|
|
 Joined: June 2012 Posts: 2333
Location: Pueblo West, CO | A lot has been written about the revolutionary design of the Ovation guitar. But surprisingly little information is available about the Ovation guitar's most prominent feature --the bowl.
I'm starting this thread because I am facinated with the design and fabrication of molded fiberglass parts and would like to discuss/document the Ovation bowls. I'd also like to talk about the different stages of bowls and possibly obtain photos of these, especially the earliest bowls made before 1968.
I've gleaned some information from the book, 'The History of the Ovation Guitar'. ('the book') It has some detail about the manufacture of the bowls from 1974 onward. But, information about the bowls made before 1974 is a little sketchy. For example, the first bowls were hand-laid over male molds using clear plastic sheet and vacuum to produce very high-quality parts. But, after a couple of years, ways to reduce the amount of time and effort to produce these parts were sought. So, the molding process was changed to hand-laid inside a female mold.
I had thought that vacuum was applied to the inside of the female molds. But, an early Balladeer project guitar that was missing the entire top came up for sale on eBay recently. The missing top wood allowed an unfettered view of the inside of the bowl. From pics of this guitar I can see that the bowls molded in the female molds were pretty crude-looking affairs, much like any hand-laid parts. The serial number on this particular example (G 552) dates it to being manufactured between 1968 and 1970. This date range is about the same time-frame that is mentioned on page 26 of 'the book'. Of particular interest in the pics is the extra layers of fiberglass reinforcement applied to the 'tailstock' area. I'm not sure if this was done at the factory or if this was a repair done by a luthier. I would appreciate it if anyone can take a look at this area in their early Ovation to see if theirs has these extra layers of cloth.
History of the Ovation Guitar - PP. 26 1965 2-ply cloth bowl hand-laid over male mold. Covered with clear plastic, apply vacuum and scrape excess resin. High-quality, but time-consuming to produce, thus very high cost.
1968-1970 2-ply cloth bowl hand-laid in a female mold. (See: G 552 pics)
History of the Ovation Guitar - PP. 73 Until 1977 hand-laid bowls (polyester resin and woven fiberglass cloth) made in New Hartford, CT. Applause guitars used sheet molding compound (SMC) manufactured by Zehrco in OH until 1981-82. Due to strike threat at Zehrco, all bowl production (cloth & SMC) were brought to Moosup, CT facility. Cloth bowls phased out in 1981 and all guitars were fitted with SMC bowls. In eight years of production over 100,000 guitars were produced at Moosup facility. (1974 - 1982)
History of the Ovation Guitar - PP. 88 Moosup facility opened in 1974. Both the low-end Applause, high-end Adamas and some of the solid-body Ovation guitars were developed at Moosup.
History of the Ovation Guitar - PP. 92 Moosup was closed in 1982-83. Marion, NC facility opened in 1982-83. Bowls (SMC) were made in Marion and sent to New Hartford, CT for Ovation/Adamas and to Korea for Applause guitars. Standard Balladeer (SSB, CA & deep bowls) were the only model produced in significant numbers at Marion. Marion facility closed in 1985.
History of the Ovation Guitar - PP. 94 Zehrco started molding Applause bowls (SMC) in 1974. SMC bowl presses were moved to Marion in 1982. In 1984 bowl production was moved back to Zehrco in OH.
2005 Factory Tour with Rick Hall SMC is random glass fibers in a resin matrix. SMC bowls are pressed into shape in heated compression molds. Around 2001, Zehrco approached Ovation with idea of using lighter SMC. Lighter SMC contains ~35-percent microscopic glass spheres, i.e.: microballoons. (Lyrachord GS) GS in Lyrachord GS name stands for glass spheres. Lyrachord GS bowls are ~35-percent lighter than standard SMC bowls.
Timeline 1966 - 1968 Hand-laid bowls over male molds.
1968 - 1970 Hand-laid bowls inside female molds.
1974 Applause SMC bowls molded by Zehrco in OH begins.
1970 - 1977 Ovation hand-laid bowls made in New Hartford, CT.
1981 Hand-laid bowls phased out.
1982 All guitars begin using SMC bowls molded in Moosup.
1977 - 1984 SMC bowl production moved to Marion, NC.
1984 All SMC bowl production moved back to Zehrco in OH.
2001 Lyrachord GS bowl developed.
Photos: 1111 G 552 #1 1111 G 552 #2 1111 G 552 #3 1111 G 552 #4 1984 Factory Tour - SMC bowl molding
Edited by DanSavage 2013-01-05 11:44 AM
|
|
|
|
 Joined: June 2012 Posts: 2333
Location: Pueblo West, CO | I would like to add that everyone should feel free to add whatever comments/photos to this thread.
Another interesting aspect of the photos of G 552 is the relatively crude looking neck block inside the bowl.
Strangely, the 5-piece laminated neck appears to be split in the same spot as it would if it used heel-block construction techniques.
Edited by DanSavage 2013-01-05 1:54 PM
|
|
|
|
 Joined: January 2009 Posts: 1249
Location: Texas | Hey Dan Here are some pics from 485 and 1911 I could not tell any difference in the composition or cosmetic makeup of either guitar. When I pulled out my point and shoot and looked at the pictures, I thought there were prehistoric drawings on my bowl, but alas, it appears to be possibly a .20 milkshake spill from 67 Pic1 Pic2 Pic3 Pic4 Pic5 |
|
|
|
Joined: March 2002 Posts: 15677
Location: SoCal | You know, you can't play 2 old Ovations at the same time. You should send one of them (your choice) to me.... |
|
|
|
 Joined: January 2009 Posts: 1249
Location: Texas | How about you come get it. |
|
|
|
Joined: May 2008 Posts: 1559
Location: Indiana | I like this topic... thanks Dan. Even though I experienced this bowl transition real time, I admit I wasn't technically aware of what was really happening. I had an early artist, a pacemaker and a 1613 classic, in that order... through the 70's, all with glass cloth bowls. Light and thin, I would often push the deepest point of the bowl into an indentation, showing the qualities of the construction to newbies at the time. A chip in the outer resin of the classic revealed the white cloth weave beneath. When my '82 Legend arrived from the factory, the SMC bowl was noticeably different... as was my Adamas a year later. No longer able to push in on the back, seemed like solid plastic to me I remember thinking. In truth, I was so taken by the new K-bar necks, the new bowls quickly became an afterthought. I'll be interested in any insights the collective here might have. |
|
|
|
 Joined: June 2012 Posts: 2333
Location: Pueblo West, CO | Hi Jay!
Thanks for the pics. These are exactly the type of pics I was hoping to get. 
Your serial numbers tell me that both bowls were hand-laid, vacuum-bagged over the male molds. Are you able to feel any texture of the fiberglass cloth weave with your fingers on the inside of the bowls?
Interestingly, in Pic #1, the bowl almost looks like there's some print-through of the fabric weave showing in the reflection of the neck. Is this just a weird reflection or can you see the weave of the fabric? 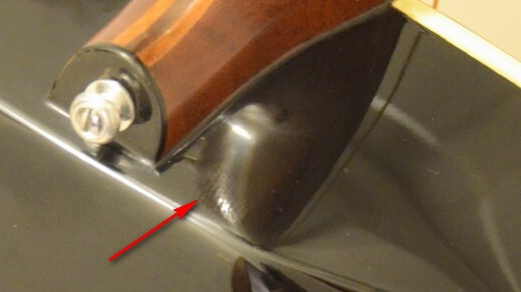
Pic #5 is also very interesting to me. I see several things.
1) It looks like the epoxy glue holding the wood block into which the strap button is screwed has let loose at some point.
It almost looks like the original 'doubler' was replaced at some point with the wood block shown in the photo. I say this because the block doesn't look like it would fit into the glue joint.
Do both guitars have this type of wood block or is one different from the other?
2) The inside of the bowl looks like it was sprayed with black paint because of the masking effect where the paint was not able to hit that allows the bare fiberglass to show through.
This is the other reason why I think this wood block was not original. It's bare wood, but missing paint below it shows the original 'doubler' was there when the inside of the bowl was sprayed.
3) What is that? It almost looks like some sort of sponge foam.
Pretty funny stuff about the vintage milkshake stain. If you're feeling really brave, you could taste it to see for sure...  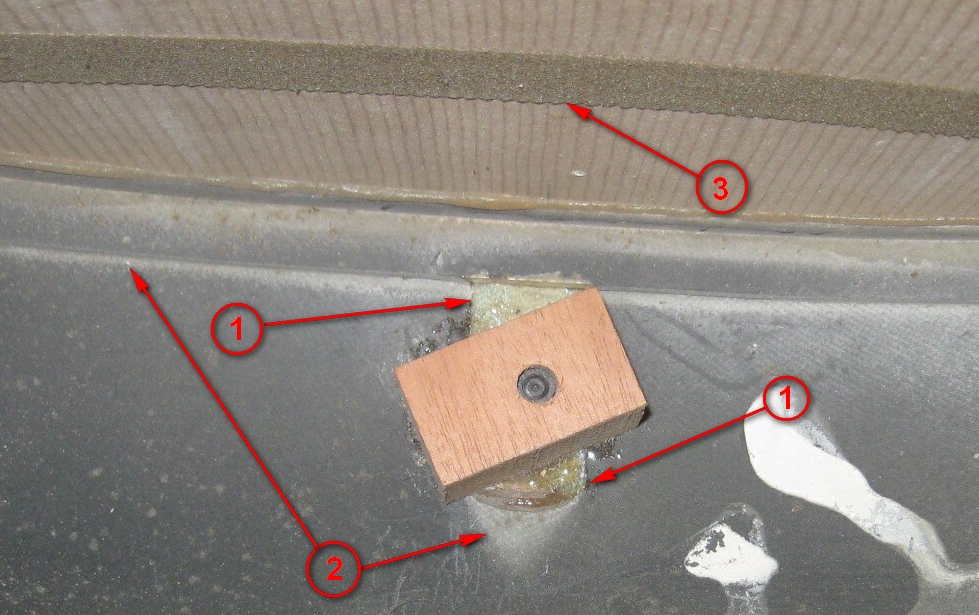
amosmoses - 2013-01-05 6:48 PM Hey Dan Here are some pics from 485 and 1911 I could not tell any difference in the composition or cosmetic makeup of either guitar. When I pulled out my point and shoot and looked at the pictures, I thought there were prehistoric drawings on my bowl, but alas, it appears to be possibly a .20 milkshake spill from 67 |
|
|
|
 Joined: June 2012 Posts: 2333
Location: Pueblo West, CO | Thanks, Jonmark.
Yep. Your description of the 'thinness' of the bowls sounds like a hand-layup to me.
If you look at PP.13 of the 2007 Ovation Factory Tour on the Ovation Tribute site, you can see several hand-laid bowls in their 'natural' state. (See: PP.13) The 'blueish' color looks to me like the primer. Where the primer has been sanded through, the natural fiberglass resin shows through as the 'greenish' color. The 'whiteish' color around the neck slot in the top of the body is where the skin of the molded fiberglass resin as been sanded through and is showing the interior of the fiberglass resin/cloth, itself. 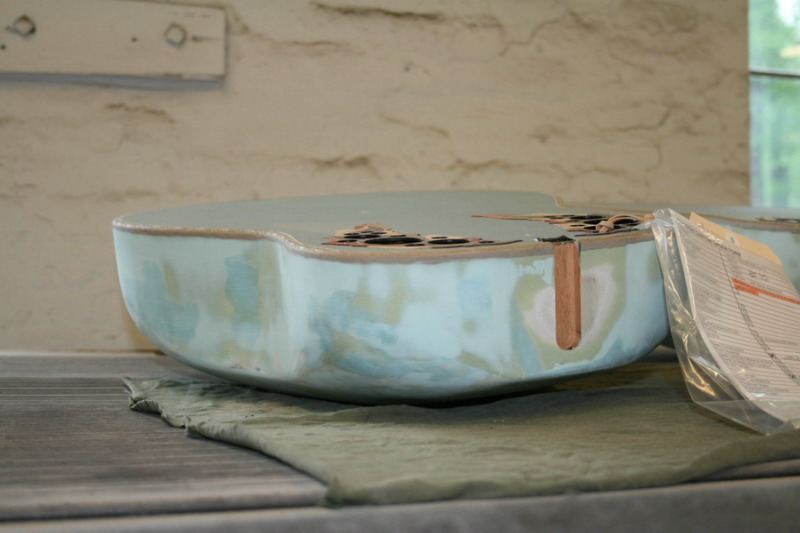
I have an `82 1655, which was the first year of the SMC bowls and it's noticably thicker and less flexible than my 2078. The later Lyrachord GS bowls also seem vibrate more than the early SMC bowl. (belly rumble) In fact, I've found that the back-door adds structural integrity. Whenever I remove it, the bowl is more flexible than when it's tightly clamped into place.
Jonmark Stone - 2013-01-05 9:29 PM
I like this topic... thanks Dan. Even though I experienced this bowl transition real time, I admit I wasn't technically aware of what was really happening. I had an early artist, a pacemaker and a 1613 classic, in that order... through the 70's, all with glass cloth bowls. Light and thin, I would often push the deepest point of the bowl into an indentation, showing the qualities of the construction to newbies at the time. A chip in the outer resin of the classic revealed the white cloth weave beneath. When my '82 Legend arrived from the factory, the SMC bowl was noticeably different... as was my Adamas a year later. No longer able to push in on the back, seemed like solid plastic to me I remember thinking. In truth, I was so taken by the new K-bar necks, the new bowls quickly became an afterthought. I'll be interested in any insights the collective here might have. |
|
|
|
 Joined: January 2009 Posts: 1249
Location: Texas | Hey Dan... I am not able to feel any cloth texture in the bowls...it is smooth to the touch. Very nice observation...I hadnt noticed that...you can see the weave, when the light hits it right...especially around the corners. P1 In regards to Pic5 1) I sent this guitar to the MS to have the bowl and soundboard polished. Kim commented to me it was the cleanest 67 that he could remember seeing. The tailpin was missing...so I imagine this is the MS repair. 2) Certainly makes sense 3) I am guessing that it is missing a brace, as you can see from the comparison pic from 495. When I feel it, it isn't foam, it feels like a very thin piece of wood. The top, below the bridge doesnt show any bellying and there are no lacquer cracks. hmmm...puzzled on what to do about this. The strip in 1911 is certainly wider than the brace in 485...and there are no glue globs. 485 1911 Closeup "you could taste it to see for sure" Sounds like one of Cheech and Chongs first routines...
