you're going to spray with Eastwood 2K, you're definitely not going to want to spray inside.
Even outside is tricky because you don't want to be breathing in the paint fumes from this finishing system.
There are no solvents. Only catalyzed paint. (Imagine breathing aerosol 2-part epoxy) |
|
|
|
Joined: November 2002 Posts: 3647
Location: Pacific Northwest Inland Empire | Thanks for the info, Dan. I will consider the options while the weather warms up a bit around here. I will be setting up the guitar in the meantime. |
|
|
|
Joined: November 2002 Posts: 3647
Location: Pacific Northwest Inland Empire | Sounds pretty good. Action is 2.38/32” (0.074) treble side & 1/8” (0.124), bass side. Nut was a royal pain, but the saddle was spot-on. Intonation is a shade off on the G string, I think. String spacing is more narrow at the neck now. Neck relief required about a half-turn tighter. Will check it again tomorrow for additional adjustment. Okay, praying for warmer weather, but reasonably satisfying outcomes, thus far! |
|
|
|
Joined: October 2014 Posts: 270
| Now we know why Ovation went from a shiny bowl to a textured bowl. |
|
|
|
Joined: October 2014 Posts: 270
| Now we know why Ovation went from a shiny bowl to a textured bowl. |
|
|
|
Joined: November 2002 Posts: 3647
Location: Pacific Northwest Inland Empire | I would speculate the SMC bowls were cheaper, in the long run. Hand-laid fiberglass would run up the labor & production costs, and probably slowed down the production rate. No matter the aesthetics, you just can't avoid the beancounters. At the end of the day, it's still capitalism. |
|
|
|
Joined: March 2002 Posts: 15674
Location: SoCal | It was easier to finish the bowls, but they also needed the molded area at the neck so that they could attach the Kaman Bar neck. The earlier bowls were thinner but the molded bowls more practical for their needs....... |
|
|
|
Joined: November 2002 Posts: 3647
Location: Pacific Northwest Inland Empire | I have put several coats of Truoil on the top & believe this is about as good as I am able, right now, in regard to the top finish. I have trimmed the rosette and finagled it into the original routed area where it's predecessor had lied. Has an interesting contour, as the fretboard extension area is flat, but the rear section is raised, somewhat. I don't think it makes a lick-of-difference to the structural integrity or resonance; it's in keeping with the restoration of functionality. Certainly more than lipstick on a pig, also!
(rosette 2- smaller image.jpg)
(rosette closeup treble view- smaller image.jpg)
(rosette closeup end view- smaller image.jpg)
Attachments ----------------
rosette 2- smaller image.jpg (94KB - 0 downloads)
rosette closeup treble view- smaller image.jpg (48KB - 0 downloads)
rosette closeup end view- smaller image.jpg (56KB - 0 downloads)
|
|
|
|
 Joined: June 2012 Posts: 2332
Location: Pueblo West, CO | Was the rosette shaped like that before it was attached to the top? |
|
|
|
Joined: November 2002 Posts: 3647
Location: Pacific Northwest Inland Empire | Nope, it was pretty flat. It took on that contour after it was fitted to the depressed area where the original was. So, the replacement rosette is a shade larger in O.D. than the original. |
|
|
|
Joined: March 2002 Posts: 15674
Location: SoCal | So the replacement was an overlaid, not inlaid, rosette?
|
|
|
|
Joined: October 2014 Posts: 270
| Looks great and I like that it proudly bears its scars. It makes it much more interesting.
Edited by BCam 2022-02-11 6:52 PM
|
|
|
|
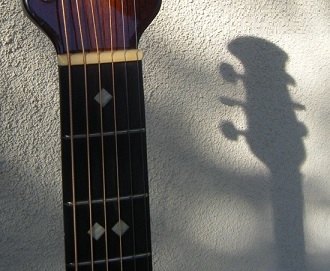 Joined: February 2016 Posts: 1846
Location: When?? | I shuttered when I first saw that rosette. It was flat as a dime when it left here. But now I understand what you mean about the fit, and I hope it seats and seals as-is and doesn't further tweak. But hey, now you can say that you have a round-front round-back guitar! The top on my '68 DB has substantial top sinking around the sound hole span that may have otherwise turned out the same as yours IF it had an overlaid rosette; HOWEVER, some owner along the line tried to make an overlay settle in like an original inlaid one, which turned out half-assed okay, but could also be a factor to what caused the sinkage in the first place upon that brace pattern since there is very little belly bulge-- meaning-- you are probably better off like you are with yours, though just the opposite of the installation result on mine (if all that makes any sense).
PS-- The guitar still sounds absolutely fantastic!
