|
|
Joined: May 2011 Posts: 81
Location: Ozark, Arkansa | Dan Savage, I have probably asked before about removing an Ultra glued in neck, but I can't track it down if I did. With the top off, can I use a heat gun to warm up the bowl and epoxy and remove the neck? Or is that too dangerous for the bowl? Do I have to steam it loose instead?
I would like to convert it to a bolt on neck while I am in the process of making this an experimental guitar, and it would be good to practice this process on a low value Ovation. I have probably mentioned the only significant issue was the top, and that is off now.
I am building it with an alternative to conventional kerfing, and making the top so I can remove it and try different bracing patterns and bridge designs. I figure I might as well go whole hog and improve the neck mount at the same time
(IMG_0946.jpg)
Attachments ----------------
IMG_0946.jpg (40KB - 0 downloads)
|
|
|
|
 Joined: June 2012 Posts: 2330
Location: Pueblo West, CO | Since the bowl is SMC that was molded at 350 degrees, you can use a heat gun to soften the epoxy holding the neck in place.
When it gets to about 170 degrees, you can start to wiggle the neck. It is a dovetail neck that's been glued into the socket in the bowl.
If you look at the Patch's Parlor Build... thread you can see what you're dealing with. |
|
|
|
Joined: May 2011 Posts: 81
Location: Ozark, Arkansa | Do or do not, there is no try!
It worked!
Kept my trusty infrared thermometer at the ready and checked it along the way frequently. I was almost ready to give up, when I noticed a separation between the heel and the bowl. It was all downhill from there.
Now, is there a trick to converting it to bolt on, a how-to-convert somewhere?
(Ultra neck removal.jpg)
Attachments ----------------
Ultra neck removal.jpg (55KB - 0 downloads)
|
|
|
|
Joined: May 2011 Posts: 81
Location: Ozark, Arkansa | I have removed the rest of the residual epoxy from the dovetail and pocket, and I have to say I was astonished by something.
For all I have read about MIK assembly, with sloppy loose neck joints and gobs of epoxy to fill them, nothing could be further from the truth on mine.
When I pulled them apart, I was surprised at how little extra epoxy there was. And when I put them back together to check the fit without the epoxy, I was amazed by how solid the joint was. Really, no wiggle room at all. I am impressed by the precision for all the speed of assembly required to mass produce them.
Which leads me to a question, I guess. If they fit this good to start with, why epoxy them? Why not just make them bolt on to start with?
Edited by Oldvation Guy 2020-08-06 9:02 AM
|
|
|
|
 Joined: June 2012 Posts: 2330
Location: Pueblo West, CO | Oldvation Guy - 2020-08-06 5:14 AM
Do or do not, there is no try!
It worked!
Kept my trusty infrared thermometer at the ready and checked it along the way frequently. I was almost ready to give up, when I noticed a separation between the heel and the bowl. It was all downhill from there.
Now, is there a trick to converting it to bolt on, a how-to-convert somewhere?
Good job.
The only trick is that you need to install threaded inserts into the heel and drill matching holes into the neck block area.
Since this heel's dovetail is wider, it will be less prone to splitting when you install the inserts. I didn't convert Patch's Parlor to bolt-on because the dovetail on the neck was to narrow and I didn't want to take a chance.
Edited by DanSavage 2020-08-06 2:40 PM
|
|
|
|
 Joined: June 2012 Posts: 2330
Location: Pueblo West, CO | Oldvation Guy - 2020-08-06 6:55 AM
Which leads me to a question, I guess. If they fit this good to start with, why epoxy them? Why not just make them bolt on to start with?
Cost. Bolt-on requires threaded inserts and bolts and the labor to install them. Epoxy is much cheaper and less labor intensive. |
|
|
|
Joined: May 2011 Posts: 81
Location: Ozark, Arkansa | I picked up two threaded inserts today at the hardware, but it will probably be this weekend before I can install them.
The way I am planning to put them in, I do not expect an issue with splitting the heel. But I will probably make a jig for a clamp to reinforce the heel while I install them to prevent any possibility that insertion pressure will split it.