Edited by jay 2013-01-06 7:06 PM
|
|
|
|
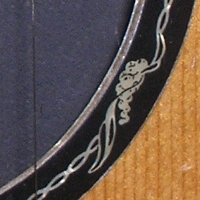 Joined: December 2009 Posts: 686
Location: Route 66, just east of the Cadillac Ranch | DanSavage - 2013-01-06 5:06 PM 3) What is that? It almost looks like some sort of sponge foam. Pretty funny stuff about the vintage milkshake stain. If you're feeling really brave, you could taste it to see for sure...  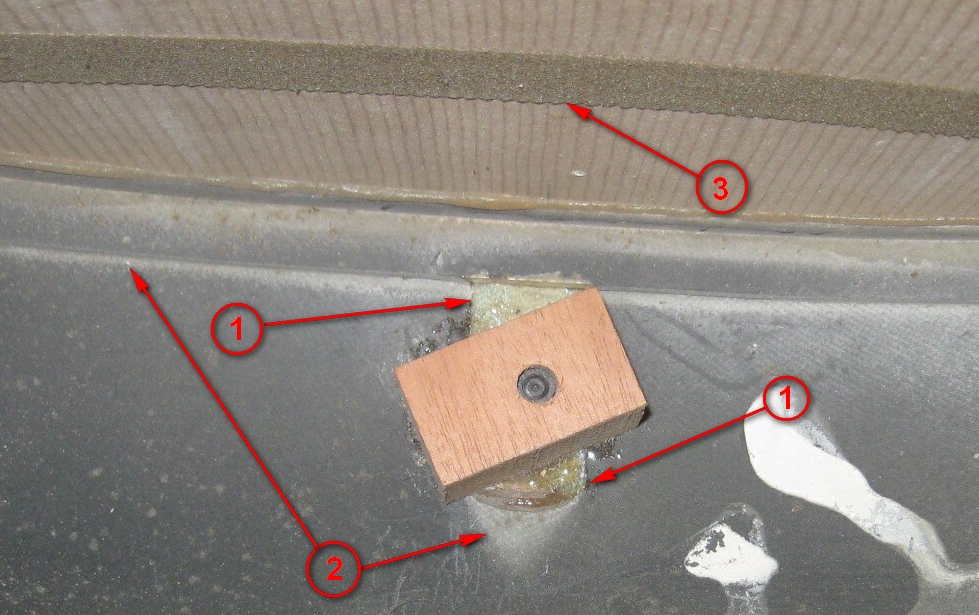
Dan, On the early Balladeers, there was a horizontal strip of fiberglass tape on the underside of the top. Somewhere there's a drawing that shows it, but I can seem to locate it tonight. Here's a photo from an an early Balladeer. I'm not sure what that strip is the picture you posted. Nick
(IMAG0237_sm.jpg)
Attachments ----------------
IMAG0237_sm.jpg (39KB - 2 downloads)
|
|
|
|
 Joined: June 2012 Posts: 2333
Location: Pueblo West, CO | Hi Jay, Print through is pretty common in the fiberglass industry and it's more of a visual problem than a structural one. It's usually caused by the resin shrinking or too much vacuum being applied to parts being vacuum bagged. It's also more of a problem with darker colors than lighter ones. It could be that during the course of its lifetime, this guitar sat in a stand for a while in a sunny spot. There are ways to minimize it, such as laying down a layer of cloth with a finer weave on the exterior layer, which is what I do. Personally, I wouldn't worry about it. 1) Aha! That makes perfect sense. 3) I looked at the original patent documents and it looks like this may just be the fiberglass reinforcement. It's interesting that 485 has a wood brace but 1911 does not. It's also interesting that 485 looks like it has a lot of excess resin on the back of the sound board while 1911 is almost perfectly clean wood in this area. With instruments this old, it's nearly impossible to determine what kind of life they've had and what's been done to them over the years. It could be that some luthier who was ignorant of the early Ovation construction added the wood brace to 485 somewhere along the line. Personally, if 1911 plays well and isn't bellying, then I wouldn't do anything. If the MS looked at it and gave it a passing grade, then I would leave well enough alone. Thanks again for the pics. Dan amosmoses - 2013-01-06 4:59 PM Hey Dan... I am not able to feel any cloth texture in the bowls...it is smooth to the touch. Very nice observation...I hadnt noticed that...you can see the weave, when the light hits it right...especially around the corners. P1 In regards to Pic5 1) I sent this guitar to the MS to have the bowl and soundboard polished. Kim commented to me it was the cleanest 67 that he could remember seeing. The tailpin was missing...so I imagine this is the MS repair. 2) Certainly makes sense 3) I am guessing that it is missing a brace, as you can see from the comparison pic from 495. When I feel it, it isn't foam, it feels like a very thin piece of wood. The top, below the bridge doesnt show any bellying and there are no lacquer cracks. hmmm...puzzled on what to do about this. The strip in 1911 is certainly wider than the brace in 485...and there are no glue globs. 485 1911 Closeup "you could taste it to see for sure" Sounds like one of Cheech and Chongs first routines... |
|
|
|
 Joined: June 2012 Posts: 2333
Location: Pueblo West, CO | Hi Nick, Thanks for the info. I did a search online and found the original patent documents/drawings that describe the reinforcement strip you mention. (See below) Dan 

nickbtx - 2013-01-06 7:00 Pm Dan, On the early Balladeers, there was a horizontal strip of fiberglass tape on the underside of the top. Somewhere there's a drawing that shows it, but I can seem to locate it tonight. Here's a photo from an an early Balladeer. I'm not sure what that strip is the picture you posted. Nick
Edited by DanSavage 2013-01-07 9:36 AM
|
|
|
|
 Joined: June 2012 Posts: 2333
Location: Pueblo West, CO | Another example of an early Ovation came up for sale on eBay. (Thanks, Jay!)
Like G 552, the serial number/date (A-913) tells me this is the second generation bowl hand-laid inside a female mold. (1968-1970)
The weave showing inside confirms it. It's interesting to see the differences in the lay-up technique between this example and G 552. Lay-ups inside female molds requires a more careful technique than over male molds to achieve consistent part thickness. This is probably part of the reason why these were considered inferior to the earlier generation of bowls hand-laid and vacuum-bagged over male molds.
1111 A-913 #1 1111 A-913 #2 1111 A-913 #3
|
|
|
|
 Joined: June 2012 Posts: 2333
Location: Pueblo West, CO | TJR recently sent me some pics I thought were very interesting, so I thought I'd share.
The first two pics show a 1st Generation hand-laid bowl.
As someone who's done this type of molding there were several details that jumped out at me. If you read 'The Book', the process for making laying up these bowls is described on PP. 26. While the 2x2 twill weave cloth can easily form over this kind of shape, the clear plastic sheet is used for for molding over a compound curved back cannot fully conform to the shape. It folds over and wrinkles when the vacuum is applied. This produces the characteristic ridges and valleys we can see in the photos along the sides and radius to the back. Once the resin has cured, these need to be sanded smooth, which we can see in this bowl. TJR relates that this bowl is noticably smaller than the modern bowl he sent me and would fit inside the modern bowl with room to spare. 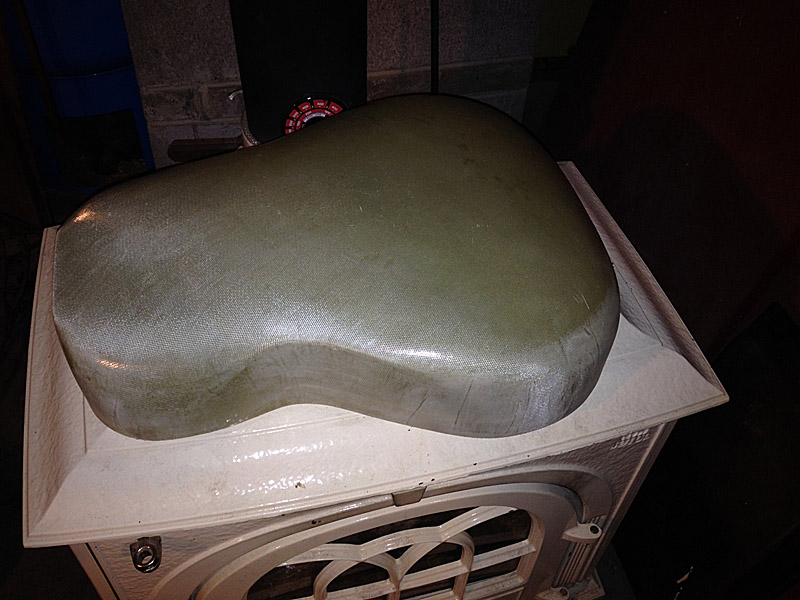
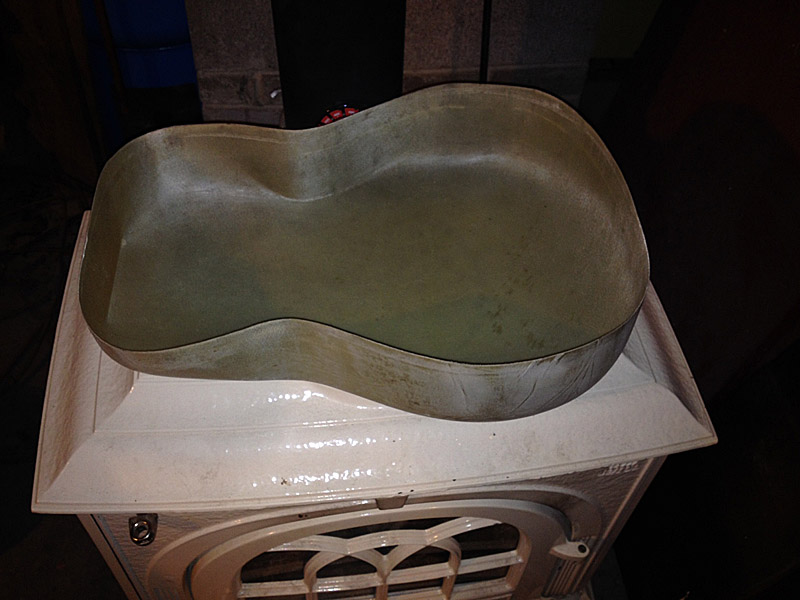
In this next photo we see a laminated wooden plug. This is from a very early development period. We can tell this because of the slab sides and lack of radius between the back and the sides along the upper and lower bouts. It also has more of a dreadnaught shape rather than the pinched-waist OM-style used by virtually all Ovation guitars. I suspect this was from a mid-step engineering test between the flat-backed fiberglass design and the fully-radiused design seen in the pics above. This type of construction is fairly normal for mold-making. Being solid wood, I'll bet it weighs a ton. 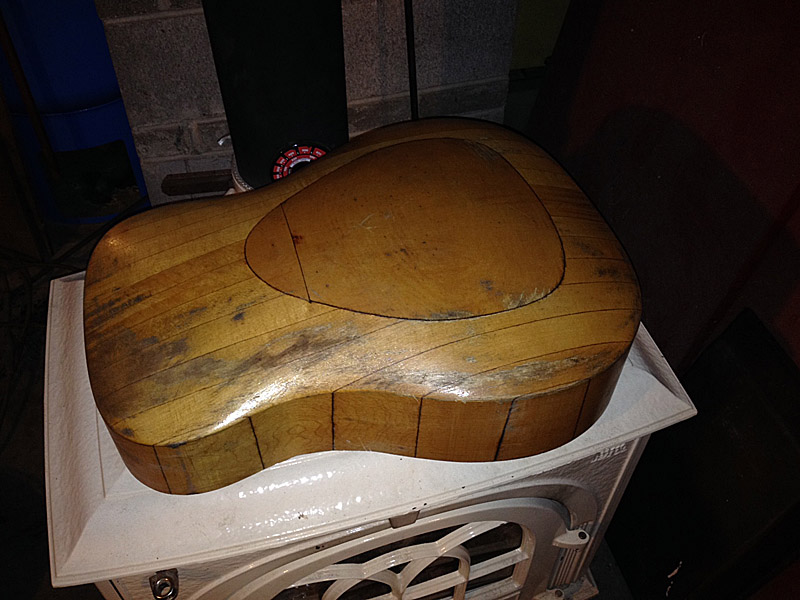
Edited by DanSavage 2014-05-14 8:56 PM
|
|
|
|
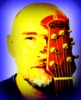 Joined: August 2007 Posts: 1008
Location: Tuscany, Italy | Thank you Dan.... |
|
|
|
 Joined: June 2012 Posts: 2333
Location: Pueblo West, CO | You're welcome. |
|
|
|
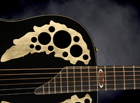 Joined: October 2012 Posts: 1089
Location: Yokohama, Japan | DanSavage - 2013-01-05 3:48 AM
I would like to add that everyone should feel free to add whatever comments/photos to this thread.
This is really interesting stuff... thanks for the in-depth history lesson. I never realized Lyrachord came so late in Ovation lore.
