|
|
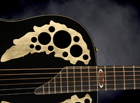 Joined: October 2012 Posts: 1090
Location: Yokohama, Japan | I'm not a Luthier, and so, I'm not sure if this is the right forum for a post like this, but I began my 1117-4 repair in earnest and thought I'd document it. "My Guitar" forum seemed as appropriate, but most repairs and reworks seem to go down in the BFLG. Please forgive me if this is in the wrong place... I thought about waiting for Mr. Budny's shop to open, but as it turns out the airfreight from Japan to NH and back would just be so expensive. And DanSavage, MWoody, FlySig, Mark in Boise and SOBeach, all provided such helpful and inspiring information, I figured I should give it a whirl. Hence I've begun my 1117-4 Repair Project (albeit slowly). After a lot of thought and dry runs, I found that there was very little space under the bridge to get the CA glue under there evenly, and I just could see myself misaligning the bridge and botching up this repair. So I figured, I'd better take the whole bridge off...not sure that was the right thing to do at this point... My 1117-4 is masking taped-up and ready to go! 
The hot spatula and iron trick...I needed to go really slow because the soundboard was splintering between the wood and the finish... 
Two hours later, the bridge finally came loose and off! Whew...but notice the peeling wood. And there are those dowels that line up the bridge perfectly. Nice! 
Per the preliminary evaluation, the bridge was glued onto the finish. I suspect CA glue was used to do this job. Most of the bottom of the bridge is covered with hard finish. Now, I need to figure out if I should CA this bridge back on or clean up the soundboard, and shave the finish off of the bottom of the bridge and use hyde glue... 
The peeling soundboard is kind of scary, but this way I can get to the cracks and areas where the finish is peeling around the bridge. I'm definitely NOT progressing with confidence at this point, but I am going to really take my time and make sure I at least give this beauty a fighting chance. I'm sorry if my work makes you cringe! |
|
|
|
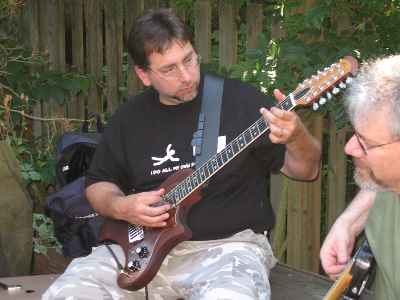 Joined: December 2003 Posts: 13996
Location: Upper Left USA | You have to try!
Looking good! |
|
|
|
 Joined: June 2012 Posts: 2333
Location: Pueblo West, CO | Even the most experienced master luthiers started out as a beginner.
Can the wood fibers still attached to the soundboard be pushed back into place?
If so, does it present a reasonably level surface?
The choice to use epoxy, CA or hide glue will depend on the smoothness of the two surfaces to be joined.
Hide glue has poor gap-filling ability. Same with thin CA.
Medium CA and epoxy are better at filling in gaps in the joints.
If you can fit the bridge back into place like a piece of a jigsaw puzzle, you might consider just gluing it as is instead of cleaning it off.
Since you've got the bridge off the guitar, you could use a slow-drying epoxy and the screws/nuts to help clamp it in place while the epoxy dries as was discussed on your other thread. You'll just want to make sure that you get epoxy between the peeling wood fibers. I suggest a laminating epoxy, such as Z-Poxy, which is more like a liquid than hardware store epoxy which is more like a gel.
At this point, I would not use CA as it will dry too fast to allow good alignment.
Edited by DanSavage 2014-07-22 8:49 AM
|
|
|
|
Joined: April 2010 Posts: 823
Location: sitting at my computer | arumako - The peeling soundboard is kind of scary... Yup, that is a bit "cringe" inducing. But fixable as Dan noted. Considering how that existing peeling made the bridge removal all the more tricky, I think you did as clean of a job as could possibly be done. Kudos.  Keep taking it slow and careful. btw - discovered this webpage Applause Bridge Repair done by ksdaddy. Not exactly your same scenario but maybe helpful. |
|
|
|
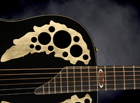 Joined: October 2012 Posts: 1090
Location: Yokohama, Japan | Again, MWoody, DanSavage & SOBeach; Thank you so much for the encouragement. My son watched me as I slowly worked the bridge off and we were both on edge the whole time...just cringing and screaming every time it sounded like wood was splintering. Finally, my daughter came down stairs, and we shrieked at the stair squeaking thinking something gave on the guitar, and we just about lost it. At that point, my son had enough, and decided he'd better get some rest...It was so hard because the soundboard was already peeling away under the bridge. I didn't know Amateur Luthiery could be hard on the heart!