::knock on 'sunken' wood::
Edited by Love O Fair 2022-02-11 8:56 PM
|
|
|
|
Joined: November 2002 Posts: 3647
Location: Pacific Northwest Inland Empire | Thanks again, guys!! Since the installation of an overlay into an inlaid resulted in a bit of a gap between the old channel and the new rosette, I decided to epoxy and clamp the rosette as flat as possible. I will see the results tomorrow, after the adhesive cures sufficiently. So, it won’t probably have much of a hump. |
|
|
|
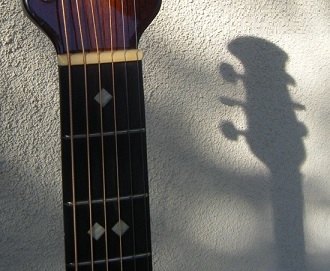 Joined: February 2016 Posts: 1846
Location: When?? | Are you going to use Truoil to finish the bridge, too? I was reading a piece about someone who uses Truoil on porous walnut and other instrument woods and preps the wood with CA glue first-- which is probably too late to do with your top if you didn't use it already-- but may work nice on sealing the bridge. Anyway, here is the URL for the article and photos--
https://drive.google.com/file/d/1t49gfO_pioRARQ8CmikgOHBydBVUs6gh/vi...
|
|
|
|
Joined: November 2002 Posts: 3647
Location: Pacific Northwest Inland Empire | Thanks for the Truoil protocol, Al. I guess the issue will be whether a shiny bridge is what I desire. Are there any advantages for an oiled bridge, like with lemon oil, over the more sealed, harder CA/Truoil treatment? The oiled option probably matches the fretboard better. It is nice to have choices, though. |
|
|
|
Joined: November 2002 Posts: 3647
Location: Pacific Northwest Inland Empire | I see this as an improvement. Hope to start on the bowl painting soon. It's warmin' up!
Edited by seesquare 2022-02-12 10:18 AM
(rosette reglue treble- smaller image.jpg)
(rosette reglue- bottom- smaller image.jpg)
(rosette reglue- bass- smaller image.jpg)
Attachments ----------------
rosette reglue treble- smaller image.jpg (48KB - 0 downloads)
rosette reglue- bottom- smaller image.jpg (61KB - 0 downloads)
rosette reglue- bass- smaller image.jpg (48KB - 0 downloads)
|
|
|
|
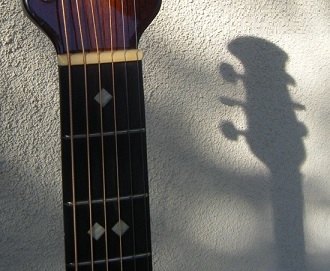 Joined: February 2016 Posts: 1846
Location: When?? | @seesquare - >>>I see this as an improvement.<<<
+1. Nice!!
>>>The oiled option probably matches the fretboard better.<<<
+1 again. |
|
|
|
 Joined: June 2012 Posts: 2332
Location: Pueblo West, CO | I agree that the rosette looks much better after fixing. |
|
|
|
Joined: November 2002 Posts: 3647
Location: Pacific Northwest Inland Empire | I am preparing to shoot the bowl. I am going to use some rattle-can lacquer, warm up the spray area to about 65 degrees, put the cans in hot water, and hope for the best. Since the paint dries quickly, I may be able to level the finish somewhat between coats, if necessary.
(masked 1- smaller image.jpg)
(masked 2- smaller image.jpg)
(masked 3- smaller image.jpg)
(masked 5- smaller image.jpg)
(masked 6- smaller image.jpg)
Attachments ----------------
masked 1- smaller image.jpg (94KB - 0 downloads)
masked 2- smaller image.jpg (76KB - 0 downloads)
masked 3- smaller image.jpg (59KB - 0 downloads)
masked 5- smaller image.jpg (64KB - 1 downloads)
masked 6- smaller image.jpg (76KB - 0 downloads)
|
|
|
|
Joined: November 2002 Posts: 3647
Location: Pacific Northwest Inland Empire | Just in case you are curious, the bowl has been wet-sanded to 2000-grit. |
|
|
|
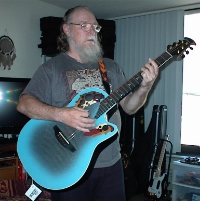 Joined: September 2006 Posts: 10777
Location: Keepin' It Weird in Portland, OR |
|
|
|
|
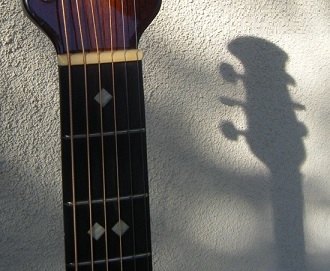 Joined: February 2016 Posts: 1846
Location: When?? | Say now... that's as pretty of a little lap slipper as I ever saw!
(except for a blonde I once knew in St. Louis) |
|
|
|
Joined: November 2002 Posts: 3647
Location: Pacific Northwest Inland Empire | Thanks Guys! Just shot the 1st coat. Will wait a few hours for the next one. Want to build it up kinda slow, but get it to flow correctly. Keeping my fingers crossed & eyes skyward. |
|
|
|
 Joined: June 2012 Posts: 2332
Location: Pueblo West, CO | If you're shooting with lacquer, you only need to wait until the previous coat is dry to the touch.