Edited by arumako 2014-05-16 5:34 AM
|
|
|
|
 Joined: June 2012 Posts: 2333
Location: Pueblo West, CO | You're welcome. I'm glad you're enjoying it. I've got some really interesting pics coming up.
Keep in mind that the whole 'Lyrachord' moniker is strictly a term Ovation marketing applied to the composite bowl. There were several processes used throughout the years to mold the bowl. Every single one was called 'Lyrachord'.
As can be seen, there's really nothing special about the process or the components.
In the early days, it was off the shelf fiberglass borrowed from Charlie's helicopter business. The first bowls were molded vacuum-bagged over male molds, but that process is very labor-intensive. To save time, they went to female molds, which didn't require as much labor. Finally, they wen to SMC.
SMC is an industrial composite used to mold Corvette bodies and other things. It allowed Ovation to produce bowls more quickly, which reduced the cost of each bowl even more and thus, increased the profit margin through reduced labor cost.
Finally, they went back to hand-laid bowls in female molds, again, but only for Adamas and custom guitars. To get the quality of the 1st gen bowls, they utilized vacuum and a membrane inside and autoclave. This produces bowls with the surface perfection and reduced production costs of SMC, but the thinness and responsiveness of the 1st gen cloth bowls. |
|
|
|
Joined: March 2007 Posts: 698
Location: Cork, Ireland | Jonmark Stone - 2013-01-06 5:29 AM
"...Light and thin, I would often ...".
Are you still light and thin??
Interestign topic anyway! |
|
|
|
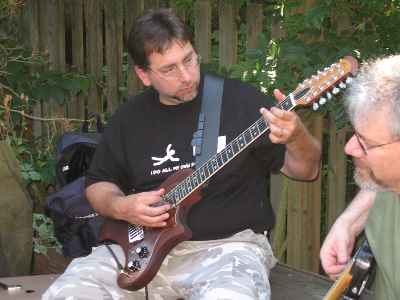 Joined: December 2003 Posts: 13996
Location: Upper Left USA | I love when people take things apart and put them back right in front of you!
Good stuff! |
|
|
|
Joined: March 2007 Posts: 698
Location: Cork, Ireland | Also interesting how the patent shown above gives a detailed description of a truss rod. Apparently that was patented in 1923: http://worldwide.espacenet.com/publicationDetails/biblio?CC=US&NR=1... |
|
|
|
 Joined: June 2012 Posts: 2333
Location: Pueblo West, CO | MWoody - 2014-05-16 7:57 AM
I love when people take things apart and put them back right in front of you!
Good stuff!
You'll really enjoy the pics I just got.
I'll post them tonight along with a description of what you're seeing. |
|
|
|
 Joined: June 2012 Posts: 2333
Location: Pueblo West, CO | sycamore - 2014-05-16 8:00 AM
Also interesting how the patent shown above gives a detailed description of a truss rod. Apparently that was patented in 1923: http://worldwide.espacenet.com/publicationDetails/biblio?CC=US&NR=1...
I could see the document earlier, but I wanted to thank you for posting the link. The curvature of the truss rod almost makes me think that tightening it would cause the neck to bow upward. |
|
|
|
 Joined: June 2012 Posts: 2333
Location: Pueblo West, CO | Here's a couple of pics of the newest generation cloth bowl. This is the same bowl I used to mold the patch on my 1619-4 Repair thread in the BFLG forum. 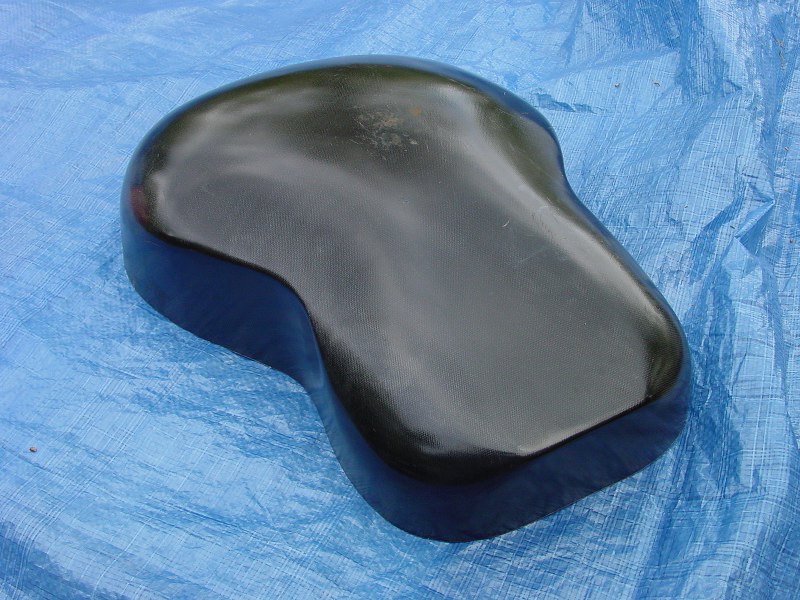
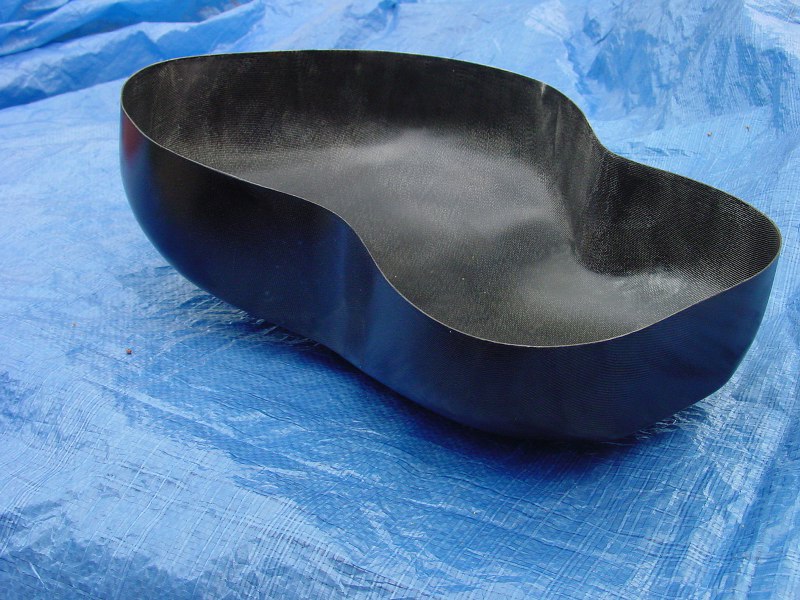
Here's a couple more pics of the 1st gen cloth bowl. 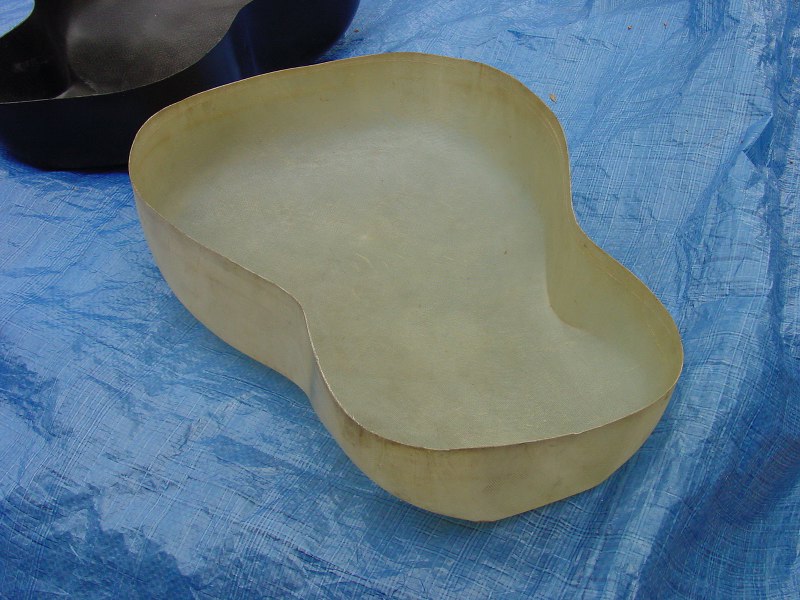
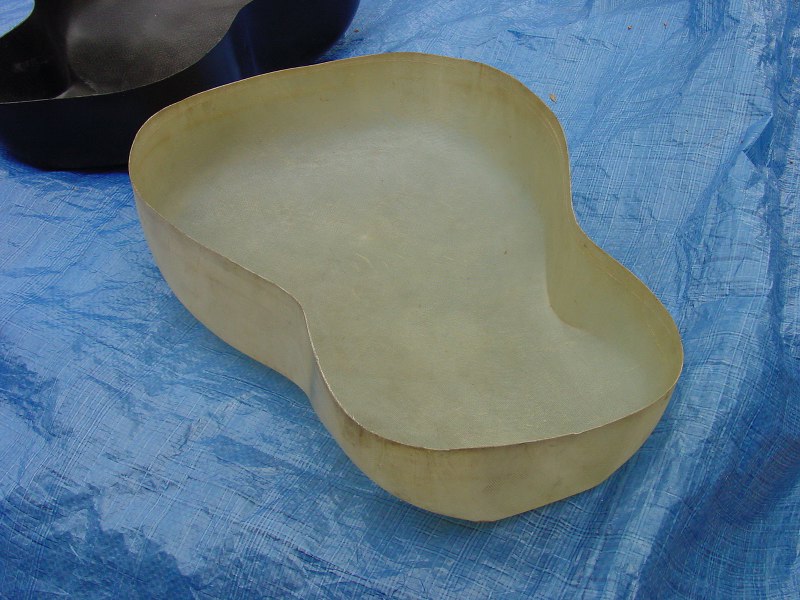
Here's a pic of the 1st gen bowl inside the newest gen cloth bowl. As you can see, they've gotten larger over time. This is not caused by shrinkage. Usually when epoxy resin shrinks, it just makes the parts thinner, not smaller. 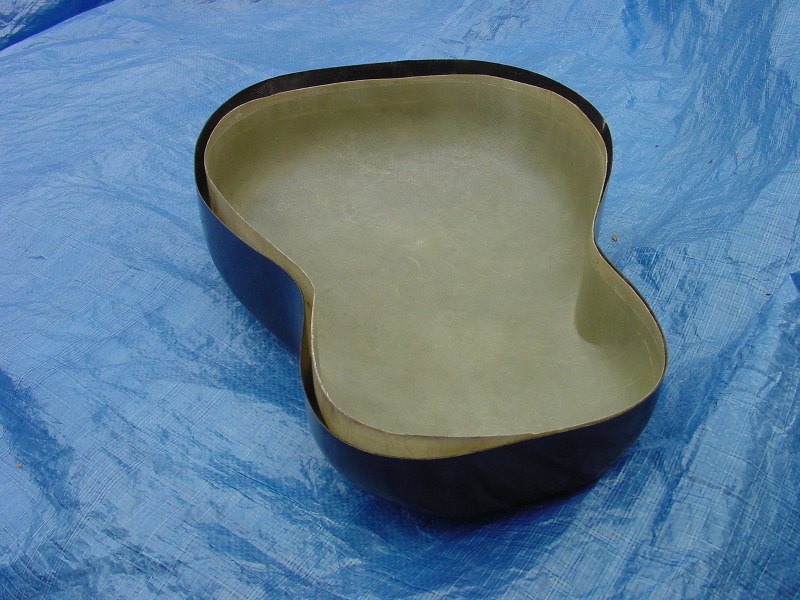
Here's a pic of the 1st gen wooden mold and and a cloth bowl. What you're seeing here is worth noting.
First, the mold is a lot deeper than the bowl. This is because when when vacuum bag molding a part, you have to allow space for the plastic bag to fold over at the base of the mold. This is the same principle used for vacuum molding plastic parts. You need a little bit over overhang which must be trimmed from the final part.
In contrast, a female mold can be made to net depth because the part can be trimmed to the top edge of the mold.
The bowl has had the neck and heel blocks glued into place and the upper part where the kerfing would be glued has been masked, then the whole interior of the bowl has been sprayed black. The sharp angle of the neck block shows us this is a very early bowl, probably 1965-1966. 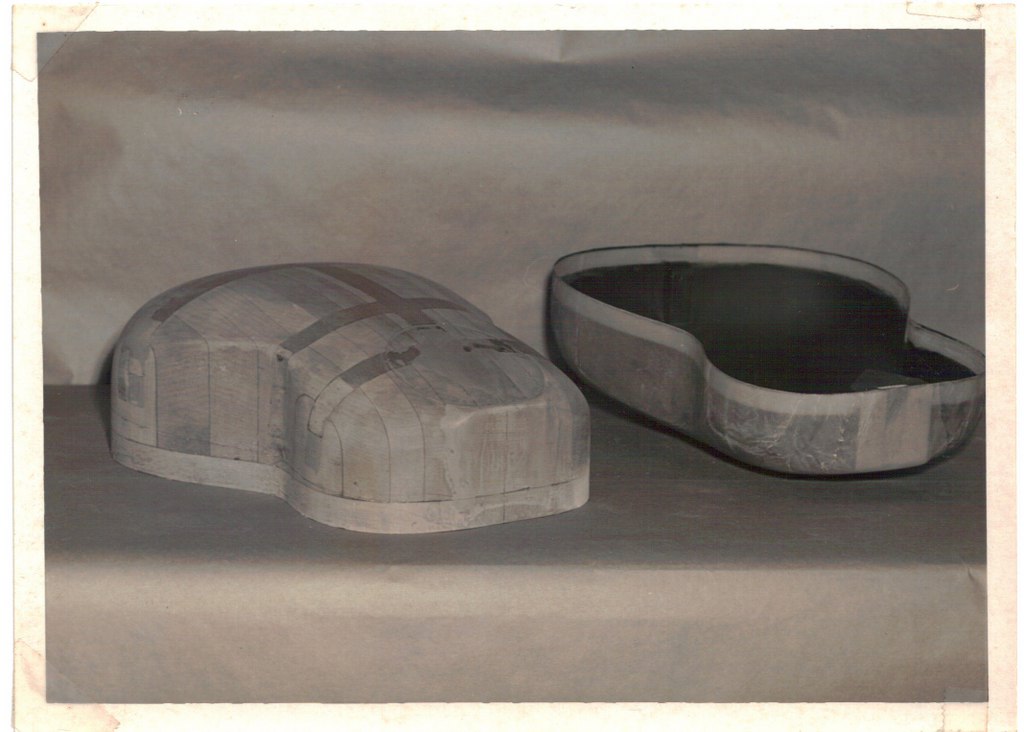
In contrast, here is a pic of the two-part mold used to produce the SMC bowls. Welcome to the industrial age!
