|
|
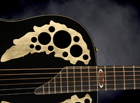 Joined: October 2012 Posts: 1072
Location: Yokohama, Japan | Belated Happy New Year OFC! I was fiddling around with my Celebrity iDea, and just got fed up with the high action and over all assembly quality and decided to disassemble her in preparation for a possible summer project. This "made in asia" guitar was not assembled particularly well and it needed a neck reset from the get go.

I love the idea behind the iDea, the design, the mp3 recorder, just attracted me from the beginning. My son first got his new, and despite having very close serial numbers the quality of our instruments were vastly different. Of course, I bought mine used and that would certainly be a consideration, but I've been wanting to do a neck reset on her since I first got her... Several years back, when I first got the guitar I contacted Kaman to see if they could provide me with a schematic of the neck joint, but they couldn't. From inside the bowl, the joint looks unusual, and I didn't want to ruin the guitar, and I looked all over the web to see if there were any pictures or neck resets done by others to no avail. So this is not really a thread about a project, but I just wanted to share pics of the joint just in case someone out there needed to do a neck reset on one of these iDeas. I've added comments that I thought might be helpful... 
Unlike other Ovation neck joints I've encountered in the past, this one is NOT Lyrachord! It is just a wood block glued to the Lyrachord bowl. An attempt at cost cutting, weight reduction or both? Hmmm...
As is the case with all made in Asia Os that I've seen, this one has an enormous amount of adhesive build up. I wonder if that is one of the Hysol adhesives? This neck was a bear to remove requiring tons of heat, some boiled water, and lots of patience. My poly-bag method did not work at all! 
From this shot, I can tell that the sound board is solid spruce. That's been a bit confusing as the Ovation website says "laminated spruce" and the box that the guitar came in says "solid spruce." Well there you have it, "solid spruce." The cavity kind of looks like the Elite T style cavity, but the supporting block under the neck is much smaller requiring some adhesive under the tip of the fretboard. 
Fortunately, the neck alignment on this one is straight... 
Neck block material is assembled to keep the neck on the guitar. Not exactly clean but it gets the job done. I am definitely going to convert this one to a bolt-on! 
You can tell from this shot that the bottom of the neck heel has the usual black plastic plate on it. Peeling some of the paint off showed a relatively nice looking mahogany (Nato) material for the neck...I think, I'm gonna go to school on Dan's 1617 neck re-finish and finish this neck with a natural color. So, this dissassembly, if nothing else, has revealed to me that the materials used on the CC54i were pretty good. Even the sound board doesn't look all that bad from the inside of the bowl. To make this guitar a real performance guitar, I'd have to re-think the pseudo-Quintad bracing that is used and completely revamp the bracing, but that will be for another thread, perhaps in the summer. I hope this thread might be of some use for anybody that needs to consider or perform a neck reset on an iDea. I'll post more pics after I get the joints all cleaned up. I love the BFLG!
Edited by arumako 2016-01-15 11:44 AM
| |
| |
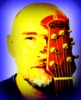 Joined: August 2007 Posts: 1008
Location: Tuscany, Italy | Thank you Arumako for sharing this. I'll surely follow your progress with interest. | |
| |
 Joined: June 2012 Posts: 2330
Location: Pueblo West, CO | The manner in which the neck attaches to the body is woeful.
Sadly, it's construction techniques like this that has caused Ovations to have a less-than-stellar reputation with luthiers.
Luthiery is all about precision wood-working. What I'm seeing here reminds me of the construction techniques I've seen in Chinese-built almost-ready-to-fly (ARF) model airplanes.