No matter how long you wait, subsequent coats of lacquer will melt into the previous coats. No need to sand between coats, either, for the very same reason.
The idea is to build up a coating of about 4-6 mils (3-4 sheets of printer paper) so that you have enough finish on there so that when you do start cutting and polishing that you don't burn through it.
With lacquer, you'll need to let it sit for a few weeks while it hardens before cutting and polishing.
Edited by DanSavage 2022-02-16 6:57 PM
|
|
|
|
Joined: November 2002 Posts: 3647
Location: Pacific Northwest Inland Empire | Thanks for the guidance & protocol, Dan. The paint is going down pretty smoothly. I have emptied the can of black lacquer, so far. RE: 4-6 mil finish- how can you determine how thick the finish may be? The rattle can says it covers about 7 sq. ft. Estimating the bowl at about 1/2 of that, so that's arithmetically 2 full coats? I hadn't thought that much about how much paint I needed; I just wanted it to go down smooth & even. I am going to shoot clear lacquer over the color coat, but I suppose I need to have enough black lacquer applied, first. What's your advice, maestro? |
|
|
|
 Joined: June 2012 Posts: 2332
Location: Pueblo West, CO | Oops. I'd thought I had already responded.
I usually just keep applying coats until the finish looks thick enough.
The pros use something called a wet-film gauge, or comb.
Here's what it looks like. 
Here's how you use it. 
|
|
|
|
Joined: November 2002 Posts: 3647
Location: Pacific Northwest Inland Empire | Well, I should have known there was a tool for this issue. How do you use this gizmo without messing up the paint surface? I understand that the reading is taken in the wet film, but I don’t see how it won’t leave a mark, as the paint sets pretty fast. So, take the reading, then shoot more paint over that area?
BTW, thanks for the support! |
|
|
|
Joined: November 2002 Posts: 3647
Location: Pacific Northwest Inland Empire | Product report & review on Amazon- guy states the reading is done right after laying down the paint & doesn't leave a mark. I wonder if the type of paint makes a difference. That lacquer dries awfully fast. |
|
|
|
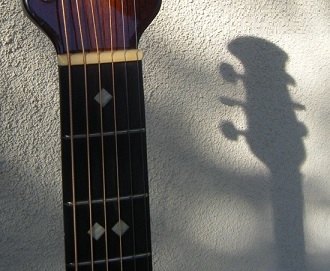 Joined: February 2016 Posts: 1846
Location: When?? | Doesn't leave a mark. That is an interesting learn-about, especially considering usage on a quick drying or thick viscus paint surface. If you are concerned with numerical precision then this tool is definitely the one to have.. but otherwise the end of a toothpick would seem to suffice at least the eyeball aspect of such a measurement if the painter is satisfied with that; or to then measure the mark on the toothpick with the gauge. Just seems less intrusive on the fresh surface. But if the pros say it doesn't leave a mark, then someone with a box of toothpicks is missing out on a cool tool. |
|
|
|
Joined: November 2002 Posts: 3647
Location: Pacific Northwest Inland Empire | I agree with you, Al. I could use a toothpick & probably get an adequate reading of paint depth, and it only leaves one small indentation to flow out, in a relatively unobtrusive location. I think I will just proceed with the clear lacquer & let it set up for a few weeks. I managed to get all the black lacquer down in one day, so this is definitely doable. More progress & I perceive there is light at the end of the tunnel, & it isn't an oncoming train.
(black lacquer 2- smaller image.jpg)
Attachments ----------------
black lacquer 2- smaller image.jpg (62KB - 0 downloads)
|
|
|
|
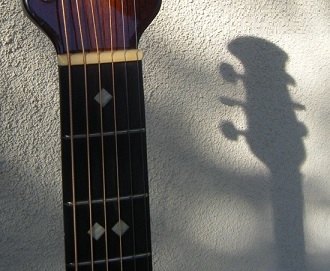 Joined: February 2016 Posts: 1846
Location: When?? | It looks like you are well, well on your way to perfection. Nice job!! It's difficult to tell if the guy in the refection is holding a camera extension handle or possibly blowing a horn in proud jubilation.. but just for fun I will go with the latter, and further imagine abundant echo in said tunnel. Glad it's not a train! |
|
|
|
Joined: November 2002 Posts: 3647
Location: Pacific Northwest Inland Empire | The reflection is comprised of me holding my cellphone over the bowl and the garage door opener track above me. Not terribly impressive, and I continue to hold my breath with this project, with intermittent spells of hyperventilation & panic.