As I noted above, the SMC bowls used fiberglass prepreg molded over steel molds heated to 300 degrees. Finished parts came out of the mold in minutes, instead of hours. 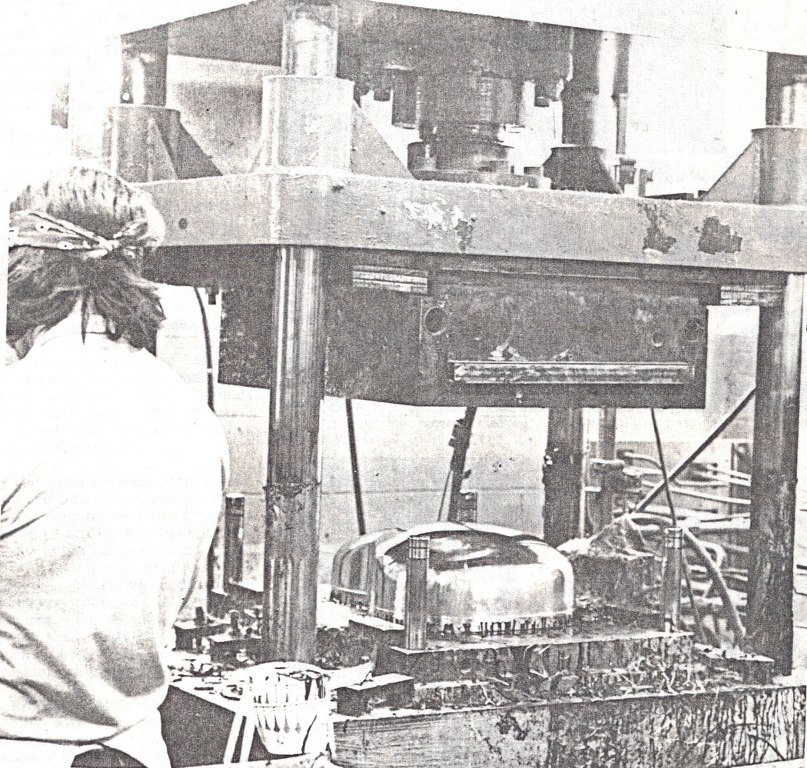
Speaking of tops, here's some pics of the 1st gen top. These used very simple X-bracing. Note the lack of finger braces and tone bars commonly seen on X-braced guitars.
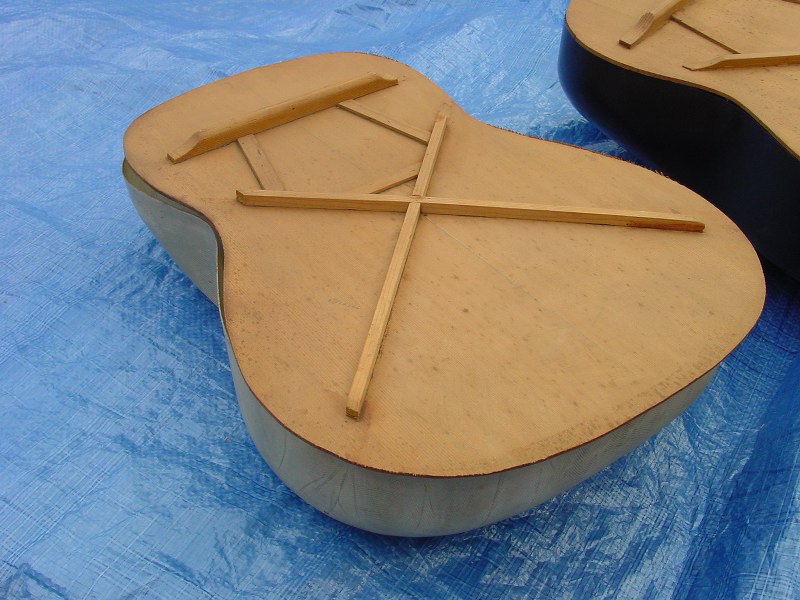
Here's another 1st gen top. This one is a 3-piece spruce top, circa 1966. 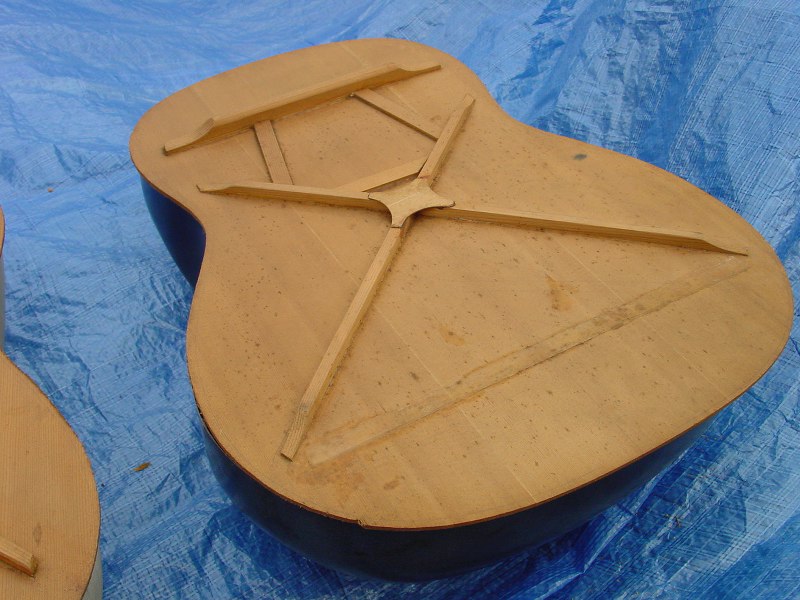
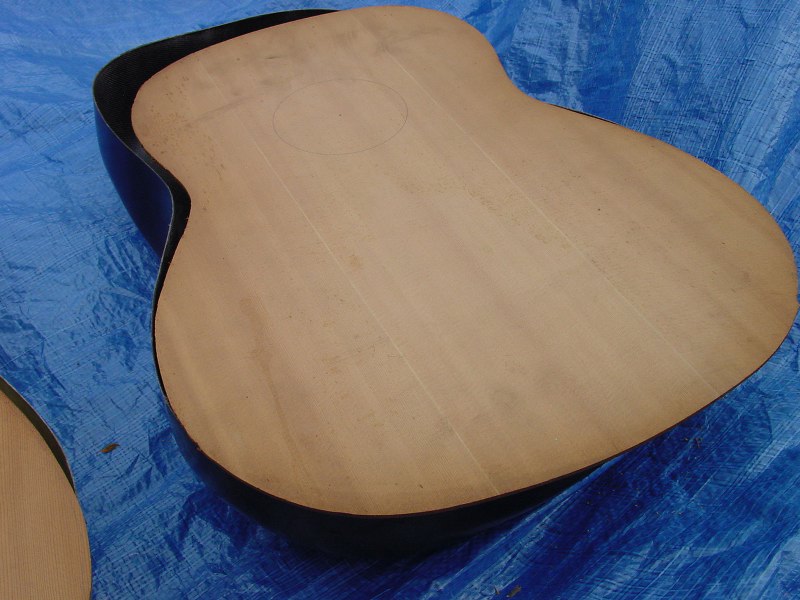
How do we know it's from 1966? Why, because it's been dated! 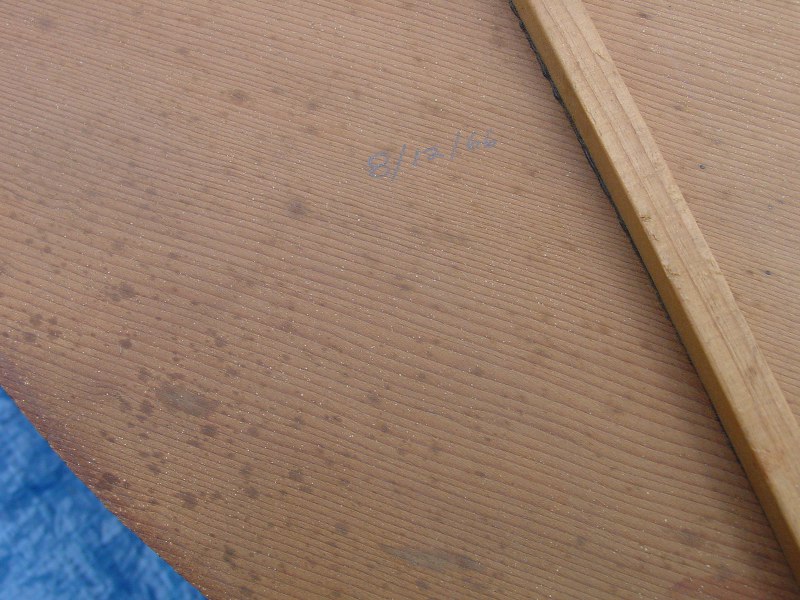
Although the X braces and popcicle braces have been scalloped, and the center joint reinforced (with birch plywood, no less!) the glue joints between the X braces and the soundhole strips are pretty sloppy. Also seen is the fiberglass reinforcement strip across the lower bout mentioned in the patent documents above. 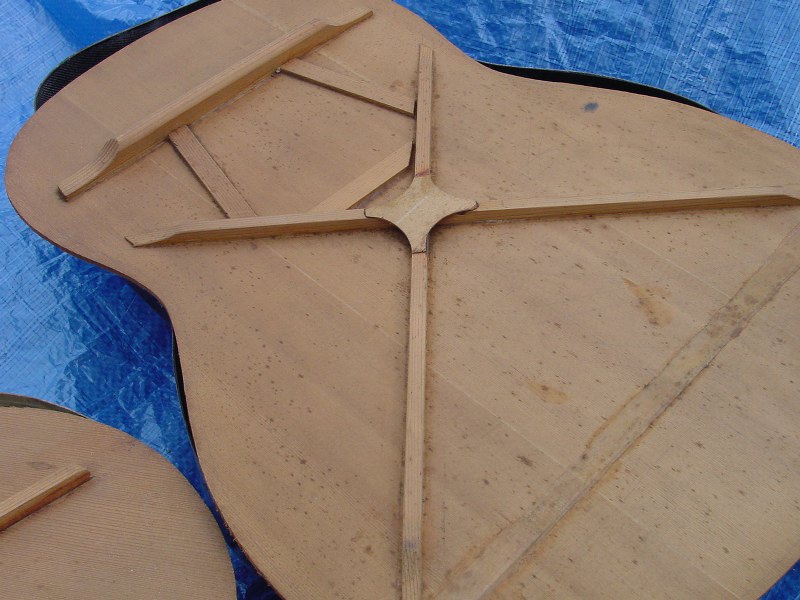
Edited by DanSavage 2014-05-16 8:29 PM
|
|
|
|
 Joined: January 2009 Posts: 1249
Location: Texas | Dan...just curious...where did you get the tops?
And do we have any idea how many of those wooden molds they used in production in the 60's...and you wonder what happened to all of them...
|
|
|
|
 Joined: June 2012 Posts: 2333
Location: Pueblo West, CO | Good question!
These tops aren't mine. TJR sent me these pics, so I imagine they belong to him.
I have no idea how many production molds survived. Generally speaking, the fiberglass molding process follows these steps:
1) Master plug --created using wood or some other medium. (I've always used wood, foam, etc.)
2) Master mold --Molded off the master plug using fiberglass.
3) Production plug --Molded off the master mold using fiberglass, and a duplicate of the master plug.
4) Production mold --Molded off the production plug using fiberglass and a duplicate of the master mold.
This process allows the manufacturer to use the production plug to produce an unlimited number of production molds. When the production molds finally wear out, the production plug is used to produce more production molds. When the production plug finally wears out, the Master mold is used to produce another (set) of production plugs, which are, in turn, used to produce more production molds.