We called them, 'Basically Almost-Ready-To-Fly. (BARFs)
Edited by DanSavage 2016-01-17 7:51 AM
| |
| |
 Joined: June 2012 Posts: 2330
Location: Pueblo West, CO | arumako - 2016-01-15 9:28 AM Unlike other Ovation neck joints I've encountered in the past, this one is NOT Lyrachord! It is just a wood block glued to the Lyrachord bowl. An attempt at cost cutting, weight reduction or both? Hmmm... As is the case with all made in Asia Os that I've seen, this one has an enormous amount of adhesive build up. I wonder if that is one of the Hysol adhesives? From this shot, I can tell that the sound board is solid spruce. You can tell from this shot that the bottom of the neck heel has the usual black plastic plate on it. Peeling some of the paint off showed a relatively nice looking mahogany (Nato) material for the neck...I think, I'm gonna go to school on Dan's 1617 neck re-finish and finish this neck with a natural color. Chinese-assembly is all about cost-cutting. No one looks to China for quality. Probably some sort of AMG. (Asian Mystery Glue) Since you don't know the composition of the glue, be very careful about grinding it. You don't know what sort of harsh chemicals will be in the dust. And, a very thick solid spruce top, at that. If the neck is only painted, then you'll probably be able to get away with simple hand-sanding. But, if it's got a thick coat of polyester resin, as did my 1617, you'll save a lot of time by using these Dremel buffs. (See: 511E EZ Lock Finishing Abrasive Buffs - 180 & 280 grit) I used the lighter colored one. (180-grit) 
Edited by DanSavage 2016-01-17 8:06 AM
| |
| |
Joined: November 2002 Posts: 3646
Location: Pacific Northwest Inland Empire | They work great for cleaning the latches & aluminum bands on the OHSC, too! I've restored some pretty grungy critters, over the years. | |
| |
 Joined: June 2012 Posts: 2330
Location: Pueblo West, CO | Good to know.
I might add that when using them to remove the finish from wood, it takes a light touch otherwise they will put grooves into the wood. | |
| |
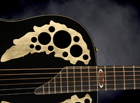 Joined: October 2012 Posts: 1072
Location: Yokohama, Japan | @ marenostrum: You're welcome! I always appreciate your interest and comments! @ DanSavage & seesquare: Thanks for the helpful comments and suggestions...
So I was able to get the neck block and joint cleaned up. Like Dan said, this Asian O is not exactly the luthier's dream. No wonder why so many luthiers in Japan refuse to work on Celebritys. A little cleaning revealed some serious concerns. The first was the underside of the fret board. When the neck block was cut to accommodate the truss rod, they inadvertently cut into the fret board. There is also a deep groove running along each side of the neck block running parallel to the length of the neck. It looks like the neck block was too big, so they cut it down to size after installing it onto the fret board. These grooves and "cut" have weakened the fret board quite a bit. I may have to fill it with Hysol 9462 or replace the neck block altogether. The heel of the neck is a bit messy, but is in working order... 
The joint cleaned up nicely too. I opted to heat and spatula the adhesive out of the joint. As Dan mentioned, it was kind of hard to tell what kind of toxicity the adhesive had, and I thought it might be safer to do it this way; however, I had second thoughts as I worked the glue off...the stuff just smelled horrible, but not like burning plastic, resin or polyurethane. It smelled like...poop! Really, nasty smelling stuff. Once it heated up it came off pretty clean and crumpled off. The problem seems to be that this guitar was assembled with a lot of this glue and the glue itself seems to be designed into the "intended" structural integrity of the neck/body joint. Not a good idea... 
The entire lower portion of the mortise joint is filled with glue. I dared not dig deeper as the whole neck support block might pop-off of the bowl. The next picture shows that the adhesive is used as a filler to hold the two wood blocks used to support the neck block too. I suspect one-day in the trunk of your car on a hot summer day, and this baby is going to need a neck reset... 
However, inspecting the entire assembly shows that I can turn this into a fully bolt on neck without using any adhesives. That will make it easy to perform a neck reset if it ever becomes necessary. The only quid pro quo is that I'll have to extend the neck block supporting the fret board to the tip of the fret board, and make accomodations on the sound board to allow the extended neck block to fit on the body... 
Of course, that is probably going to make the guitar much heavier in the final analysis...still, it is probably worth a shot. In addition, I thought I might change the bridge while I was at it. The original iDea bridge is much smaller than the 1868 bridge. They have equal depth, but have different breadth. The O enthusiast can tell them apart, but for what its worth, the iDea bridge is to the right and the 1868 bridge to the left. 
It's also interesting that the iDea bridge uses no position marking pins. Another cost cutting measure no doubt. This 1868 bridge is a spare that I have sitting around. So, I'll be installing it on to the iDea. I'll have to move the bridge forward toward the neck on the guitar by about 1.5mm to ensure that proper intonation is maintained. 
I think the iDea will look pretty good with the 1868 bridge. Since, I'm planning on swapping tops completely, I don't imagine I'll get to this until the summer, but I've decided to sand-off the paint to see what the solid spruce top looks like. If it looks pretty good, I might just keep the top, reconfigure the bracing on the sound board, add some bling, and put her back together. We'll see how it goes!