Edited by seesquare 2022-02-20 7:07 AM
|
|
|
|
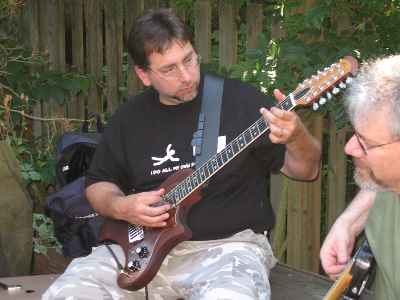 Joined: December 2003 Posts: 13996
Location: Upper Left USA | Yous people continue to be not only a great reference source but an incredible source of enthusiasm! |
|
|
|
Joined: November 2002 Posts: 3647
Location: Pacific Northwest Inland Empire | Thanks for the support, Michael! It appears all my projects boil down to either I manage them, or they manage me. No complaints, really. |
|
|
|
 Joined: June 2012 Posts: 2332
Location: Pueblo West, CO | seesquare - 2022-02-20 5:05 AM
The reflection is comprised of me holding my cellphone over the bowl and the garage door opener track above me. Not terribly impressive, and I continue to hold my breath with this project, with intermittent spells of hyperventilation & panic.
I know how it feels.
I went through the same spells of consternation/panic when I was restoring Jay Kantor's 1967 Balladeer, including refinishing the bowl.
Are you planning to shoot clear over the black?
|
|
|
|
Joined: November 2002 Posts: 3647
Location: Pacific Northwest Inland Empire | Thanks for the empathy, Dan. Not so much the financial risk, but the amount of sweat and time, to avoid having to rework some aspect extensively.
Just emptied the can of clear lacquer on the bowl. Looks good and the reflection is pretty deep. Guess I will let the critter rest awhile and get the finish nice and hard. So, best protocol of cutting & polishing? |
|
|
|
Joined: November 2002 Posts: 3647
Location: Pacific Northwest Inland Empire | I have invested in a set of 2x2 Micro Mesh papers (3000-to-12000-grit) to do the final level & polishing phase. A good deal of elbow grease, I'm sure, but less chance of burning through the finish. And, the shipping will take about a week, so that should stifle my impatient & impetuous impulses!
(Micro Mesh sanding pads- smaller image.png)
Attachments ----------------
Micro Mesh sanding pads- smaller image.png (85KB - 0 downloads)
|
|
|
|
 Joined: June 2012 Posts: 2332
Location: Pueblo West, CO | Yes, if you're done spraying you'll want to let it rest for a month or so.
The 'cutting' portion is meant to level the surface by taking the high spots down to the level of the low spots. (obviously)
If orange peeling is present, you'll need to remove more material than you would if there were no orange peeling. (obviously)
If the orange peeling is extreme, I would start with 600-grit to remove most of it, then switch to 800-grit to fully level the surface.
If the orange peeling is minor, I would start with 800-grit.
At that point, you just work your way through progressively-finer grits until you get to at least 1500-grit.
I wrap the sand paper around a small styrofoam block and always use water to prevent the sand paper from clogging.
Every time you change grits, alter your sanding pattern from vertical to horizontal and vice-versa. This will allow you to more easily see whether you've removed the previous sanding marks.
After that, it's time to start polishing. I've always had good luck with Meguiar's #9 swirl remover with a soft cotton polishing wheel chucked into an electric drill.
I tried #7 a couple of times, but the #9 seemed to work better.
You'll want to alternate between vertical and horizontal between each pass.
I also look at the surface underneath florescent lights as these will show imperfections/scratches really well. Again, alternate views between horizontal and vertical.
Under the lights, any areas that still need polishing will have a cloudy/foggy appearance. |
|
|
|
Joined: November 2002 Posts: 3647
Location: Pacific Northwest Inland Empire | Thanks Dan. The challenge will be waiting a month before I embark on this phase. I will look for the Meguiar's #9 (as in Love Potion?). I understand about alternating the sanding patterns. I have a 2-foot fluorescent fixture over the main bench, so that should suffice for the close inspection for scratches & flaws. There are also two, twin-bulb, 4-foot fixtures on the ceiling, too. As the years commence, I notice needing more illumination for my work projects. Age & Gravity is a bit of a nuisance, at times. This may sound a trifle nit-picky, but what's the best color or wavelength for the light tubes? I know the more-blue ones seem a bit harder on the eyes than the more-yellow ones, but they may show the flaws better.
The orange peel doesn't look too bad. Hopefully, I can start at 800-grit, & proceed from there.
Edited by seesquare 2022-02-21 5:22 PM
(bowl reflection 022122 one- smaller image.jpg)
(bowl reflection 022122 two- smaller image.jpg)
Attachments ----------------
bowl reflection 022122 one- smaller image.jpg (74KB - 0 downloads)
bowl reflection 022122 two- smaller image.jpg (75KB - 0 downloads)
|
|
|
|
 Joined: June 2012 Posts: 2332
Location: Pueblo West, CO | The final surface looks pretty good. Let `er shrink, then start with 800-grit...