Now, it's entirely possible what we're seeing here in this pic is not a production mold, but the master plug, the wooden plug being more 'dramatic' in the photos. |
|
|
|
 Joined: October 2005 Posts: 4071
Location: Utah | The bracing on my 1976 Patriot (center hole A braced) is quite a bit daintier than the bracing in those pictures. Really the braces are surprisingly thin and light. |
|
|
|
 Joined: June 2012 Posts: 2333
Location: Pueblo West, CO | I just finished pulling the top off my 1619 and the A brace wood is ~1/8" thick, or about 1/2 that of the X braces. |
|
|
|
 Joined: June 2012 Posts: 2333
Location: Pueblo West, CO | Here's what's left of the A braces from my 1619. 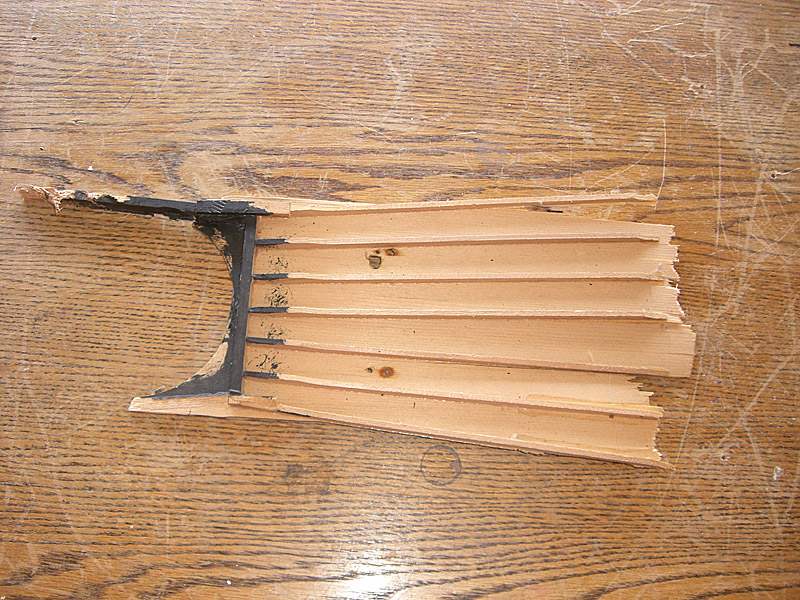
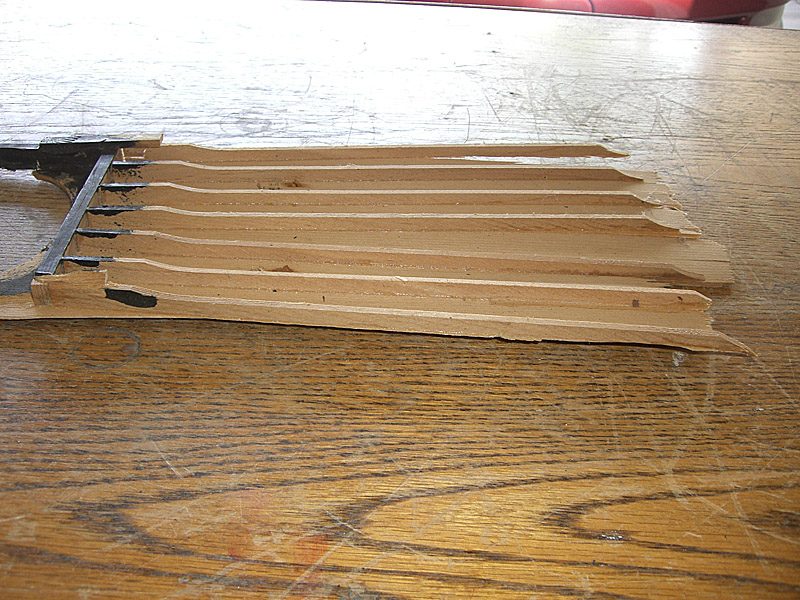
Edited by DanSavage 2014-05-17 6:51 PM
|
|
|
|
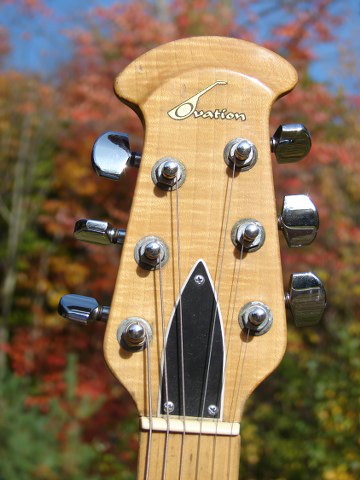 Joined: July 2002 Posts: 288
Location: Maine | Nice documentary you have going on here. Can't wait to see the rest of the rebuild.
|
|
|
|
Joined: September 2009 Posts: 180
Location: michigan | Great stuff. I just picked up a 40th anniversary balladeer shiny bowl (2007 I believe). I think they only made 50 (mine is serial number 3)
What type of process did they use on these 40th anniversary reissues. I also have the 40th anniversary Glen Campbell which is a hand laid fiberglass (but not shiny) |
|
|
|
Joined: November 2011 Posts: 741
Location: Fort Worth, TX | rhoadsscholar - 2014-05-17 10:10 PM
Great stuff. I just picked up a 40th anniversary balladeer shiny bowl (2007 I believe). I think they only made 50 (mine is serial number 3)
What type of process did they use on these 40th anniversary reissues. I also have the 40th anniversary Glen Campbell which is a hand laid fiberglass (but not shiny)
Wow, I was the original purchaser of serial number three! If you don't mind me asking, how did it come into your hands after going off to Colorado following a trade for it? The only thing about it that bugged me was the ripple lines you could see in the top that revealed where the bracing was.I guess this happened during certain humidity conditions but I was always afraid the top was going to crack because of it. The top on it must have been really thin but it sure was a nice responsive guitar. |
|
|
|
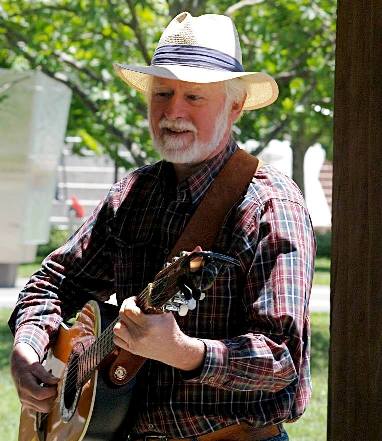 Joined: September 2012 Posts: 813
Location: Thredbo, NSW, Australia | DanSavage - 2014-05-18 11:50 AM
Here's what's left of the A braces from my 1619.>
I'm hoping the backdrop for the bracing is an oak desk or table, and not an extended soundboard! (I was wondering how the pick scratches came to be on the inside.)
In any case, thank you so much Dan for your story here and in the 1619-4 rebuild. I'm following them both with interest.
|
|
|
|
 Joined: October 2005 Posts: 4071
Location: Utah | DaveKell - 2014-05-18 2:33 AM
The only thing about it that bugged me was the ripple lines you could see in the top that revealed where the bracing was.I guess this happened during certain humidity conditions but I was always afraid the top was going to crack because of it. The top on it must have been really thin but it sure was a nice responsive guitar.
My 1976 Patriot shows the same bracing lines due to the thinness of the top and possibly the thinness of the braces. It is the very best sounding guitar I've ever played, O or A or otherwise. Black gloss O's show these lines more than other finishes. There don't seem to be any structural concerns. My guitar is 37 years old and is going strong. |
|
|
|
 Joined: June 2012 Posts: 2333
Location: Pueblo West, CO | BanjoJ - 2014-05-18 5:03 AM
I'm hoping the backdrop for the bracing is an oak desk or table, and not an extended soundboard! (I was wondering how the pick scratches came to be on the inside.)
In any case, thank you so much Dan for your story here and in the 1619-4 rebuild. I'm following them both with interest.
Ha ha! It used to be an oak computer desk. I wanted to get rid of it, but SWMBO insisted on keeping it. I shrugged and said okay and turned into a workbench in my shop. I have no reservations about drilling holes in it, driving screws into it, spilling paint on it, scratching it, etc. While it was fine furniture at one time, now it's a workbench and is treated as such. (much to her consternation)
You're very welcome. I'm glad you're enjoying it.
Edited by DanSavage 2014-05-18 4:28 PM
|
|
|
|
 Joined: June 2012 Posts: 2333
Location: Pueblo West, CO | trickard - 2014-05-17 7:56 PM
Nice documentary you have going on here. Can't wait to see the rest of the rebuild.
Thanks, TJ. I think you'll like the next update to my 1619-4 thread. |
|
|
|
 Joined: June 2012 Posts: 2333
Location: Pueblo West, CO | rhoadsscholar - 2014-05-17 8:10 PM What type of process did they use on these 40th anniversary reissues. I also have the 40th anniversary Glen Campbell which is a hand laid fiberglass (but not shiny) The 1st gen bowls were vacuum bagged. While this produces very high quality parts, it's pretty labor intensive. Here's a schematic drawing showing the laters used when vacuum bag molding. 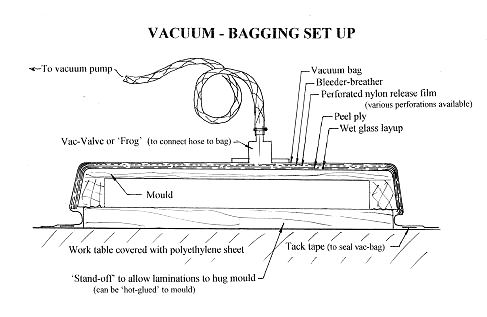
And, here's a part being molded. Even though this is a slightly concave part, the process is the same for a male part like the 1st gen bowls. Notice the folds in the plastic vacuum bag. These can also be seen in the pics of the 1st gen bowl I posted and this is how they get there. 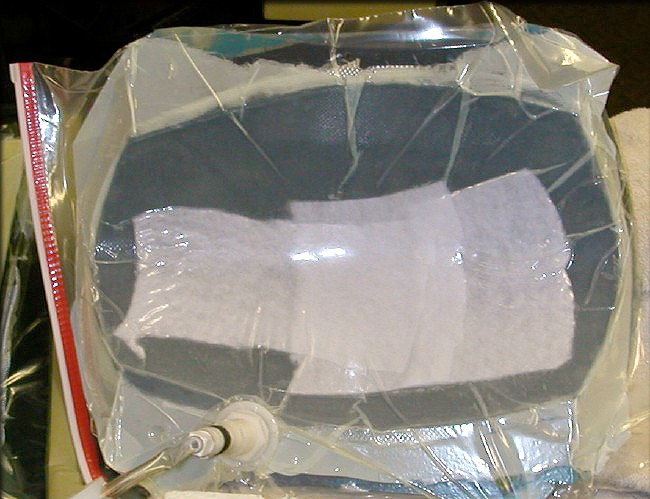
The later hand-laid bowls, like the one seen in my 1619-4 thread, are made in female molds.
But, instead of squeegeeing the excess resin by hand, and then letting them cure naturally, they put them into an autoclave which applies vacuum, pressure and heat. Here's a schematic drawing of how the bowls laid up. This drawing shows prepreg, but the bowl I've got was done with plain old resin and 2x2 twill cloth. Generally speaking, prepreg uses fiberglass roving, not woven cloth. 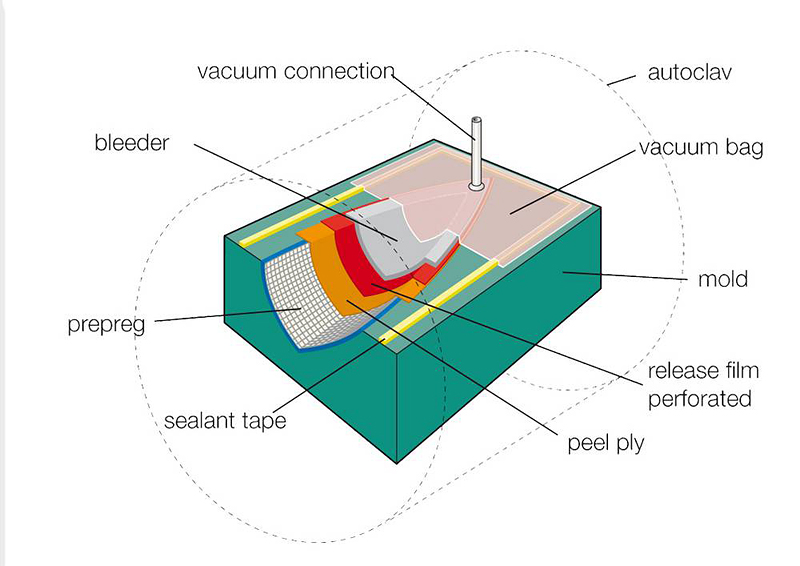
And, here's a carbon fiber bowl being molded in a female mold. This part is placed into the autoclave. The pressure squeezes out the excess resin and the heat makes the part cure faster. Making parts using this method is less labor intensive and the finished parts can be produced more quickly. Not as quick as SMC prepreg, but a lot quicker than letting the resin cure naturally. So, you get high quality parts more quickly. 