Edited by Oldvation Guy 2020-08-06 5:43 PM
|
|
|
|
Joined: May 2011 Posts: 81
Location: Ozark, Arkansa | I want to be sure I drill the holes straight, perpendicular, and parallel, so I made this drill guide to help.
I discovered there was a slot in the pocket perfect for this purpose. So I welded two steel 1/4" barrels to a piece of flat stock exactly the same width as the slot in the picture. I will clamp the guide via the top barrel so I can drill the bottom hole in the pocket first. Then I will temporarily bolt the bottom guide in place while I drill the top hole.
Then I will install the neck in the pocket snugly, moving the guide bracket to the inside of the bowl to drill through the guide into the heel.
Edited by Oldvation Guy 2020-08-09 11:44 AM
(IMG_0959.jpg)
(IMG_0960.jpg)
(IMG_0961.jpg)
(IMG_0962.jpg)
Attachments ----------------
IMG_0959.jpg (43KB - 0 downloads)
IMG_0960.jpg (40KB - 0 downloads)
IMG_0961.jpg (38KB - 0 downloads)
IMG_0962.jpg (35KB - 0 downloads)
|
|
|
|
 Joined: June 2012 Posts: 2330
Location: Pueblo West, CO | Nice job. That'll work. |
|
|
|
Joined: May 2011 Posts: 81
Location: Ozark, Arkansa | Thanks, Dan. One last pic.
I said I was going to make a special tool to reinforce the heel when I set the anchors in it. Well, here it is.
The "jaws" are cut out of a piece of yellow pine on a 15 degree angle to fit into the dove tail, not just contact the outer edge. Then a clamp holds the jaws in place with an appropriate amount of pressure to prevent expansion of the heel.
I also glued some maple pieces to the end of the heel for added insurance. I already made sure they fit into the pocket properly. They also give me a bit more depth on the heel for the anchors. Probably overkill, but I would rather be safe than sorry.
What fun!
Edited by Oldvation Guy 2020-08-09 7:29 PM
(IMG_1740_01.jpg)
Attachments ----------------
IMG_1740_01.jpg (83KB - 0 downloads)
|
|
|
|
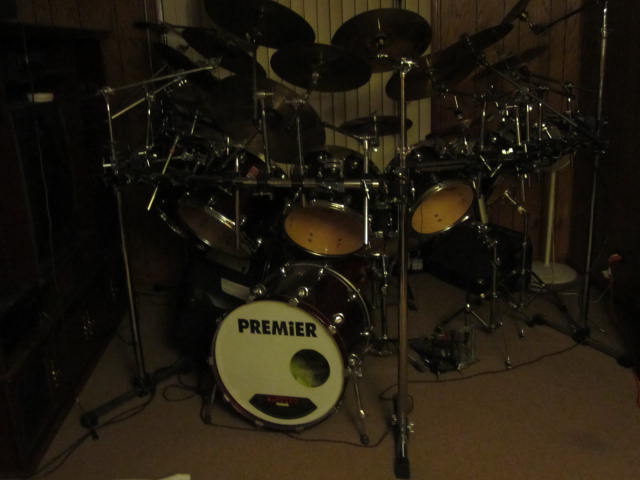 Joined: February 2014 Posts: 714
Location: moline,illinois | Oldvation very cool work I hope Arumako sees this he'd dig it I believe he changed a celebrity from dovetail to bolt-on,what type of heat gun did you use to loosen the neck I have a couple guitars that need work and am debating trying to do the neck re-sets myself.
|
|
|
|
Joined: May 2011 Posts: 81
Location: Ozark, Arkansa | The drill guide and dove tail clamp worked perfectly for drilling the holes in the pocket and heel.
I will let the pics speak for themselves. The neck is bolted on and solid!