Edited by arumako 2016-01-21 10:18 AM
| |
| |
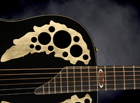 Joined: October 2012 Posts: 1072
Location: Yokohama, Japan | Thrilled to see all the great stuff going on at NAMM 2016! Thanks for all the OFC and FB posts. DW's publicist, Elizabeth's comment was so nice, and xraiderman's presentation of the 40th Anniversary Bear Claw Adamas was really something special! Of course, I couldn't keep my hands off of the CC54i Project after all this excitement; and so, I limited myself to 1 hour to see how far I can get... Grabbed my trusty Black and Decker 7448 Sheet Sander, some goggles, a mask (ya gotta use a mask for sure!) and vacuum cleaner to see how far I can go... 
For solid body electrics, I usually use heat or chemical removers, and the black polyurethane finish on my 1868 peeled off easily with heat, but this looked like some kind of special resin; and so I played it safe and went with my sander. The "platinum" finish came off unevenly, and it was slow going and a bit worrisome; however, once I got down to the primer, the surface seemed to really level-off and the material began to come off more quickly and evenly. Fifty minutes into the sanding, I had gone through two 60-grit "one-third size" sanding sheets, and most of the "platinum" color was gone. 
By "clean-up" time, the primer was thinning out nicely and evenly. You can't really tell from this pic, but the sound board is becoming quite visible and looks suprisingly good. As a matter of fact, it looks so good, that I'm seriously considering just keeping the existing sound board, and reconfiguring the bracing. As Dan mentioned, the sound board is quite a bit thicker than normal and I should be able to sand it down by .10 to .20 millimeters. Combined with a thinner finish, less restrictive bracing, and a properly assembled neck...this CC54i makeover should be quite thrilling! Still debating what kind of finish to put on this one. Definitely going to give it some bling, but maybe black wash and black burst with natural maple bindings and black-gold-black purfling? Oh man, seeing all those 50th Anniversary Os just really makes the creativity run wild and $$$!
Edited by arumako 2016-01-23 9:40 AM
| |
| |
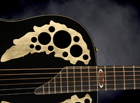 Joined: October 2012 Posts: 1072
Location: Yokohama, Japan | Removal of the finish came to a screeching halt a few days ago, when the mounting pad on my Black and Decker 7448 came loose in a big dramatic way (thankfully no harm came to the iDea). I've been using this thing for years and I figured it was time to invest in a new sander, but then I thought maybe Hysol 9462 would be able to handle this kind of load...wouldn't hurt to try...so, I broke out the powerful adhesive to glue the viberating sand paper mounting pad back onto the sander...
Now, holding a sound board onto a guitar is one thing, but holding a sandpaper mounting pad on a vibrating sander? "Naw, no way..." right? Well, I glued the pad back on, waited 48 hours, and do you know what? This Hysol stuff is monstrous! The pad is secure and I was able to continue without investing in a new tool! This stuff must be from Krypton or something...just unbelievable! Thanks for introducing this stuff to me Dan!
So what does an iDea guitar look like under the platinum finish? Well, nobody cares (lol), but I'm gonna share anyway - here it goes... 
I was surprised. I knew the spruce top was solid, but I figured they would not be "book matched" or have knots, pits and other irregularities filled with wood filler, but this looks clean, with nice evenly spaced grains and apparently book-matched! The matched pieces of the sound board look to be glued properly and securely. 
The sound board is apparently ungraded (not an A or AAA grade or anything like that), but over all it looks very nice. Unfortunately, there is one small edge of the sound board that was gouged and filled with some kind of glue. probably CA glue. I may be wrong, but I suspect that 20 years ago, this guitar would not have made if off of the production line. Defects like this would render the guitar a "2nd", "Refurb", or an outright reject - perhaps a reflection of Fxxxxr's quality control management philosophy. 
However, in all honesty, I don't think my guitar repair abilities could do much better at making a new, clean sound board (hoping to attain Dan's level of expertise in the future, but that will be many projects down the road!); and so, I think I'm going to keep the top and go for the rebrace, refinish and reassemble strategy. She does look pretty good with the bridge in position... 
I'm kind of getting excited about this iDea. Next step is to strip the neck down to bear wood...I wonder if I can make the headstock a slot head? I've always wanted a slot head, but there doesn't seem to be enough space. Well for now, what color? Natural, black, wine-red...to sunburst or to not Sunburst? Any thoughts? 
Just a little bit more work and the disassembly will be completed! Very cool!
Edited by arumako 2016-01-27 10:33 PM
| |
| |
Joined: December 2015 Posts: 41
| I have one of those Ovation Tangent guitars in black, from 2002(?), before Fender bought them. I've been curious as to what it would look like with the black removed, but it sounds surprisingly great as is, so I don't want to mess with a good thing.