Any discussion about vacuum molding composites wouldn't be complete without also mentioning resin infusion. Instead of laying up cloth and wetting it out with resin, then vacuum bagging it, dry cloth is laid up, vacuum is applied and the resin is sucked through the cloth. Resin infusion is slightly more wasteful of resin, but produces the highest quality part with the highest cloth to resin ratio. To my knowledge, resin infusion is not used with autoclave molding, nor did Ovation use it in their molding process. 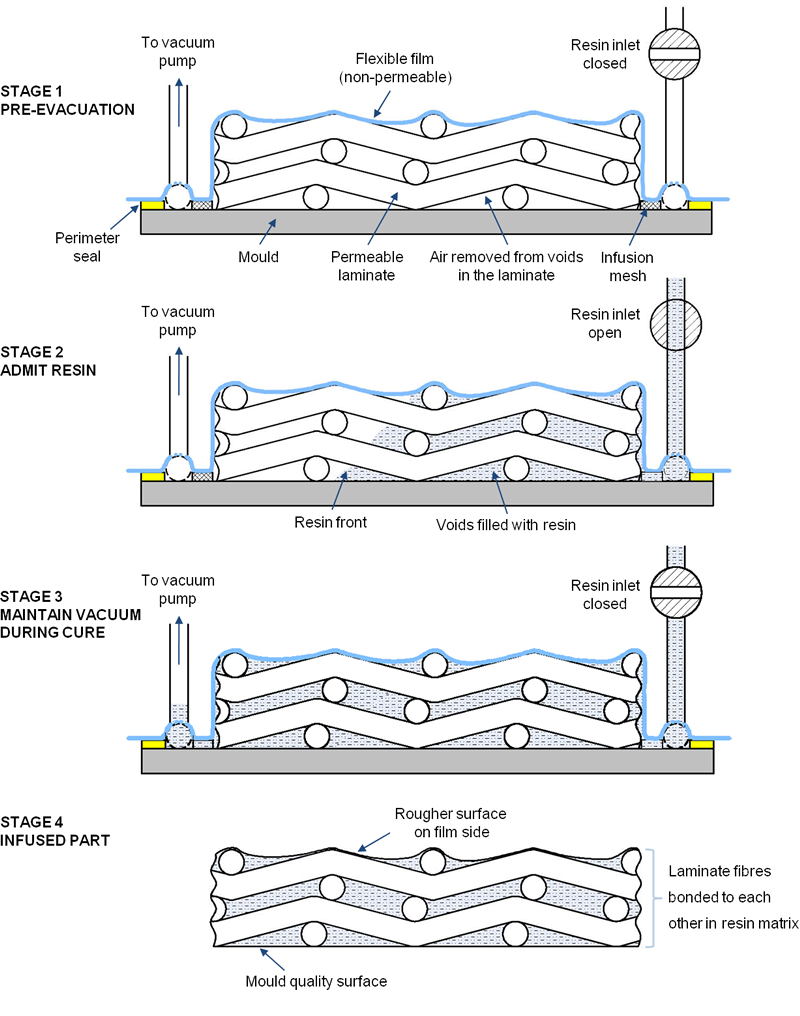
Edited by DanSavage 2014-05-18 5:05 PM
|
|
|
|
 Joined: January 2009 Posts: 1249
Location: Texas | Dan...this is almost as good as 24. Ok...but back to scholar's question (i think)...Do you think that they made the 40th RI shinys the old fashion way? |
|
|
|
 Joined: June 2012 Posts: 2333
Location: Pueblo West, CO | Jay,
I haven't seen a 40th in person, so I can't say for sure how the bowls are made.
Given that the original shinys were laid up over a male mold which required sanding to smooth out the wrinkles and folds, then I would say that they were weave-filled, primed, painted and polished.
My modern, autoclave cloth bowl would not be able to be sanded and polished without cutting into the cloth. So, to make a modern cloth bowl into a shiny bowl would also required weave-fill, priming, painting and polishing.
Was that non-committal enough?  |
|
|
|
 Joined: January 2009 Posts: 1249
Location: Texas | Dan...I just enjoy the dialog, regardless of the level of commitment. Maybe someone here can pop a few pictures of their 40th bowl, inside and out for your consideration. I bought one with quite a bit of damage to the bowl...Scratches from a belt and what looked like to be a chemical melt from epoxy or something. I sent it to the MS and bowl came back looking brand new. As badly melted as it was, I thought it would have to be replaced. Nope and for some ridiciously small fee. There is no doubt in my mind, we are going to miss those guys tremendously. |
|
|
|
 Joined: June 2012 Posts: 2333
Location: Pueblo West, CO | Me, too. I was just kidding around.
Yes, I agree. From what I understand, finding a luthier who works on Ovation guitars isn't easy. With the factory closing down, it's a serious loss of resources. |
|
|
|
Joined: December 2003 Posts: 852
Location: Canada | I think that with the re-opening of the factory and announcement of the 50th anniversary models it's timely to bring this thread back so it hopefully can be updated. I am getting the impression that all the 50th anniversary models (and it seems ALL "current" Adamas models if there are any) are spec'd with hand laid bowls. I am wondering what process would apply to this generation of bowls and who actually makes them, as I can imagine that the 7 production workers will be quite busy and bowl making could be something to be contracted out. |
|
|
|
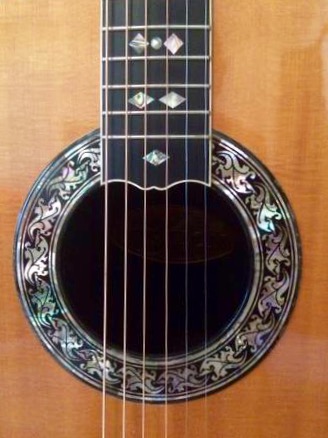 Joined: December 2014 Posts: 1713
Location: Frozen Tundra of Minnesota | Thank You for re-opening this thread!
As per his usual, Dan's Teaching Method is Exceptional! I love learning all of this, and have just learned a great deal! Thank You Dan!!
It will be exciting and interesting to see what the new re-birth brings us in new technology, and what they decide to use, and why, with the New Ovations/Adamas, and how it compares and measures up to the past procedures. I look forward to learning much more!  |
|
|
|
 Joined: June 2012 Posts: 2333
Location: Pueblo West, CO | d'ovation - 2015-11-11 2:22 PM
I think that with the re-opening of the factory and announcement of the 50th anniversary models it's timely to bring this thread back so it hopefully can be updated. I am getting the impression that all the 50th anniversary models (and it seems ALL "current" Adamas models if there are any) are spec'd with hand laid bowls. I am wondering what process would apply to this generation of bowls and who actually makes them, as I can imagine that the 7 production workers will be quite busy and bowl making could be something to be contracted out.
They're probably made using the same process I described at the top of the page, namely vacuum-bagged inside a female mold, or at least that's what the modern cloth bowl I've got looks like. It's a lot more refined than the 1st gen hand-laid, and vacuum-bagged bowl that was on #485.
Even so, with modern materials such as teflon mold release, one worker could lay up a dozen or so bowls per day. I know I could. The only real limit is the number of production-ready molds available.
Molding a one-piece part, like the bowl, is pretty straightforward. What becomes time-consuming is when you have to seam two or more molds together to make a single part, like what I had to do when I was making the inlet ducts or nose cones for the model airplane kits I used to sell.
Farming the job to an outside service only makes sense when you've got enough parts in the pipeline to offset the cost of paying someone else to do the work. |
|
|
|
Joined: December 2001 Posts: 7236
Location: The Great Pacific Northwest | Comparing bowls or making statements about "deep is louder" and such must be put into context as well. The contour bowl is a different shape (yeah duh) but not only that, it is my understanding that the new bowls have different finish coats (e.g. paint) than the originals. Over time, different paints and epoxies were used throughout the process. All of these other factors affect the final tone significantly. So comparing a new hand laid bowl to a 80's or 90's or even early 2000's era bowl fair. It's even possible that a new bowl with a new thinner, lighter finish might have more resonance than an older bowl with a thicker finish of different ingredients.
One of the issues with the Q was that because it was so resonant, the slightest coating dampened the tone more than was acceptable. There are also exceptions to the rules like a 12-String Shallow that Al was playing in my studio that I didn't realize was a a shallow bowl cause the thing sounded so big. Then there's Stonge's "unfinished" parts-o-damas that just booms. Why are the original SlotHeads soooo much louder... is it just time to break in....
Bottom line... I think we're just going to have to play the new guitars. My main reason for not jumping on the deep vs mid vs shallow opinion wagon is that I have had the opportunity to play and/or hear some of the rule breakers and the differences were not subtle at all.
I also think the contour bowls are a stroke of genius. There is even a theory that while the depth is only slightly less than a deep bowl, the shape of the inside of the bowl actually causes the same if not more resonance on the frequencies that matter due to the way the waves hit it.
Again... we're just going to have to wait and see. |
|
|
|
Joined: December 2003 Posts: 852
Location: Canada | Mr. Ovation - 2015-11-12 2:49 PM So comparing a new hand laid bowl to a 80's or 90's or even early 2000's era bowl fair. It's even possible that a new bowl with a new thinner, lighter finish might have more resonance than an older bowl with a thicker finish of different ingredients. One of the issues with the Q was that because it was so resonant, the slightest coating dampened the tone more than was acceptable. Oh boy now this goes into the territory like at AGF where they like to discuss the effects of various body woods on tone ... Why are the original SlotHeads soooo much louder... is it just time to break in.... . So I am curious, as the late 70s seemed to have been a transitional time from handlaid to composite, what kind of bowls were used on the production Adamas 1687s of that time? And was that reproduced for the 30th Anniversary RIs?
Edited by d'ovation 2015-11-12 4:11 PM
|
|
|
|
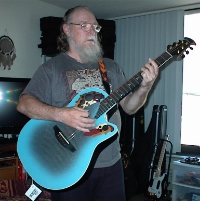 Joined: September 2006 Posts: 10777
Location: Keepin' It Weird in Portland, OR | BTW-- My 1881 SSB Adamas is LOUD.
Just sayin'
|
|
|
|
 Joined: June 2012 Posts: 2333
Location: Pueblo West, CO | Mr. Ovation - 2015-11-12 1:49 PM
Comparing bowls or making statements about "deep is louder" and such must be put into context as well. The contour bowl is a different shape (yeah duh) but not only that, it is my understanding that the new bowls have different finish coats (e.g. paint) than the originals. Over time, different paints and epoxies were used throughout the process. All of these other factors affect the final tone significantly. So comparing a new hand laid bowl to a 80's or 90's or even early 2000's era bowl fair. It's even possible that a new bowl with a new thinner, lighter finish might have more resonance than an older bowl with a thicker finish of different ingredients.
Absolutely correct. When talking about composites and finish, context is everything.
From a technical standpoint the formulation of epoxy can make a big difference in the final product. Marine epoxy, such as West Systems is very different from aerospace-grade epoxy, like MGS. Whether the epoxy is post-cured or not also makes a difference in the final product.
Modelers are interested in this kind of stuff, so a modeler did a few tests comparing some popular aerospace-grade epoxies. As with musical instruments, molded airplane parts work best when made with stiffer epoxies. If you're interested in really geeking out on epoxies, see: Epoxy Test - USC vs. MAS vs. RR vs. MGS FWIW, I used MGS epoxy for all my molded parts.Generally speaking I would expect stiffer epoxy to make better musical instruments because it would transmit vibration better than softer epoxies which would tend to absorb (read: dampen) the vibrations. As I mentioned earlier, excess resin only adds weight, not strength. Excess epoxy would also dampen vibrations. Vacuum-bagged parts are superior because it squeezes out the excess resin. 'The Book' states, the 1st gen bowls were considered to be better than the 2nd gen bowls. This can be directly attributed to the the difference in how the two generation of bowls were manufactured.
Similarly, the finish, any finish, applied, dampens vibrations. The best is no finish. Next, is french polish, followed by varnish, then nitro, polyurethane, and lastly polyester. WRT the contour bowls, my brother stayed with me last year and we had a chance to play together, he on my 2078TX-5 and me on my Book Elite. One thing that struck me while he was playing was how loud the 2078 was. I kept thinking to myself, 'Dang! Take it easy. You're drowning me out' It wasn't until later that I realized that it wasn't his playing, but the guitar itself that was loud. |
|
|
|
 Joined: December 2008 Posts: 1455
Location: Texas | This thread hasn't been active for a while, but I suspect it gets read quite a bit (and it's still very informative.) What brought me back to it was;
I was doing a little work on my 1979 Pacemaker (1115) and remembered that, back when I first got it (maybe 8 years ago?) and peeked inside, I noticed some odd-looking tan cloth/material (or something) in the "tailstock" area. (It appears to be a cloth bowl, weave patterns are visible inside, and that would fit with Dan's timeline.) I never figured out what it was, and I love the guitar, so I basically forgot about it until I looked inside it today with a flashlight. Out of curiosity, I checked the OFC and reread this entire thread. Only when I looked at those photos Dan originally linked in his first post did I realize that the inside of my Pacemaker looked EXACTLY like what he'd seen in that old late-60's Balladeer bowl in his photos (here's a reduced copy of Dans photo.):

Apparently, that "rough" area wasn't necessarily unique to those very early bowls afterall. I don't think it's an aftermarket repair, although it's possible that someone reached in from the soundhole to patch a hole or something. The outside of the bowl looks nearly perfect, except for one barely-detectable indentation in that general area which looks like it was hit from the outside by something. It could have been a factory repair, since they certainly would have been able to repaint the entire bowl to make it unnoticable from the outside, but has anyone ever heard of the factory patching bowls from the inside (with the top still attached) to repair them like that? (especially sometime after 1979?) A simpler explanation might be that it was (sometimes?) deemed unnecessary to sand and paint that part of the inside of the bowl because (almost) no one would ever see it anyway once the top was attached? (Or, maybe, if a bowl didn't pass inspecton, it was patched like that and then put back into the production line?) Interesting mystery (great guitar, regardless.) |
|
|
|
 Joined: June 2012 Posts: 2333
Location: Pueblo West, CO | Here's a bunch of pics of the inside of the various guitars I've worked on. If the inside of your bowl looks like these, then here's my explanation for the rough area.
It's simply a reinforcement for the strap mount. The fiberglass bowl is pretty thin -- two layers of cloth. This area of the bowl would distort with the weight of the player's arm pushing down on the lower bout while playing with a strap. To prevent the strap button (molly) from tearing out of the bowl, the MS added these extra layer(s) of cloth.
The rough surface texture is because they wet the area of the bowl where the cloth was going to go with epoxy, then laid on the cloth and wet it out. To get a smooth surface would have required a top coat of epoxy. Since no one was going to be 'touching' this area, or even seeing it, there was no reason to 'waste' the extra epoxy. The exception is the first bowl. This is Paul's 1117, which got a hand-laid bowl at its most recent factory visit. When the MS added the extra cloth, they top-coated it with epoxy.