(IMG_0962.jpg)
(IMG_0963.jpg)
(IMG_0966.jpg)
(IMG_0969.jpg)
(IMG_0967.jpg)
(IMG_0968.jpg)
(IMG_0971.jpg)
Attachments ----------------
IMG_0962.jpg (35KB - 0 downloads)
IMG_0963.jpg (69KB - 0 downloads)
IMG_0966.jpg (67KB - 0 downloads)
IMG_0969.jpg (59KB - 1 downloads)
IMG_0967.jpg (60KB - 0 downloads)
IMG_0968.jpg (65KB - 0 downloads)
IMG_0971.jpg (56KB - 0 downloads)
|
|
|
|
 Joined: June 2012 Posts: 2330
Location: Pueblo West, CO | Nicely done, Steve.
Yep. It doesn't take much to hold the neck on. |
|
|
|
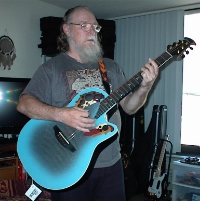 Joined: September 2006 Posts: 10777
Location: Keepin' It Weird in Portland, OR | Impressive.
|
|
|
|
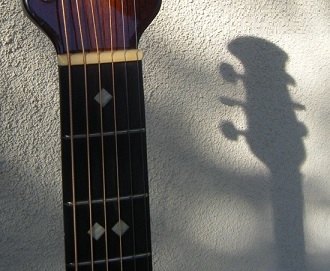 Joined: February 2016 Posts: 1846
Location: When?? | Excellent! Nice practical approach. Looks like to turned out great. Extra points for working barefoot!
Please keep us posted on this one's ongoing progress. |
|
|
|
Joined: May 2011 Posts: 81
Location: Ozark, Arkansa | Thanks! I do my best work barefoot. Lets me feel the earth move under my feet...oh, wait, that is the wrong song... |
|
|
|
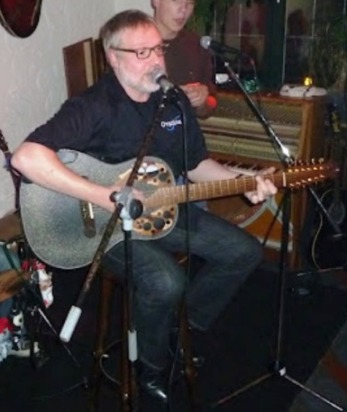 Joined: May 2011 Posts: 758
Location: Muenster/Germany | Great work! And thus you can loose the neck if you may need a better neck angle with the new top. Don“t set the screws too tight. |
|
|
|
Joined: May 2011 Posts: 81
Location: Ozark, Arkansa | Thanks, DetlefMichel. But I am struggling to understand why Ovation used two 1/4 20 bolts to hold the neck on. By your remark, and what Dan Savage said, the two big bolts seem to be overkill.
The next phase will be creating my kerfing. The top will be screwed on, rather than be glued, because the purpose of this guitar is experimentation with tops, bridges, bracing, stringing, etc. The top will be held on by 14 small screws and inserts in blocks around the rim of the bowl.
I have already added electronics and battery box to the bowl, and a sound port.
Even finishing the bowl will be experimentation.
I am pretty pumped about this project! A long time in the planning.