"Can the wood fibers still attached to the soundboard be pushed back into place?" Yes!
"If so, does it present a reasonably level surface?" Yes!
"The choice to use epoxy, CA or hide glue will depend on the smoothness of the two surfaces to be joined."
Okay, I think I will go with Z-poxy. That should give me plenty of time to work the clamps in place. 
With the neck angle just a bit off, shaving the finish from the bottom of the bridge would bring the neck angle just about to the top of the bridge. So I am slowly evaluating what it would take to get the finish off of the bottom of the bridge. I think there is enough space to get the Z-Poxy into the splintered wood. Since the surface is still fairly flat, I should be able to clamp everything in place and secure things pretty well. The pins that are still embedded in the bridge are excellent and will enable me to line up things pretty well. ksdaddy's post was also very informative. Thanks for the heads-up SOBeach. If some tender loving care and patience can get that Applause back in shape, I think my chances are not impossibly bad. I'm sure there will be more "cringing" to come, but please bare with me. Thanks again...I'm going to wait a couple days before I proceed. I can only take so much Amateur Luthiery excitement in one day! Whew!
Edited by arumako 2014-07-23 10:08 AM
|
|
|
|
 Joined: June 2012 Posts: 2333
Location: Pueblo West, CO | Before attempting to glue the bridge into place, you should work on fixing the cracks in the sound board to give yourself as level of a surface as possible.
In looking at the above pic, I agree. It would be best to shave/chisel all the glue/finish off the bottom of the bridge to lower it so it's more aligned to the neck angle. |
|
|
|
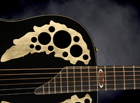 Joined: October 2012 Posts: 1090
Location: Yokohama, Japan | Okay...after getting over the trauma of removing the bridge from the 1117-4, I decided to clean up any excess finish that remained on the soundboard and the bridge. I also made a bridge clamp that goes under the bridge through the sound hole. I decided to go with the 30-minute flavor of Z-Poxy, and thin and thick CA glue to fix the cracks and fill in the finish where ever there are finish chips. Here's everything I need to finish off the project; 
Filling the finish cracks with thin CA was pretty easy (albeit a bit messy). These CA products recommended by DanSavage are really quite phenomenal (thanks DanSavage!). The difficulty was getting the glue all the way into the splintered soundboard. The splinter under the bridge went under the bridge and about 1 cm beyond! I thought CA glue would be the best to get deep into the splinter with a syringe, but CA adhere's and grips so quickly; fear drove me to use Z-Poxy. Since Z-Poxy was too thick for a small syringe, I had to push the glue in with my spatula... 
After gluing under the splinter, I first clamped the area in front of the bridge to try to squeeze the splinter together; and sure enough the Z-Poxy started to flow out of the splinter. On a side note, while I was working on filling the finish cracks, I spilled some CA glue on some Saran Wrap (plastic wrapping sheet) and I noticed the CA didn't burn through the sheet (after all it's plastic). I decided to wrap some aluminum bars with Saran Wrap and use them as clamping cauls. The CA sticks to the plastic wrap, but I can immediately tear the excess Saran Wrap away and sand and polish the finish down. Of course in doing so, the plastic wrap is sanded away as well and doesn't interfere with making a clean professional looking finish. 
During my dry runs and glue runs, I've been spilling CA and Epoxy all over the place. I'm just not used to working with these strong adhesives. I figured I'd better be cautious. Newspaper inside and around the sound hole. After clamping everything into place and after waiting about 6 hours, I added thin CA glue to further fill in the cracks, and used thick CA to fill the areas that needed filling in the finish. 
Now, I'm just going to wait 72 hours, sand and polish up the finish, and see if she's good to go... 
Still debating whether bridge screws are going to be necessary...but no matter how many times I look at her, she sure is one heck of a beauty! I hope all this works out!