It's interesting to see a stripped, similar-looking model. | |
| |
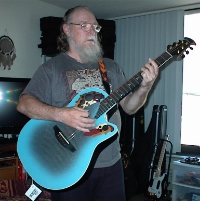 Joined: September 2006 Posts: 10777
Location: Keepin' It Weird in Portland, OR | Ken, I once owned a CC54i iDea.
I first was told that it had a "laminate" top.
But the box said that it had a Solid Top...
I could never really tell because of the opaque finish.
This is a truly educational thing that you are showing us.
Thank You.
| |
| |
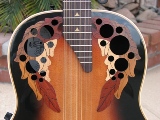 Joined: November 2013 Posts: 164
Location: Phoenix, AZ | Arumako,
Great job! Thanks for taking the time to share your project, very interesting and educational.
Probably difficult to pull off, but a "Sunburst" paint job with black on the outside would look great.
This would show off the surprisingly nice wood grain, while covering the defect along the outside. | |
| |
Joined: December 2004 Posts: 572
Location: Denmark | Personally I would not sunburst. At least not with a black outer as I doubt that it would be a match to the soundholes. But some transparent finish to show the grain. A while back I had a Celebrity with a -8T (Transparent blue) finish which was kind of nice to look at, but maybe a bit too colorful to such a nice grain. A semi transparent version of "Under the Wave off Kanagawa" (http://www.metmuseum.org/collection/the-collection-online/search/45434) would also make a nice top decoration with a matching headstock.
Edited by tpa 2016-01-28 4:53 PM
| |
| |
 Joined: June 2012 Posts: 2330
Location: Pueblo West, CO | Looking good, Ken.
You're quickly becoming the go-to guy for Ovations in Asia. Pretty soon, all the luthiers who don't want to work on Os will be sending the work in your direction.
Be careful. It sounds like you're going to soon become a victim of your own success.
WRT converting the peg head to a slotted, you probably won't be able to do that because the wood is too thin to mount the tuners on the side.
So, if I understand correctly, you're going to rebrace the top with it still attached to the bowl? What brace pattern are you planning to use?
Dan | |
| |
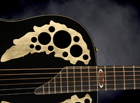 Joined: October 2012 Posts: 1072
Location: Yokohama, Japan | Hey guys, thanks so much for taking the time to comment! I really appreciate your input! @Explorer - those Tangent guitars are cool, and if it ain't broke, don't mess with it! @OMA - I saw the thread from back when you first bought your iDea guitar. I think I saw some pics on photobucket too. I am learning so much from this dissassembly, and the more I work on this guitar, the more I am convinced it can be a pretty great instrument
@Lonnie - I've made a bunch of photo shop renditions of a sunburst and just can't seem to get it right. WRT the gouge in the sound board, I think if I add binding and purfling, I'll be able to cover the gouge up nicely.
@tpa - I wish I were an artist capable of a semi transparent version of "Under the Wave Off Kanagawa" with matching headstock! I guess some kind of semi transparent iron-on might be the only way to pull that off!
DanSavage - 2016-01-29 3:51 AM You're quickly becoming the go-to guy for Ovations in Asia. Pretty soon, all the luthiers who don't want to work on Os will be sending the work in your direction. Be careful. It sounds like you're going to soon become a victim of your own success.  Dan NOT! You are too kind Dan, but thanks for the encouragement. And yes, I am planning on replacing and re-arranging the bracing without taking off the top. The 1868's Quintad bracing is quite the marvel of engineering. It acts almost like an equalizer providing the guitar with that unmistakable O voice. So, I'm planning on arranging the iDea's bracing as much like the 1868's Quintad bracing. My 1868 is to the left and a photoshop rendering of my CC54i bracing pattern is to the right...
I've been studying the iDea's bracing pattern and was a bit bewildered by the size of the cross brace (blue) that spans the entire width of the sound board...why so big, why so thick? I haven't removed anything yet, but the more I look and feel the bracings of the iDea, the more I am convinced that they are made from pine. My Celebrity CC247 has spruce braces, but I'm almost sure that part of the cost cutting measures for the iDea included the exclusive use of pine bracings. It's not the first time, I've seen this in an Asian made guitar, but I never thought I'd find this in the iDea! Tragic... 