Personally, I like the daylight temperature range. (5000K - 6500K)
WRT to tired eyes, I replaced my old florescent tubes with LED and found they put out more light.
Edited by DanSavage 2022-02-22 12:05 AM
|
|
|
|
Joined: November 2002 Posts: 3647
Location: Pacific Northwest Inland Empire | Thanks for the feedback, Dan. I know what you are referring to with the LED lights. I replaced our florescent fixture in the kitchen with an LED fixture, switched it on, and immediately remarked, "Geez, this light must be for old folks!" Yeah, well, get used to it, Bonzo.
So, I will let the finish cure for the next month. Got other things to occupy my time, like fabricating fenders for my recumbent trike. Probably ought to just buy them from the factory, but where's the fun in that?! |
|
|
|
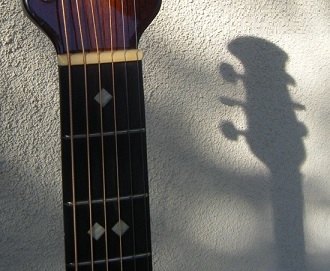 Joined: February 2016 Posts: 1846
Location: When?? | Looking great! That's gonna cut and polish real nice with the 800 followed by your new pads.
A tip on the Meguiar's.. always put it on the applicator cloth or wheel and smooth it out on there first. Never put it directly on the surface first. Great stuff. Long ago (70s-80s) Maguire's marketed a two-step version that was popular on the show car scene. The first step filled, and the second step leveled and cured to "wet look" that lasted for a few days. Perhaps those were the same or similar formulas as 7 & 9 are today. You can also hand-apply either to new car headlights to protect them from going cloudy, or drill-rotary it onto older ones and it will perk them back up.
Have fun with the trike. Maybe go full fairing! My pa-in-law and I once built a recumbrent peddle configuration for a canoe. 10-speed chain in a standard Coleman with 28" diameter paddles on both sides aft and a steering wheel rudder. It required a foot of draw below, but it hauled right along.
Edited by Love O Fair 2022-02-23 12:02 PM
|
|
|
|
Joined: November 2002 Posts: 3647
Location: Pacific Northwest Inland Empire | Some impressive engineering there, Al. So, was it christened, "The Sequoia Sidewheeler"?!
Thanks for the advice on the Meguiar's procedure. I have about a month to study up on polishing, and practice on some stuff, like maybe going after the 1111-6 Balladeer I got from Dave, several months ago. Yes, the one that took the dive & got repaired, a second time. The yellow enamel paint has been curing over a couple of months, so should be hard enough to test out the Micro Mesh pads on. |
|
|
|
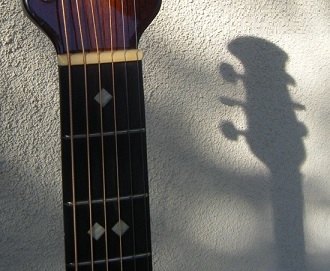 Joined: February 2016 Posts: 1846
Location: When?? | @seesquare - >>>"The Sequoia Sidewheeler"?<<<
Close.. since it did in fact spend most of its life on the slow and easy wides of the San Joaquin River casting toward shore for bass. But no, we named it "Peep".. short for PP.. which stood for "pedal powered".. since who really wants a boat named Pee Pee?
How's it going with the polish on the 1111-6? Curious to know how that enamel reacts to your pads and the Meguire's. I'm agreeing that it should have cured hard by now to make a very ice polished gloss.
Edited by Love O Fair 2022-03-02 1:34 PM
|
|
|
|
Joined: November 2002 Posts: 3647
Location: Pacific Northwest Inland Empire | Haven't started yet. Got sidetracked with the trike fender project. I will report some results, pretty soon. A canoe named Pee Pee- now, that's funny. "Peesquare" would probably not be an improvement, either. |
|
|
|
Joined: November 2002 Posts: 3647
Location: Pacific Northwest Inland Empire | Went after the 1111-6 with the micro mesh pads, up to 12000-grit. Have before & after pictures, though hard to photogrash the change. It is significantly smoother, and I did burn through some of the clearcoat in places. There is still fine scratches, and I will polish them out with some rubbing compound and plexiglass cleaner. Need to make a trip to Ace Hardware, later today. I think I will post the images at the 1111-6 thread, also, to continue that documented process.
(micromesh- after treatment 1st image- smaller image.jpg)
(micromesh- before treatment 3rd image- smaller image.jpg)
Attachments ----------------
micromesh- after treatment 1st image- smaller image.jpg (66KB - 0 downloads)
micromesh- before treatment 3rd image- smaller image.jpg (67KB - 0 downloads)
|
|
|
|
Joined: November 2002 Posts: 3647
Location: Pacific Northwest Inland Empire | Yeah, I know, it's been a while. I wanted the lacquer to set up really well before I went after it with the micromesh pads. I started with 4000-grit to level the orange peel, didn't find it was cutting sufficiently, so dropped to 3600-grit & made adequate progress. Switched to 6000, then finished with 12000. Used some medium rubbing compound to get out the swirls, then put on a coat of paste wax. This is as good as it is going to get. Not perfect, but it is done. I will get it strung up and tweak the action, as necessary.