Edited by Oldvation Guy 2020-08-14 8:30 PM
|
|
|
|
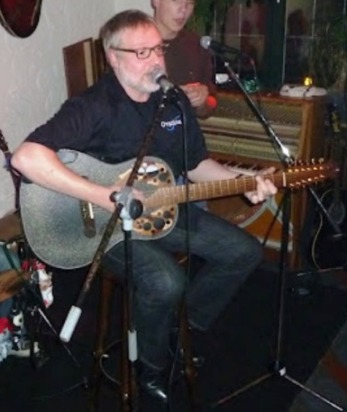 Joined: May 2011 Posts: 758
Location: Muenster/Germany | Bigger bolts are always better. |
|
|
|
 Joined: June 2012 Posts: 2330
Location: Pueblo West, CO | Ovation actually went smaller for the 50th CL. I haven't taken these out, but they look like 10-24 socket head screws. 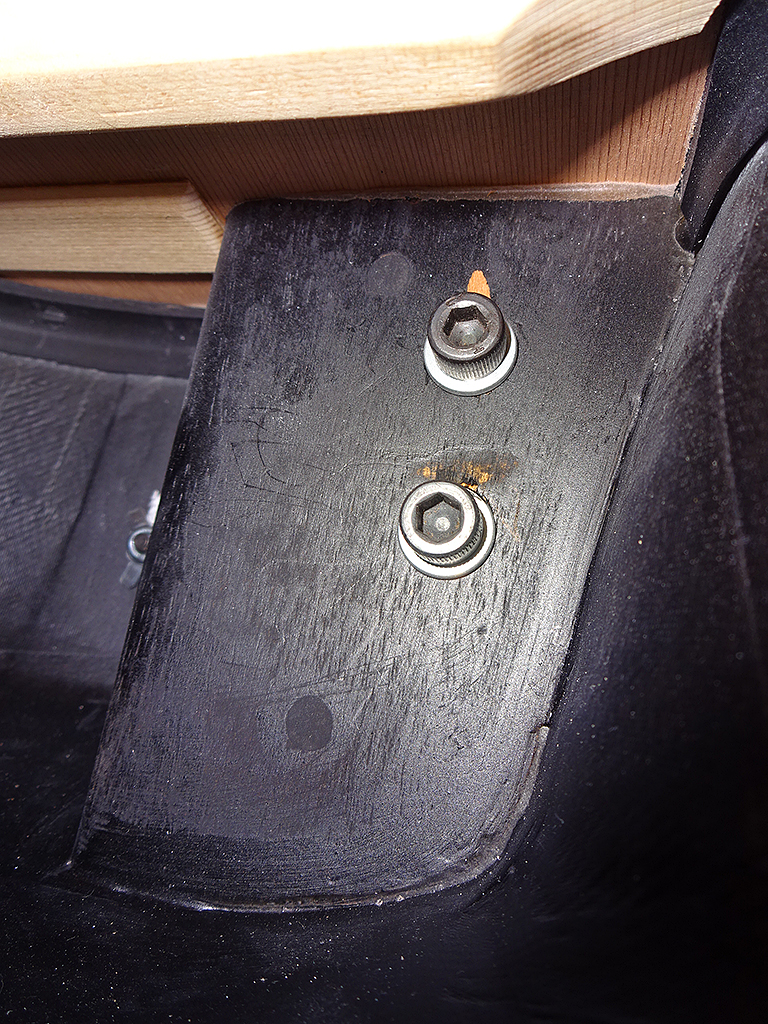
|
|
|
|
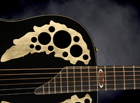 Joined: October 2012 Posts: 1072
Location: Yokohama, Japan | 2wheeldrummer - 2020-08-09 10:03 AM
Oldvation very cool work I hope Arumako sees this he'd dig it I believe he changed a celebrity from dovetail to bolt-on,what type of heat gun did you use to loosen the neck I have a couple guitars that need work and am debating trying to do the neck re-sets myself.
"Cool work" indeed Oldvation! Thanks for the detailed documentation. You're getting such great help and encouragement from the heavy hitters at the OFC, I've just been enjoying your project. I love your bolt drilling jig and the tenon joint protector. The jigs I used were far more archaic than yours, though. I've been through five Celebrity bolt-on conversions to date; and they provide great stability and ease of maintenance. My first conversion was for a CC-247, and I used two M6 steel bolts which are very close to the .25" bolts you used. 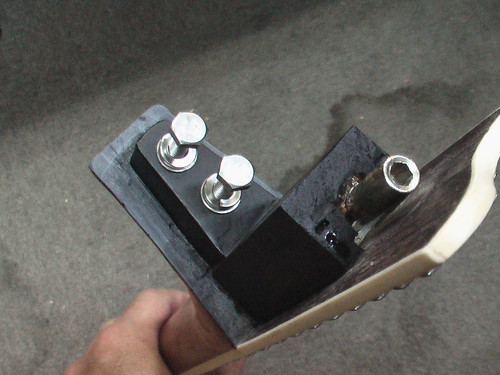
Like you, I found this configuration to be overkill; so for my next conversion, a CS-249, I used two M4 (about .14") Allen bolts (like Dan's 50th CL) that worked just as well to secure the neck. 