The braces on the iDea are longer than the braces on the 1868; and so, I am going to shorten them up to match the length of the 1868. I also want to angle the vertical middle brace in the iDea to match the 1868. The 3-Oval sound hole on the iDea hinder the braces from extending past the neck joint, but I think the neck block will do an adequate job of keeping the top from bowing into the sound board at the neck joint. The iDea also has some thin pieces of wood glued under the bridge to act as a bridge plate, but I don't think those are necessary and will be removing them with the bracing. These changes should free up the sound board to achieve better resonance. Because of the modern look of the iDea, I've decided to cut and shape bracings out of twill carbon fiber. I think Hysol 9462 will have no problems securing carbon fiber to spruce. Also, I'm going to try some 1mm thick carbon fiber sheet for binding and purfling... maybe with some abalone... I've also found a nice looking block of carbon fiber to fabricate a new bridge based on the 1868 bridge. A slothead is most likely out of the question, but a carbon fiber face plate on the head stock would be a nice match. Man, just seeing the photos of the Adamas electric at NAMM is just messing with my brains! 
But in reality, the carbon fiber components should help to lighten the guitar. They should also provide rigidity that cannot be achieved by wood bracings. They'll contrast nicely with the clean spruce top and Lyrachord bowl. My plans are to highlight the grain of the top with light brown stain that progressively gets darker near the outside edges, and finish it all with a thin gloss shellac or polyurethane finish. Hmmm, this is getting interesting!
Edited by arumako 2016-01-31 7:38 AM
| |
| |
Joined: May 2008 Posts: 1559
Location: Indiana | Really interesting, Ken. Nice work. | |
| |
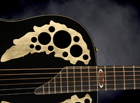 Joined: October 2012 Posts: 1072
Location: Yokohama, Japan | Thanks Jonmark Stone. I just gotta keep taking it slow to make sure I don't cause a major catastrophe! Just as I suspected all the bracing on this iDea was made from pine. I started without gloves, but after getting some serious splinters, wisdom got the better of pain, and I put some gloves on... 
Although pine is sharp and provides nice painful splinters, they aren't exactly suitable for bracing. A bit oily, heavy and flexible, they just are not the epitome of ethereal rigidity. So, that's why the cross brace on the iDea was so thick and large! And removing the bracing was quite an undertaking. I used heat, and several different sized spatula's as I couldn't quite fit the Dremel tool in the space provided by the mid-depth bowl. It took a long time, but after I was done removing half of the bracing, I just couldn't take the punishment anymore, and decided to use some boiling water. I dipped the steel spatula's in boiling water, then heated them on the iron, and worked off the braces. Just a few drops of water made a huge difference and the remainder of the braces came off without much trouble...whew. Under the sound board is quite a mess at the moment, but some fine chiseling and sanding will clean things up nicely. I did get too ambitious at one point and cut into the sound board (thankfully not a catastrophe), and this will need to be fixed before assembly. Perhaps some fiberglass and resin to fill the gaps. 
In the final analysis, the carbon fiber bracing will be installed based on this photoshop mock-up. I'm still not sure how to deal with the area with the Oval sound holes interfering with the bracing. Probably, won't even need to bother with any bracing up in that area. The Adamas bracing includes a thin cross brace under the bridge, but I'm pretty sure I won't be needing that. 
With the breathing room offered by the Quintad bracing, this iDea should find some serious resonance. So while I wait for materials to arrive, I can start working on the neck! Gotta slow down, slow down...
Edited by arumako 2016-02-02 10:29 AM
| |
| |
Joined: March 2013 Posts: 359
Location: undisclosed | Very inspiring Arumako. I have a feeling my neck on the celebrity mandolin is the same style of mounting, lots of epoxy everywhere. Interestingly its bracing also seems a bit short contributing to the slight top bow as the glue job wasn't great along with the failed glue joint on the fingerboard.
From boat building bracing strength can be tested by measuring deflection with weights on a measured length. I'm used to imperial measure so for example over a foot of length measure how much weight it takes to deflect x distance with the pine stock sizes then do the same with the carbon fiber to match it. For fine tuning increase the weights a few times to see if the range corresponds up to failure. Obviously if you want to go stronger it will be easy. Rough and tumble engineering for sure but good enough for picking. | |
| |
Joined: March 2013 Posts: 359
Location: undisclosed | Forgot to mention that with skinny braces you'll have to glue something to the top of them to keep them in column for testing. Anything thin and flat should work.
On the bracing what about spanning the soundholes and just painting them black? | |
| |
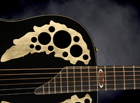 Joined: October 2012 Posts: 1072
Location: Yokohama, Japan | Thanks for the advice Cavalier! It's amazing how so many folks with expertise from so many different fields hang out at the OFC. What with Dan and his $10,000 airplanes, and your experience with boat building! You can't go wrong with that kind of advice. I'll definitely use your method to test the bracing capabilities of the carbon fiber.