If it's 'tan' that's just years and years of accumulated dust collecting in the nooks and crannies of the rough fiberglass cloth. If you were to take a stiff brush to this area, you could return it to its original color -- black. My 1111 looked the same way (see below) until I brushed out all the dirt. Paul's 1117-4 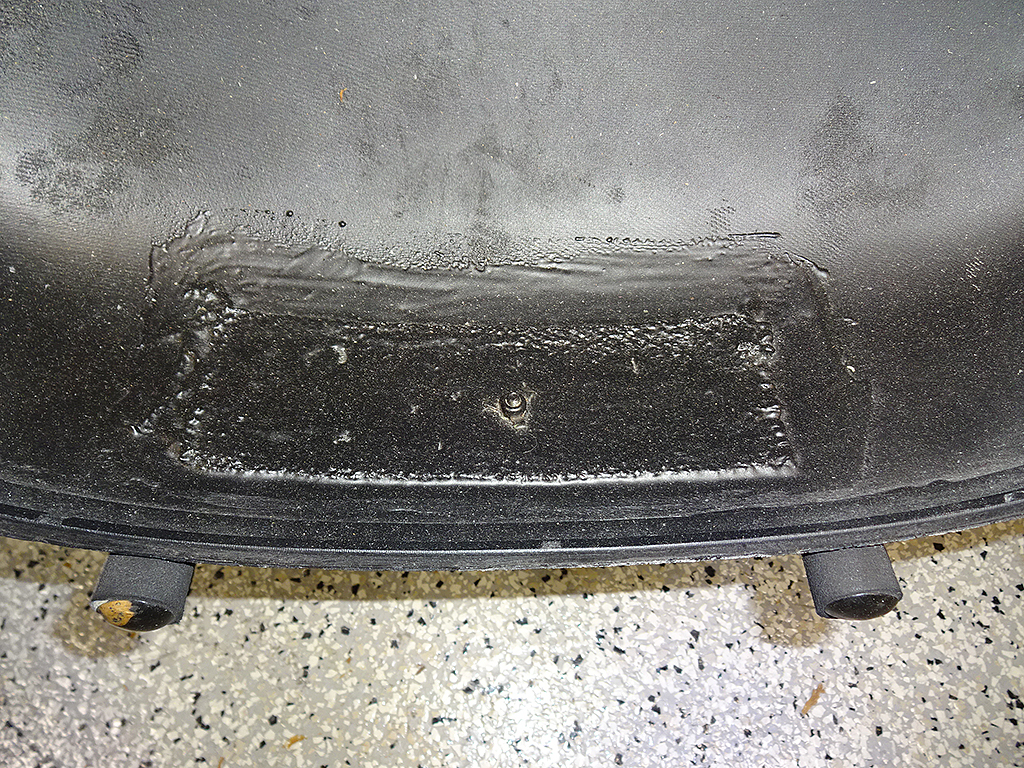
1111-4 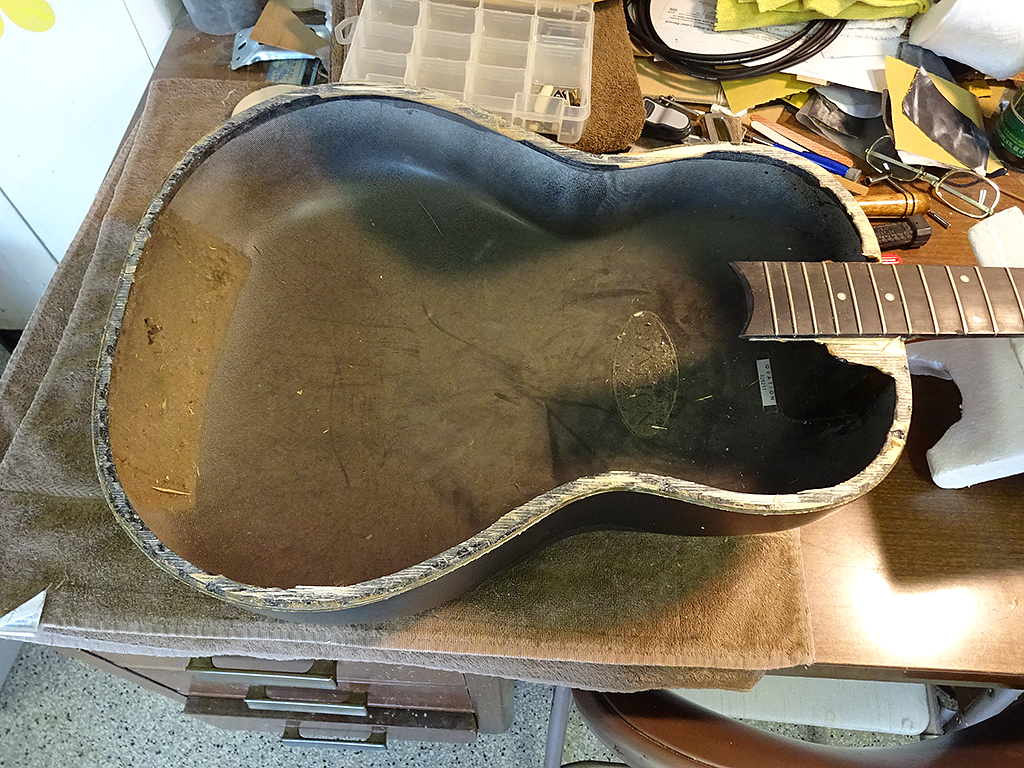
1113-4 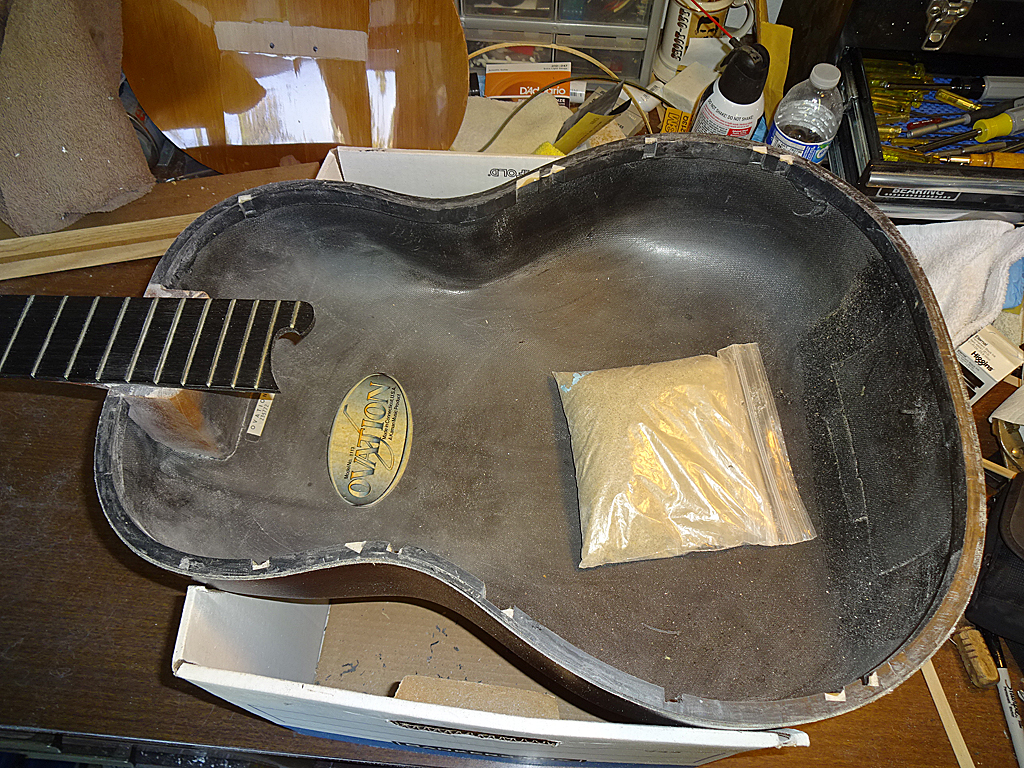
1117-4 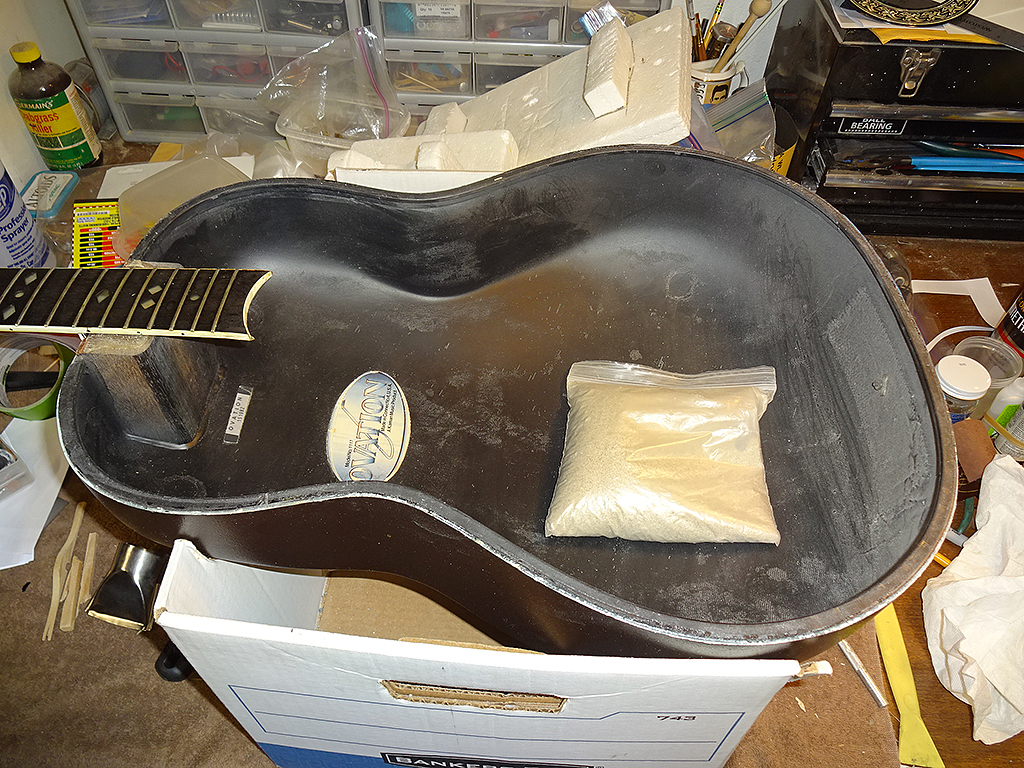
1617-4 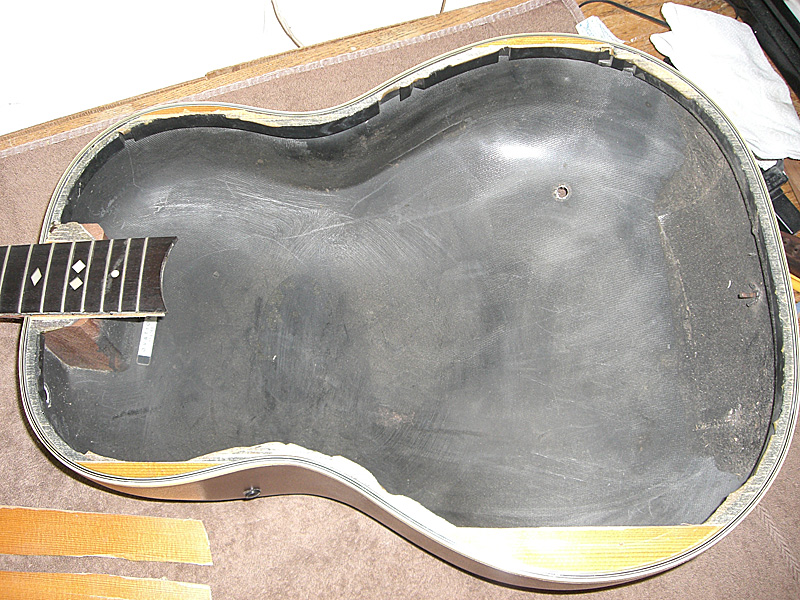
1619-4 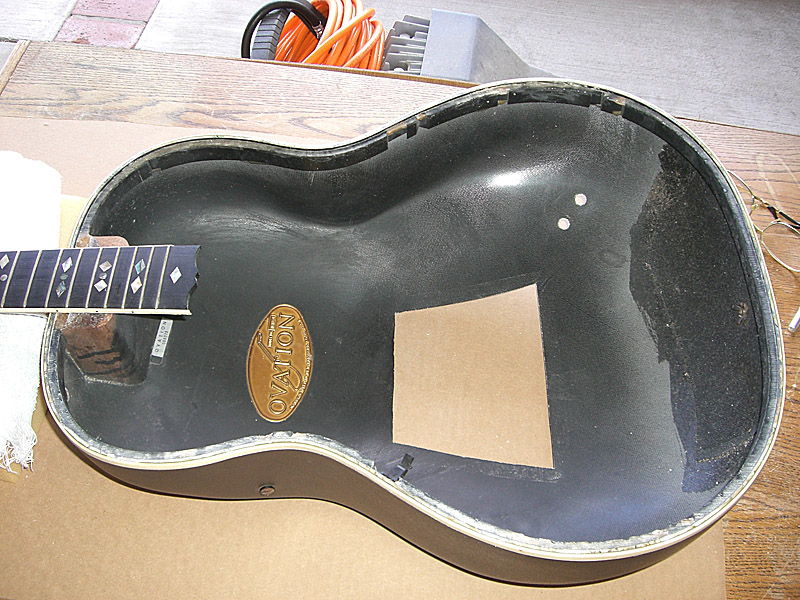
Edited by DanSavage 2017-02-20 10:00 AM
|
|
|
|
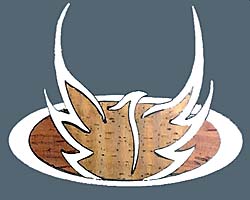 Joined: June 2002 Posts: 6202
Location: Phoenix AZ | It's kind of like a restaurant with good food but you don't necessarily want to look in the kitchen. |
|
|
|
 Joined: June 2012 Posts: 2333
Location: Pueblo West, CO | Yeah, no foolin'.