Edited by arumako 2014-08-20 3:48 AM
|
|
|
|
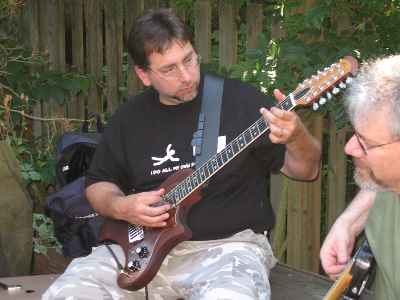 Joined: December 2003 Posts: 13996
Location: Upper Left USA | Looking good! |
|
|
|
 Joined: June 2012 Posts: 2333
Location: Pueblo West, CO | I agree! You're doing a great job.
As an aside, the 30-minute Z-Poxy is fairly thick. The Z-Poxy laminating resin forms a bond that is as strong as the 30-minute stuff, but is much thinner and could easily be injected with a syringe.
Yes, the Zap family of CA glues are really good. I've been using them for years. Same with Saran Wrap. In fact, for building my model airplanes I would tape the plans to the back side of a pane of glass, then lay down Saran Wrap to the front of the glass, then glue the parts directly to it. When the glue was dry, I just peeled the Saran Wrap off the glass, then off the wood parts, sanding away the excess glue where necessary.
Keep up the good work. I'm looking forward to seeing the completed job. |
|
|
|
Joined: April 2010 Posts: 823
Location: sitting at my computer | Nice progress arumako. It's getting there!
Good photos, and write-up too. All helpful stuff for us apprentice BFLG'rs. |
|
|
|
 Joined: January 2009 Posts: 1249
Location: Texas | This is extremely interesting to read. Thanks for wanting to share your journey. Major cudo's to Dan, Woody and SO for being available for consultation and never ending encouragement. |
|
|
|
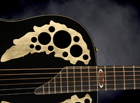 Joined: October 2012 Posts: 1090
Location: Yokohama, Japan | Thanks again for the encouragement MWoody, DanSavage & SOBeach! @DanSavage - thanks for the side-note regarding Z-Poxy's Laminating Resin. I'll definitely need to get some of that for another project I'll be working on soon. @jay - Your kind comment is most appreciated. It really is my privilege to share. Everybody at OFC has been so inspiring and helpful. Did you see DanSavage's "1619-4 Rebuild" thread under the BFLG? Priceless stuff! I hope documenting this will help some other Ovation restoration somewhere in the world. As you said, amosmoses - 2014-08-20 2:42 AM Major cudo's to Dan, Woody and SO for being available for consultation and never ending encouragement. really says it all. Tomorrow the clamps come off and the finish sanding and polishing begins!
Edited by arumako 2014-08-20 6:51 PM
|
|
|
|
 Joined: June 2012 Posts: 2333
Location: Pueblo West, CO | Speaking of the 1619-4 Rebuild thread, I should be posting more soon. |
|
|
|
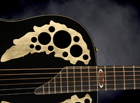 Joined: October 2012 Posts: 1090
Location: Yokohama, Japan | Seriously, one of the things I've been waiting for all summer has been to see the finished Bear Claw Spruce top 1619-4! I feel like my daughter when we first went to see "Frozen"...can't wait! |
|
|
|
 Joined: June 2012 Posts: 2333
Location: Pueblo West, CO | Your patience is about to be rewarded. It's almost done.
I posted pics and the latest updates. |
|
|
|
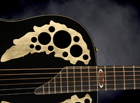 Joined: October 2012 Posts: 1090
Location: Yokohama, Japan | Inspired by DanSavage's "1619-4 Rebuild," I have pushed through to finish my 1117-4. At some points it was pretty close to "carnage," but in the end it seems to have come together rather well! The problem with novice guitar restorers like me is we just get too liberal with the adhesives! After the clamps came off, it was pretty obvious that a lot of scraping, sanding and polishing was going to be required! 
My trusty exacto blade and sharpened half-inch chisel was exactly what I needed to scrape the excess glue off of the bridge and finish...sorry to induce more cringing here! 
Since the guitar's finish is polyurethane based, I figured automotive waxing compound and polish would be (not the best, but...) the most appropriate economic solution. Here's everything I needed to get this done... 
The exacto blade is nice and flat. If I point the blade away from me, and pull the exacto blade over the finish toward me, it scrapes all the mounds down to a nice and flat condition. The sharp chisel enabled me to clean around and over the bridge where I was a bit too enthusiastic with the adhesives! I just had to work really, really slowly and softly! Once things seemed pretty settled, I added some more thin CA around the bridge. After 4 runs, the CA began to puddle around the bridge which meant (theoretically anyway) that the capillary action of the glue filled every gap around the bridge. 