(new color label- smaller image.jpg)
(Pandora II face- smaller image.jpg)
(Shiny bowl finish 1- smaller image.jpg)
(Shiny bowl finish 2- smaller image.jpg)
Attachments ----------------
new color label- smaller image.jpg (50KB - 0 downloads)
Pandora II face- smaller image.jpg (79KB - 1 downloads)
Shiny bowl finish 1- smaller image.jpg (97KB - 0 downloads)
Shiny bowl finish 2- smaller image.jpg (92KB - 0 downloads)
|
|
|
|
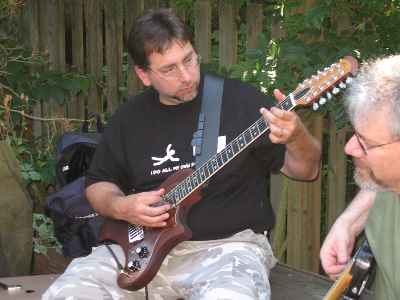 Joined: December 2003 Posts: 13996
Location: Upper Left USA | Yes!
And you were dressed when you took photos of reflective surfaces! |
|
|
|
Joined: November 2002 Posts: 3647
Location: Pacific Northwest Inland Empire | so much for the naked truth, eh? |
|
|
|
Joined: December 2003 Posts: 852
Location: Canada | Oh so shiny! Looking forward to the sound sample m |
|
|
|
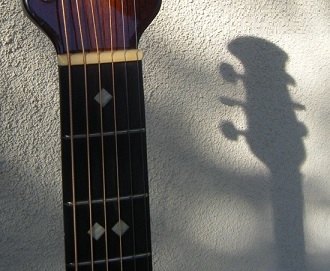 Joined: February 2016 Posts: 1846
Location: When?? | Chris.. what you have there is an over-the-top awesome guitar! Given what you had to start with it is the difference between a Conestoga wagon and a custom Corvette. The bowl finish looks downright fabulous (especially since you had clothes on), and the rustic finish on the top is absolutely perfecto. Great label, too! Can't wait to hear reports on how that old wood sounds when you string it up. I predict it will vibe rich and full. So congratulations on your project!! And finally... wanna sell it? |
|
|
|
Joined: March 2002 Posts: 15674
Location: SoCal | What strings are you gonna put on it?
|
|
|
|
Joined: November 2002 Posts: 3647
Location: Pacific Northwest Inland Empire | RE: strings
Since this has been essentially a community project, I am open to suggestion. I think I should proceed somewhat conservatively with lighter-gauge strings, though I feel confident in my repair work to structural integrity. I have been doing more fingerpicking lately, so that is a consideration. May not need coated strings, as my hands don't sweat much & live in a relatively dry climate.
So, Ladies & Gentlemen, cast a vote. You know the basic age, size, construction & dynamics of this instrument.
Sorry LOF, not (currently) for sale. But thanks for the sterling review of the project! I really need to devote the next year into determining how I bond to this critter. I do the same thing with my tennis racquets. It's the vessel that carries the magic, but you still need to learn the ingredients & incantations. |
|
|
|
Joined: March 2002 Posts: 15674
Location: SoCal | Everybody has their own opinion on this. Just get a set of your favorite strings and see how they sound..... |
|
|
|
Joined: November 2002 Posts: 3647
Location: Pacific Northwest Inland Empire | Ray Davies, from "A Well-Respected Man": "His own sweat smells the best."
Thanks, Paul. That is the way I shall proceed. |
|
|
|
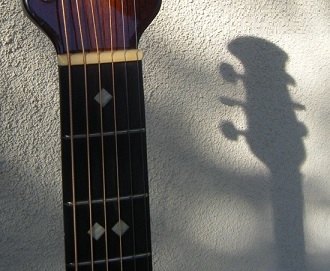 Joined: February 2016 Posts: 1846
Location: When?? | I got all hung up on D'Addario EXP-16s for a while. Extended play coated. Worked as advertised and kept accurate tone for substantially longer than the standard EJ-16s which are of the same stock, just not coated. I think they stopped making them since the only ones I can find anymore are on Ebay and other obscure places, and those are typically the older issue packaging. Anyway, I still have one pack left. If you'd like to try them on Pandora II let me know and I will shoot them up your way.