Once I get the material and cut them into shape, I'll try to see what they look like if they span the sound hole...kind of like the 50th Adamas bear claw...only inside the bowl! Might be cool! | |
| |
Joined: March 2013 Posts: 359
Location: undisclosed | If you get interested there is a lot of wood and epoxy engineering done by the Gougeon brothers of WEST epoxy fame. They developed lots of testing for wood and composite strength and fatigue over repeated cycle loading. http://www.westsystem.com/ss/assets/HowTo-Publications/GougeonBook%...
Using carbon fiber bracing should allow thinner sections for the same strength improving top vibration.
One reason I get worried about top veneers in laminates is what looks cool could have impacted strength and tone, that burl or birds eye is going to affect the vibration . Quite a challenge for the manufacturer when many sales are appearance driven. | |
| |
Joined: December 2004 Posts: 572
Location: Denmark | The cross going brace may have an influence on the top stability. The mode illustrated on the below picture will be restricted: 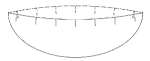
Besides affecting tonal characteristics I guess the also the tendency to bellybulge will be increased. But that doesn't mean that omitting it will be a bad solution. Especially since such stiffness is provided also by the saddle piece. It means that it will make some sense to prepare a cross going brace while you work on the other braces. This you can use as a guide for the other braces, and if You find that the guitar need it it can easily (to a person with your skills) be added.
Edited by tpa 2016-02-04 4:05 PM
| |
| |
 Joined: June 2012 Posts: 2330
Location: Pueblo West, CO | Interesting that you're going to use CF for the braces, Ken.
I'm curious why you settled on CF instead of spruce. | |
| |
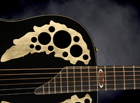 Joined: October 2012 Posts: 1072
Location: Yokohama, Japan | DanSavage - 2016-02-05 5:48 AM
Interesting that you're going to use CF for the braces, Ken.
I'm curious why you settled on CF instead of spruce.
...well the truth be known, I saw the Adamas electric and was enamored by the aluminum bridge and over all look, and thought I might use CFRP (carbon fiber reinforced polymers) for cosmetics only - like the binding...love the way carbon fiber looks on motorcycle parts and what not...
So, when my brain finally caught up with my imagination, I took a look at the data sheet provided by Cavalier and noticed that all the measurements I was looking for was on the Net (just amazing). So here's what I've found (probably some discrepancy and inaccuracy in my data, but FWIW...)
I tried to accumulate strength data for bracing materials as follows (http://www.wood-database.com/ has some excellent information about all kinds of woods):
White Pine = WP; Sitka Spruce = SS; Yellow Birch = YB; Carbon Fiber = CFRP
...and compared 6 physical characteristics of the material:
Specific Gravity: WP - 0.35; SS - 0.40; YB - 0.62; CFRP - 1.5
Density (g/cubic cm): WP - 0.400; SS - 0.432; YB - 0.689; CFRP - 1.585
Compressive Strength (psi): WP - 4,800; SS - 5,610; YB - 8,170; CFRP - 15,954
Bending Strength (Gpa): WP - 0.0593; SS - 0.07; YB - 0.114; CFRP - 10
Stiffness Strength or MOE (Gpa): WP - 8.55; SS - 11.03; YB - 13.86; CFRP - 135
Specific Strength [Pa/density(kg/cubic meter)]:
WP - 148,250
SS - 162,037
YB - 1,661,829
CFRP - 44,164,037
Since you're into model plane building, I'm sure you already know this stuff; but I think what this means is that CFRP is too strong. The material has excellent strength-to-weight (specific strength) characteristics, but it's just too stiff! I was thinking I could fabricate a bridge out of a piece of 3K Twill 70% CFRP block that I have 2"x7"x0.5"; but since a bridge is essentially a "brace", that will stiffen things up quite a bit. Combined with CFRP braces...maybe too stiff?
Still, I am super tempted to experiment to figure out just how this will affect the resonance of the sound board. Will probably need to use a lot of shorter smaller braces to make certain the various modulus movements of the sound board are not overly hindered by the stiffness of the CFRP. As a matter of fact, reproducing the Quintad bracing of the 1868 with CFRP may ruin the resonance of the spruce top altogether...