Once the scrapping ended, I wet sanded using 400, 600, 800, 1200, and 2000 grit sandpaper. Then I used the 7 micron abrasive waxing compound, 2 microns and finally 1 micron... 
And then I used polishing compound to brighten her up... all the gaps and cracks have been filled and she is just glimmering! 
Now, to string her up and see how she holds up under pressure...I was a bit leary that my mixing of the Z-Poxy was a bit off, but apparently this stuff is pretty forgiving! The wrong adhesive would have rendered this project a disaster! Thanks to DanSavage, MWoody & MarkinBoise's expertise on the subject, I was spared the alternative heart wrenching scenario! Thank you, thank you, thank you! 
The string height is right at 2.2mm at the 12th fret with no buzzing! 
She's holding up under medium gauge string tension and sounding absolutely SWEET! She is everything I imagined her to be and more! 
So...thank you for all the encouragement and advice DanSavage, MWoody, FlySig, SOBeach, MarkinBoise, jay and anybody else I may have missed! Without the help of the OFC, this beautiful 1117-4 would have been in the trash! I will definitely be playing her for my next performance! Domo Arigato 10 times over!
Edited by arumako 2014-08-23 2:23 AM
|
|
|
|
 Joined: January 2009 Posts: 1249
Location: Texas | And she lived happily ever after. Bravo! That is a awesome job! Congratulations. Let us know when you are open for business. |
|
|
|
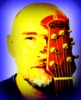 Joined: August 2007 Posts: 1008
Location: Tuscany, Italy | Bravo. Thanks for sharing Arumako. You guys make us feel adventurous in doing some home work on our beloved guitars....  |
|
|
|
 Joined: October 2005 Posts: 4071
Location: Utah | Wow! Looks amazing! |
|
|
|
 Joined: October 2005 Posts: 4071
Location: Utah | Check out this cool scraper idea from Stew Mac. Use a regular single-edged razor blade and some clear tape (Scotch Tape) which is about .002" thick. The key is to put a burr on the razor blade similar to a regular wood scraper. I haven't used this trick yet but it looks simple and effective.
http://youtu.be/rTVScFJoe24 |
|
|
|
 Joined: June 2012 Posts: 2333
Location: Pueblo West, CO | Nice job! You did a real nice job of bringing this guitar back from the brink. It's a very satisfying feeling doing work like this yourself.
Yep, you used the thin CA exactly the right way by running it around the edge and letting it wick into the glue joint and keep doing it until it doesn't wick any more.
I used Xacto blades for scraping all the time. In fact, I used my Xacto chisel to scrape the finish off the abalone purfling on my 1619-4. Sometimes I like scraping better than chiseling because it gives you more control and don't take off too much. |
|
|
|
Joined: March 2002 Posts: 15677
Location: SoCal | Great looking guitar! Congrats on a job well done..... |
|
|
|
Joined: April 2010 Posts: 823
Location: sitting at my computer | Nicely done arumako. Congrats! enjoy that "fixed-it-myself" mojo. |
|
|
|
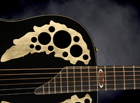 Joined: October 2012 Posts: 1090
Location: Yokohama, Japan | Just got back from vacation with the family and was very encouraged by all of your kind comments. After a week, the bridge is holding firmly - so much so, that I don't think the bridge bolts will be necessary at this point! So, thanks again, and thank you OFC!
DanSavage - 2014-08-23 7:16 AM
It's a very satisfying feeling doing work like this yourself.
Yes! It is...it's actually kind of addictive! Can't wait for my next project! |
|
|
|
 Joined: June 2012 Posts: 2333
Location: Pueblo West, CO | As near as I can tell, the only reason Ovation started adding bridge bolts was because they glued the bridges to the finish instead of the bare wood.
Though I do have to admit, I was more than a little nervous when I strung up my 1619 and tuned it to concert pitch.
Also, neither Martin, Taylor or most any other luthier bolts their bridges to the soundboard. That's because they glue wood to wood, which is much stronger than wood to finish.