Edited by Love O Fair 2022-04-10 6:38 PM
|
|
|
|
Joined: November 2002 Posts: 3647
Location: Pacific Northwest Inland Empire | Gee, thanks for the offer! I appreciate the generosity. I think I will just dash down to The Olde Minstrel Shoppe and secure a set of Silk & Steel. They are the most familiar, and will provide a reference for this initial trial. |
|
|
|
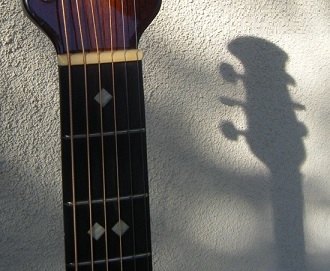 Joined: February 2016 Posts: 1846
Location: When?? | @seesquare - >>>secure a set of Silk & Steel<<<
I have never tried those before, so I went and did some research upon your mention. If I play 1,000 times, I use a pick, maybe, twice-- and even then it is the thinnest pick possible. Always a bare flesh thumb strummer and finger plucker. Rarely using fingernails to pick either, but rather just various callouses that always seem to naturally maintain to my daily playing all on their own (though I sometimes file on them for different touches and tones). So I think I will join you in the Silk & Steel endeavor, and shall experiment upon what may come of it. I see D'Addario EJ40 in the online ads. Are those the ones you use??
Edited by Love O Fair 2022-04-11 7:02 AM
|
|
|
|
Joined: November 2002 Posts: 3647
Location: Pacific Northwest Inland Empire | I kinda like the Ernie Ball version. Yeah, I'm pretty old. They seem to be pretty dependable- "what you hear is what you get". Being functionally tone-deaf, I really can't discriminate real well, anyway. Guitar tuner- never leave home without it. Or, misplace it. |
|
|
|
Joined: November 2002 Posts: 3647
Location: Pacific Northwest Inland Empire | Just a quick update. The refurbished incarnation is sounding magnificent & enjoying it a lot. The 1st hardshell case scenario from Guitar Center was a total flop (they said it would fit- wasn't even close). I have another model on backorder, due to arrive about mid-June. Hopefully will be an improvement & more accommodating. I am currently using an old Worcester T&S chipboard that housed the Academy blue-top. It's flexible enough to allow the latches to work. Looked for another Worcester case from different sources. Geez, those critters are worth some serious bucks! I tried out my other Ovation cases. The 1115 case is too shallow, believe-it-or-not. The C2C4 case is for a classical guitar & not deep-enough, either. The GCDB apparently had a really deep bowl. I measured it at 6-1/2", not including the bridge & saddle. Fat-bottom-girls, eh wot? |
|
|
|
Joined: March 2002 Posts: 15674
Location: SoCal | I did a thread, about 4 years ago on bowl depths. The deep bowls were deeper in the 60's and lost depth over time. I'll try to find the thread.....
|
|
|
|
Joined: March 2002 Posts: 15674
Location: SoCal | Back in Sept 2018, I posted this about deep bowls
"Just as a note, researching old catalogs showed that the artist depth bowl were originally 5 1/8" deep. By 1984, the GC model was 5 1/4" deep, which is what the mid depth bowls became. So the 06 model was based on the mid 80's models, the 2018 model on the 70's models.
1/4 inch difference really made a difference. Deep bowls started out as 5 13/16" depth and evolved to to 5 3/4". 1/16" difference. Maybe one of the reasons why old O's sound a little better?" |
|
|
|
Joined: March 2002 Posts: 15674
Location: SoCal | The complete thread is here....
http://ovationfanclub.com/megabbs/forums/thread-view.asp?tid=48497&...
|
|
|
|
Joined: November 2002 Posts: 3647
Location: Pacific Northwest Inland Empire | Thanks for the posting, Paul.
So, this poses an interesting question for me. When the Mothership was constructing these various iterations of roundback guitars, did they use the same mold for deep bowls, then a different mold for mid-bowls, then another for shallow-bowls (sounds logical), then vary the relative depth within those models. So, the GCDB would have been, essentially, an "untrimmed" deep-bowl, straight from the mold. Given back then, they were handlaid fiberglass, there could have been greater latitude & options for bowl depth?
And, I would guess old O's sound better because they're old- top is aged & "opened up". That's why Dan uses torrefied tops on his creations. And, I will place a bet that all those engineering types at The Mothership were testing out soundboard vibrational dynamics of differing bowl depths pretty extensively. So perhaps, bringing something new to the market was the driving force for choosing the combination of components. So, do you want the '70 Boss 302, or the '69 Mach 1? As they say, YMMV. |
|
|
|
 Joined: June 2012 Posts: 2332
Location: Pueblo West, CO | moody, p.i. - 2022-05-11 7:02 PM
I did a thread, about 4 years ago on bowl depths. The deep bowls were deeper in the 60's and lost depth over time. I'll try to find the thread.....