They were a bit lighter and believe it or not, the difference in balance is slight but noticable. It could be that Ovation used the .25" bolts back in the day, just because they were cheaper and more readily available. At least for my locality in Japan, the M4 allen wrench bolts and inserts were expensive specialty products twenty years ago, and unfinished M6 bolts/inserts were much easier to find. By the way, one M4 bolt/insert combination has plenty of holding power for super shallow conversions. It looks like you still have a ways to go; but with all the help you're getting at the OFC, you definitely can't go wrong. Thanks for sharing. I know what you mean when you say, "What FUN!" Carry-on, carry-on...
Edited by arumako 2020-08-16 12:29 AM
|
|
|
|
Joined: December 2004 Posts: 572
Location: Denmark | A shim of some kind to distribute the load on the plastic (Lyrachord?) surface and to avoid the screw "digging in" might seem proper. |
|
|
|
Joined: May 2011 Posts: 81
Location: Ozark, Arkansa | TPA, thanks for the suggestion, but the inserts that hold the top down will not be near the SMC Lyrachord material of the bowl.
The small blocks that hold the inserts will be separate from the kerfing, and slightly thicker to accommodate the inserts. The kerfing will not be traditional scored kerfing, but thin strips laminated over one another, much like perfling. The blocks will be tapered, wider at the bowl edge, and narrower on the inside edge, allowing the strips to overlap slightly to help secure the blocks.
Like I said, this has been a while in the planning, and it continues to evolve as I think through various aspects of the design. So I am always interested in input and suggestions. Kind of like community brain-storming, which I think is the way Ovation designed the original concepts for their cutting edge guitars, incorporating lots of thinking and research from many resident geniuses.
I can't wait until all this planning is playable!
Edited by Oldvation Guy 2020-08-18 8:06 AM
|
|
|
|
Joined: December 2004 Posts: 572
Location: Denmark | Well actually I was thinking of the screws for the neck. An in reviewing the thread I realise that I might have messed up a bit, because the photo that triggered my comment was actually the small metric M4 screws used by arumako in his guitars. Sure the M4 screw will hold but one also have to consider the surface pressure and shear friction under the relatively small head of the socket head screw.
You seem to use a bit bigger screws with bigger heads and with a shim (toothed?) underneath..
Edited by tpa 2020-08-18 2:03 PM
|
|
|
|
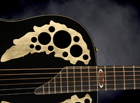 Joined: October 2012 Posts: 1072
Location: Yokohama, Japan | tpa - 2020-08-18 4:00 AM
Well actually I was thinking of the screws for the neck. An in reviewing the thread I realise that I might have messed up a bit, because the photo that triggered my comment was actually the small metric M4 screws used by arumako in his guitars. Sure the M4 screw will hold but one also have to consider the surface pressure and shear friction under the relatively small head of the socket head screw.
You seem to use a bit bigger screws with bigger heads and with a shim (toothed?) underneath..
You're absolutely right tpa. The smaller head of the M4 allen screw can be a risk. A standard washer and locking washer should be included in the assembly to make sure the pressure is distributed over a larger surface area. I converted a CC257 SSB Celebrity with one M4 screw/shim including the washers for a friend an year and a half ago, and the neck has not moved at all. |
|
|
|
Joined: May 2011 Posts: 81
Location: Ozark, Arkansa | This is the last pic I will post on this thread. Here is a shot of the Ultra 1527 with a drilling template top on it, hence no sound hole or bridge. This will be used to drill holes for the mounting screws of future tops. I picked this up in Dallas a couple of years ago for experimenting, and it has been sitting in the closet waiting patiently to be reborn as my prototyping guitar.
I want to experiment with bridge, bracing, kerfing, and top designs. This will allow me to do that just by removing the screws from whatever top I have on it at the time.
I am not done with the mounts or kerfing yet. I will start a new thread when I get more done on it, but I thought I would let you see what I have been working on.
Edited by Oldvation Guy 2020-09-02 9:52 PM
(IMG_1793.jpg)
Attachments ----------------
IMG_1793.jpg (64KB - 0 downloads)
|
|
|