As they say, if ain't broke, don't fix it. |
|
|
|
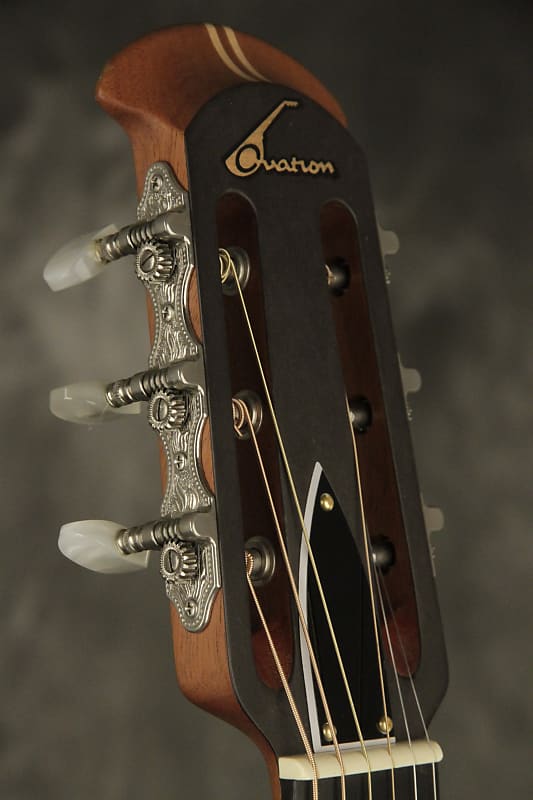 Joined: April 2013 Posts: 101
Location: NW Indiana | Wow, Arumako, what a great (and courageous) job! Congratulations! I just added a 1114 Folklore to my collection and it has several finish cracks. You have peaked my interest in having a go at a DYI repair, and I am in the hydrating phase right now. I may have to re-read your posts daily to keep up my courage. lol. Best wishes. |
|
|
|
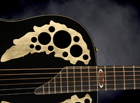 Joined: October 2012 Posts: 1090
Location: Yokohama, Japan | Thanks for the comment Cripple Rick! Wow, a Folklore, that would probably be the most sought after "O" in Japan (maybe aside from the Adamas). You never see those around over here...I don't know, a 1117-4 with the bridge already peeling off (and practically free) is kind of a "nothing-to-lose" project, but a Folklore with only finish cracks...man; have you considered sending it to New Hartford for a restoration. It may take a while with the 50th Anniversary being their 1st priority and all, but the folks at the Mother Ship are masters, and they do immaculate work for very very reasonable prices. If I was in the States, I don't know if I ever would have attempted a DIY repair...
On the other hand, of course, I'm really glad that my circumstances kind of forced the issue for my 1117-4. The guitar still sounds incredible and it would have been a tragedy to just toss her. Since then, I've learned to do neck resets and repaired/restored several acoustic guitars and basses. Got reacquainted with some power tools that were collecting dust too. As you can tell, the folks here at the BFLG are so knowledgeable and helpful; and I've been able to overcome my "acoustic guitar complex" with their help. An iDea CC54i rebuild, an 1868 restoration, and a Fxxxxr F-330-12 repair are all projects waiting in the wings, and well...I would have never imagined attempting them had I not worked on the 1117-4!
If you go through the BFLG archives, there are some incredible project examples out there. I'm sure you're already browsing through that stuff, but I gotta warn ya, working on guitars is addictive! Good luck with the Folklore! What ever you decide to do, please share your journey with us and post some pictures. I never seem to get enough of looking at and listening to beautiful Os. They are just majestic, historic, artistic...well, you get the drift!
Edited by arumako 2016-04-05 10:25 AM
|
|
|
|
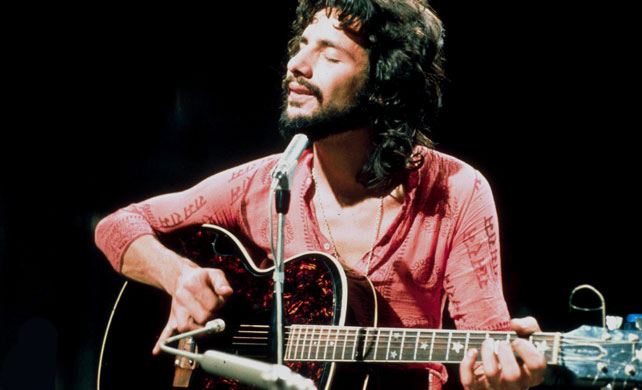 Joined: December 2015 Posts: 287
Location: Katmandu | What a beautiful, beautiful guitar, and a home-luthiery project fully realized! |
|
|