Also, the older bowls were smaller back then. This is an older bowl inside a newer bowl. The the newer bowl is the one I got from TJR and used it for my Black Pearl.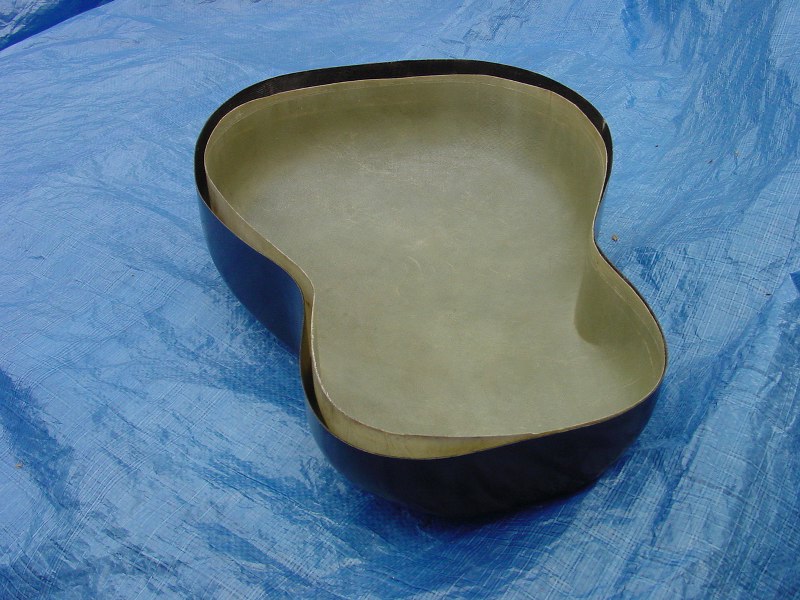
|
|
|
|
Joined: December 2003 Posts: 852
Location: Canada | I was not aware of those subtle bowl changes over time figured that Ovations were very consistent. Did this also include Adamas, i.e. did a 1687 change bowl size in its 20 year production history, and how did the RIs fit in that came almost 10 years after production stopped? |
|
|
|
Joined: March 2002 Posts: 15674
Location: SoCal | I think things changed as they better learned to make the bowls and then in the early 80's when they started using the molded bowls, not the hand laid bowls.
Just a guess...... |
|
|
|
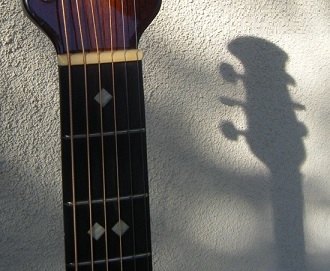 Joined: February 2016 Posts: 1846
Location: When?? | I agree with Paul. The early hand-laid method left a bit of wiggle room per bowl or model, but the latter fixed molds did not wiggle or lie and just kept on coming. |
|
|
|
Joined: November 2002 Posts: 3647
Location: Pacific Northwest Inland Empire | So, in a relative sense, a trifle less "handmade", then. |
|
|
|
 Joined: June 2012 Posts: 2332
Location: Pueblo West, CO | Yeah, nah!
A 'molded' part comes out the exact size of the mold that produced it.
There is no wiggle room unless the molds were changed from one production run to the next. |
|
|
|
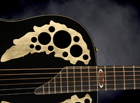 Joined: October 2012 Posts: 1077
Location: Yokohama, Japan | Hey seesquare, been away for nearly an year and re-read through this whole thread. Just great information all around. Thanks again for sharing your journey. I noticed that the airbrush didn't work out for you. Sorry about the bad advice! Hope the investment in the equipment wasn't a total loss... Was surprised to see that you settled on a rattle can lacquer with no clear coat? Just amazed at the level of gloss you achieved with that! Must of spent an enormous amount of time with the cut and polish process - a real labor of love. How does she sound with the Silk & Steel? |
|
|
|
Joined: March 2002 Posts: 15674
Location: SoCal | Chris, still enjoying the GCDB? |
|
|
|
Joined: November 2002 Posts: 3647
Location: Pacific Northwest Inland Empire | You betcha! It's a great instrument. I find myself grabbing the GCDB about as often as the 1111 I got from Dave. They both have some serious mojo for me. I'm blessed with having "normal" humidity in my baliwick, so they just hang on the wall for easy access. Gotta put in a plug for Dennis Anthonis on YouTube. He's older than me, anyway, and keeps on truckin', despite some serious hand issues over the past few years. Very inspiring & reaffirming.
And, Paul, thanks for asking! |
|
|
|
Joined: November 2002 Posts: 3647
Location: Pacific Northwest Inland Empire | Oh, and I still haven't found a case for the GCDB. Just too deep. I will eventually construct one, I guess. |
|
|
|
Joined: March 2002 Posts: 15674
Location: SoCal | Chris, send me an email moody dot pi at gmail . I'd like to know where you live. I've got kids in both Oregon and Washington and would enjoy seeing you on a trip up there..... |
|
|
|
Joined: November 2002 Posts: 3647
Location: Pacific Northwest Inland Empire | You left off the ".com". Picky, picky, picky..........message sent!
Actually, that didn't work. Check your mailbox here.
Edited by seesquare 2023-02-23 2:43 PM
|
|
|