Then there's the issue of getting a 2mm thin piece of CFRP to adhere flush to the sound board...(not to even mention that 2mm might be too thick for CFRP bracing!) just a lot of hurdles to get over at this point. While I was researching this stuff I ran across a guitar that uses "balsa/CFRP" laminates for bracing, that looked very very cool, but all that to say, I think I'm just way in over my head! This is another Winnie the Pooh moment for me, "Think, think, think..."
Edited by arumako 2016-02-05 11:01 PM
| |
| |
Joined: March 2013 Posts: 359
Location: undisclosed | Maybe you should make a few cigar box guitars to compare brace size. Carbon fiber uni would use smaller braces and fewer for the same strength for sure. I think you'd have to take into account that the new material could need a new pattern to take advantage of its properties. Perhaps a variation on the double bars or single x used on archtops? Interesting to see what you come up with there. Careful though, as I remember some of those honey tree efforts came to a sticky end. | |
| |
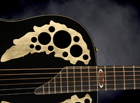 Joined: October 2012 Posts: 1072
Location: Yokohama, Japan | Cavalier - 2016-02-05 2:51 PM
Carbon fiber uni would use smaller braces and fewer for the same strength for sure. I think you'd have to take into account that the new material could need a new pattern to take advantage of its properties. I think you're right Cavalier. Not one to give-up so easily, I've outlined a basic bracing pattern based on the Quintad bracing with 3 main bracing pieces (in orange) and 3 tone braces (in green). 
The bracing surface area is 34% lower to "soften-up" the rigidity of the CFRP braces and bridge (may need to route under the bridge in strategic areas to relieve it from it's "hyper" rigidity as well). The braces will be much shorter and thinner too. T2, T3 & T4 (un-marked) will be no more than 3mm in height, 2mm wide at the base and tapered to 1mm at the top. B2 & T1 are designed to jump over the bridge area to make sure the extreme rigidity is not killing resonance. It's going to be difficult to bring out the bass response in the guitar, so I'm leaving the bass area as clear as possible. Bracing will be added if necessary in the areas shaded in red. Frankly, I have no idea how this will all sound, but the spruce top has a pretty sweet tap tone, and with some tweaking, I might be able to get this thing to sound half-way-decent. Even if it doesn't work out, I sure am learning a bunch! Great fun!
Edited by arumako 2016-02-06 10:19 AM
| |
| |
Joined: March 2013 Posts: 359
Location: undisclosed | Looks good! I What do you think about keeping the braces recessed under the soundhole? Visually they would be less noticeable. I'm not sure filling in the notch will do much right there.
Tone wise I'd expect carbon bracing to increase the high end definition and perhaps sustain. It should be possible to try different configurations or materials if it doesn't work out, if your nerves can stand the removal process!
Edited by Cavalier 2016-02-06 10:35 AM
| |
| |
 Joined: June 2012 Posts: 2330
Location: Pueblo West, CO | arumako - 2016-02-05 8:55 PM
White Pine = WP; Sitka Spruce = SS; Yellow Birch = YB; Carbon Fiber = CFRP
...and compared 6 physical characteristics of the material:
Specific Gravity: WP - 0.35; SS - 0.40; YB - 0.62; CFRP - 1.5
Density (g/cubic cm): WP - 0.400; SS - 0.432; YB - 0.689; CFRP - 1.585
Compressive Strength (psi): WP - 4,800; SS - 5,610; YB - 8,170; CFRP - 15,954
Bending Strength (Gpa): WP - 0.0593; SS - 0.07; YB - 0.114; CFRP - 10
Stiffness Strength or MOE (Gpa): WP - 8.55; SS - 11.03; YB - 13.86; CFRP - 135
Specific Strength [Pa/density(kg/cubic meter)]:
WP - 148,250
SS - 162,037
YB - 1,661,829
CFRP - 44,164,037
Since you're into model plane building, I'm sure you already know this stuff; but I think what this means is that CFRP is too strong. The material has excellent strength-to-weight (specific strength) characteristics, but it's just too stiff! I was thinking I could fabricate a bridge out of a piece of 3K Twill 70% CFRP block that I have 2"x7"x0.5"; but since a bridge is essentially a "brace", that will stiffen things up quite a bit. Combined with CFRP braces...maybe too stiff?
I think the stiffness figures are for a given size. Yes, you're correct. I am familiar with CF.
I think using CF for braces would work fine, but you would want to do one of two things. Either, use very thin CF laminated to the wood (top and/or bottom) or, if you use CF alone, use very thin pieces so that you get some flexibility to the top.
If you google for carbon fiber guitar braces you'll see that there's a lot of people experimenting with CF.
For testing, the first thing I would do is simple deflection testing. Take a piece of spruce that's the size of a brace and clamp one end to the work bench. Next, hang a weight off the free end and measure how much it deflects. Then, do the same thing with a piece of CF and use different thicknesses until you get the deflection you desire.
I don't think there's anything inherently wrong with using CF for a bridge. Yes, it will be stiffer than wood, but if you want it to have the look of CF, but the flexibility of wood, just reduce the thickness until you get what you want.
Even though CF is stiff, it will still bend. It's just stiffer than most other materials for a given size. What makes CF popular is that you can reduce the size which reduces the weight, but still retain the same stiffness. I'm sure if you use the same principle for your braces, your experiment will be successful.
Carry on.  | |
| |
Joined: December 2004 Posts: 572
Location: Denmark | Since the body is still on the soundboard you have the option of using a speaker and a sinus generator and sweep through a frequency interval to check for resonant modes to see how the braces change behavior. Another property to check is temperature expansion. You will not want the top to move depending on temperature.
Edited by tpa 2016-02-06 5:44 PM
| |
| |
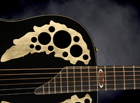 Joined: October 2012 Posts: 1072
Location: Yokohama, Japan | Thanks for the advice regarding the cross-going brace and bellybulge, tpa. On my 1868 the sound board curled up at the sides because there was no cross-going brace. Kind of the opposite of a bellybulge. I'm going to cut and shape some small CFRP braces that can be added. I think if I keep the cross-going brace low and thin, it will work out pretty well.
And your suggestion about the sinus (the same as a tone generator, right?) generator is also great advice. As a matter of fact, it will help me to be concise about my brace placements and shapes without putting strings on the guitar! They even have on-line tone generators that work pretty well. Which means I'll want to pre-cut and shape a variety of braces to test.
Dan, thanks for the verification. I was afraid the CFRP material was way too stiff to be practical; Do you use carbide tipped tools when working with CF?
Thanks for the interest and the tips folks! I'd be lost without the BFLG! | |
| |
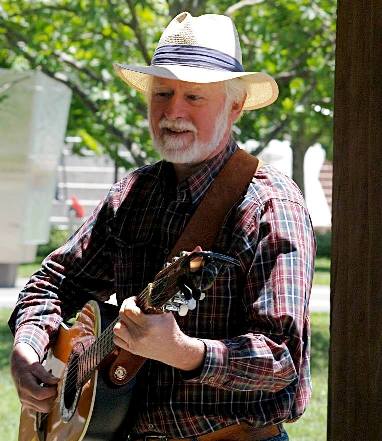 Joined: September 2012 Posts: 813
Location: Thredbo, NSW, Australia | Double post
Edited by BanjoJ 2016-02-07 12:00 AM
| |
| |
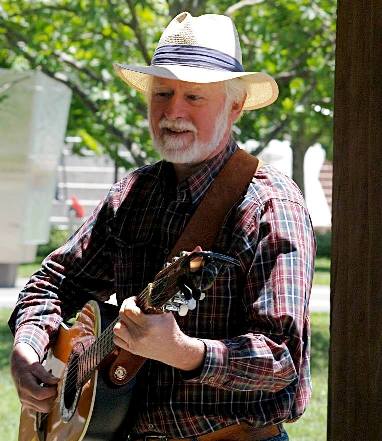 Joined: September 2012 Posts: 813
Location: Thredbo, NSW, Australia | I was interested to see the bracing in my ute. The braces vary in height along some braces, and the long braces are different to the short braces.
(Braces-07S.JPG)
(Braces-08S.JPG)
(Braces-09S.JPG)
Attachments ----------------
Braces-07S.JPG (60KB - 0 downloads)
Braces-08S.JPG (61KB - 0 downloads)
Braces-09S.JPG (65KB - 0 downloads)
| |
| |
Joined: December 2004 Posts: 572
Location: Denmark | Yes, tone generator. Nowadays I believe You can find a tone generator on-line to work with your PC sound card. | |
| |
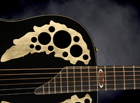 Joined: October 2012 Posts: 1072
Location: Yokohama, Japan | Cavalier - 2016-02-05 2:51 PM ...Careful though, as I remember some of those honey tree efforts came to a sticky end. Hoping to avoid the sticky end, and there is still a long, long way to go, but materials are prepped and in order... 
The CFRP bridge and braces are going to be especially challenging; but if I don't botch it up, the purfling and binding should work out pretty nicely. Maybe a fall 2016 completion. Gonna take it real slow... | |
|
|