I love Gordon Ramsay's Kitchen Nightmares TV show. Heh heh heh... |
|
|
|
Joined: December 2008 Posts: 252
Location: Seattle | This is a interesting thread and well documented
Side question.
Noticed that some of my ovations are snagging my golf shirts.
Thinking it was just me I did a OFC search and found this has been discussed in 2006 under ”Ovation bowls are ruining my shirts! “
Out of curiosity ,which bowls tend to do this and why? |
|
|
|
 Joined: June 2012 Posts: 2333
Location: Pueblo West, CO | Thanks!
Weird. On which part of the guitar is your shirt being snagged? |
|
|
|
Joined: November 2002 Posts: 3650
Location: Pacific Northwest Inland Empire | And, how old is the guitar? Dry climate? Static electricity? Fiberglass delamination? Paint flaking? Contour bowl? Could be lots of stuff, here. |
|
|
|
 Joined: December 2008 Posts: 1455
Location: Texas | We finally know why OMA plays without a shirt…
|
|
|
|
Joined: December 2003 Posts: 852
Location: Canada | Great thread, thanks. So it seems the paint of my 1687 is flaking off there's some whit that shines through in places, and these are not places where there is any friction. Is there a way to prevent further damage and cover up the existing bald patches? I really like the sparkly paint. |
|
|
|
 Joined: June 2012 Posts: 2333
Location: Pueblo West, CO | d'ovation - 2017-11-23 1:55 PM
Great thread, thanks. So it seems the paint of my 1687 is flaking off there's some whit that shines through in places, and these are not places where there is any friction. Is there a way to prevent further damage and cover up the existing bald patches? I really like the sparkly paint.
I have developed a technique to 'duplicate' the pebbly look/feel of the original finish.
This arose from the need to blend the original finish into new binding when during the course of re-topping guitars.
It won't do anything to fix places where the old finish has poor adhesion like what you describe, but it can fix places where the underlying glass has become exposed.
I've never had the occasion to fix the gold speckling of the Adamas bowls, but that shouldn't be too hard to duplicate, either. |
|
|
|
Joined: December 2008 Posts: 252
Location: Seattle | The snag inducing bowls I have are the 2080 Adamas, and a new 2017 Legend Plus (Korea). Not a problem on my 1117 Legend ('73) and 1621 ('75).
but really..... Given all the things I could worry about this aint one of them. |
|
|
|
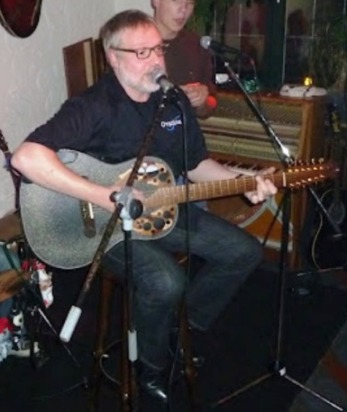 Joined: May 2011 Posts: 759
Location: Muenster/Germany | I want to talk about sound for a minute. We all know that different woods for back and sides create different guitars, and different bowls are no different.
I had a lot of Ovations and I did not know that in the early years other materials were used for the bowls. I only realized that guitars after 1982 were pretty heavy. From my personal taste the 70´s guitars were more delicate in sound and easier to handle, but the newer (SMC) guitars have definetely more power, more basses, sometimes you would not believe that such heavy guitars (esp. the 12strings 1538 and 1758) would produce any sound at all, but they do. My custom legend guitar built in 1982 is twice as "fundamental" as the two from the 70´s I had before.
Maybe the heavier bowl is the better for the Ovation guitar construction?
|
|
|
|
 Joined: January 2009 Posts: 1249
Location: Texas | The shiny bowl is as light as any bowl, imo...and produces a response equal or better than any other bowl Ovation came out with, acoustically, imo. As many times as this has been kicked around, I think it is clear that it is a sum of the parts, instead of a single part. |
|
|
|
 Joined: June 2012 Posts: 2333
Location: Pueblo West, CO | I just finished reading an interesting article that discusses using computer modeling to isolate the manner of sound generation in classical acoustic guitars. Among other things, it mainly talks about the relationship between the top, the air inside the guitar and the back/sides.
See: Mathematical Modelling and Acoustical Analysis of Classical Guitars and Their Soundboards As expected, there is a direct relationship between the movement of the top and the back due to the coupling of the two via the air piston contained inside the body. And, as expected, the top moves a lot more than the back because the air is somewhat compressible and the top is made to be more flexible than the back. WRT your observations, it's possible that the earlier thin cloth bowls created a response that is slightly out of phase with the top and cancels the propogation of sound waves throughout the body and out the sound hole. The stiffer bowl of later guitars vibrate less. Because their movement is more limited due to their thicker material, the sound waves are not canceled. Imagine, sitting in a bathtub full of water. If you slide forward and backward and wave can be generated which sweeps back and forth through the length of the tub. The amplitude of the wave can be increased by moving in time with the wave, but the timing (frequency) of how long it takes for the wave to reach from one end of the tub to the other is controlled mainly by the length of the tub. A longer tub would produce a lower frequency and a shorter one a higher frequency. Now, if you move out of phase with the wave, you can cause it to stop altogether. This is similar in concept to the thinner back which is more flexible and bounces back more quickly, which could accelerate the sound wave so it leaves the back at a higher rate than it arrived. So, instead of the top and back moving up and down together, they are now acting more like a bellows where one is moving up while the other is moving down. Also, as expected, thinner, more flexible material favors lower frequency sound waves (bass) and thicker, stiffer material favors higher frequencies. (treble) This becomes even more complicated when you have hand-laid, woven cloth fiberglass bowls whose thickness (and vibratory response) is controlled by how much resin the lay-up applied to that bowl. So, you could have one bowl that has more or less bass and more or less treble, depending on how it was laid-up. One thing that the SMC bowls did introduce was consistency of thickness and hence, response. As Jay points out, the end result is a sum of the parts. It's difficult to compare one guitar to another mainly because of the wood involved. Even when two guitars are built identically, the wood used in its construction has a lot to do with how it will sound. One of the things I found interesting about the documentation of the prototype Adamas guitars on the Ovation Tribute site is that by using composite tops, the factory reduced the number of variables required to produce consistently good-sounding guitars when compared to all-wood guitars. But even so, the factory still struggled to produce guitars with a consistent frequency response that their ears said sounded good. One would sound really good and the next, not-so-good. They had reduced the number of wood components to just the birch core of the top and the braces, but still have inconsitent results which needed fine-tuning. The above paper also talks about the relationship of the neck to the body and that even it can affect the final sound of the guitar.
Edited by DanSavage 2017-11-24 4:29 PM
|
|
|
|
Joined: March 2005 Posts: 2791
Location: Atlanta, GA. | When, where, how and why did the "shiny" bowls come to be in the mfg process?
I know... that's a lot to ask. |
|
|
|
Joined: March 2005 Posts: 2791
Location: Atlanta, GA. | Ackkkk....
Nevermind. I didn't notice there was a page 2 & 3 to the thread.
I'll go back and read more. |
|
|
|
Joined: July 2005 Posts: 1609
Location: Colorado | I took these these pictures just prior to the Slothead reunion - an epic event - first time in my life MY GUITAR was invited to an event and I got to tag along for the ride.
We wanted to determine which original pre-production slothead mine was - as the original label was long gone (The factory pulled the label off!). Darren wanted to look at it for a couple weeks because this particular guitar - once it got to me was played on the road for 2 dozen years - minimum 6 hours per day. Folks who have played it can really attest to the fact an Adamas will open up. They were in the process of making the reissues - so having instruments around to compare to was fun. Curiously they numbered and wrote weights on the braces in pencil - enough got documented when it was made - that all Beal, Darren, and Nick Macklin had to do was refer to the old large blue print records. Turns out it is #43, which has a storied "out of the factory-back into the factory history" It actually went out - came back - then went out again. Not sure what these pics tell you Dan, but here goes.
Edited by elginacres 2017-12-02 2:14 PM
(17 on bracing and mirror on 17 bracing.jpg)
(Bracing Showing #17.jpg)
(Close up showing mirror 17 and 3.jpg)
(IMG_0960.jpg)
(Mirror Image - Neck side bracing showing a 3 and a 17.jpg)
Attachments ----------------
17 on bracing and mirror on 17 bracing.jpg (121KB - 1 downloads)
Bracing Showing #17.jpg (46KB - 1 downloads)
Close up showing mirror 17 and 3.jpg (102KB - 1 downloads)
IMG_0960.jpg (83KB - 2 downloads)
Mirror Image - Neck side bracing showing a 3 and a 17.jpg (85KB - 0 downloads)
|
|
|
|
Joined: July 2005 Posts: 1609
Location: Colorado | Here are a few bowl pics from 2005, the blue print records, a stunning cameo of a pre-production Q, Bill doing the honors once it was determined to be #43, a blurry historical shot showing both Timm Kummer and Uncle Beal can play guitars...Cliff made the culminating photo for the calendar - but this one is the amateur photo hour version - with the kodak instamatic. Memories from the older guard.
(IMG_1387.jpg)
(IMG_1390.jpg)
(STA_1418.jpg)
(STA_1420.jpg)
(STB_1421.jpg)
(STB_1419.jpg)
(IMG_1409.jpg)
(IMG_1404.jpg)
(IMG_1415.jpg)
Attachments ----------------
IMG_1387.jpg (53KB - 0 downloads)
IMG_1390.jpg (73KB - 0 downloads)
STA_1418.jpg (55KB - 0 downloads)
STA_1420.jpg (32KB - 0 downloads)
STB_1421.jpg (32KB - 0 downloads)
STB_1419.jpg (48KB - 0 downloads)
IMG_1409.jpg (62KB - 0 downloads)
IMG_1404.jpg (43KB - 0 downloads)
IMG_1415.jpg (77KB - 0 downloads)
|
|
|
|
 Joined: June 2012 Posts: 2333
Location: Pueblo West, CO | elginacres - 2017-12-02 11:59 AM Turns out it is #43, which has a storied "out of the factory-back into the factory history" It actually went out - came back - then went out again.
Very cool. Thanks for posting the pics & info.
As it turns out, #43 pre-production Adamas is one of the guitars documented on Jerome's Ovation Tribute site vibratometer plots. The numbers on the printed spreadsheet match the sheet on Jerome's site.
See: Adamas #43 Vibrometer PlotsFrom the plot, it looks like a well-balanced sounding guitar. 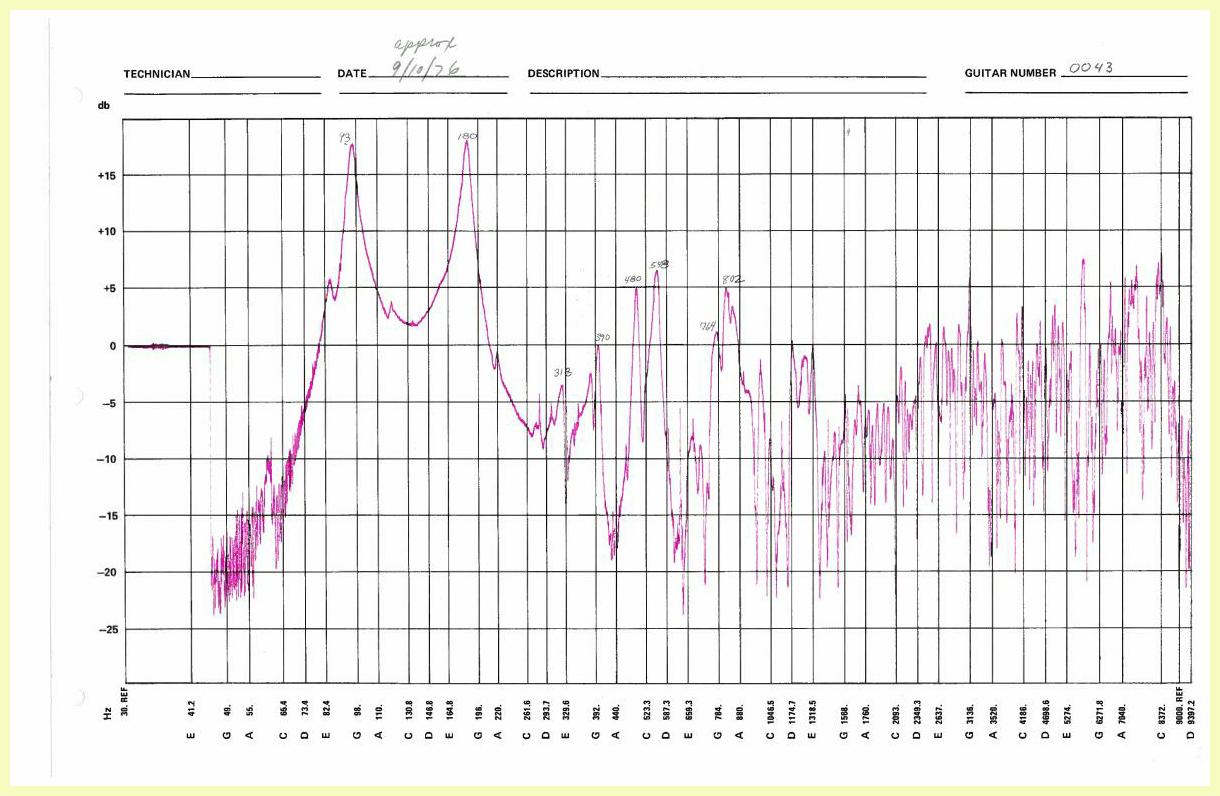
For a comparison, here's the plot from what they considered their optimum (prototype 26-3): 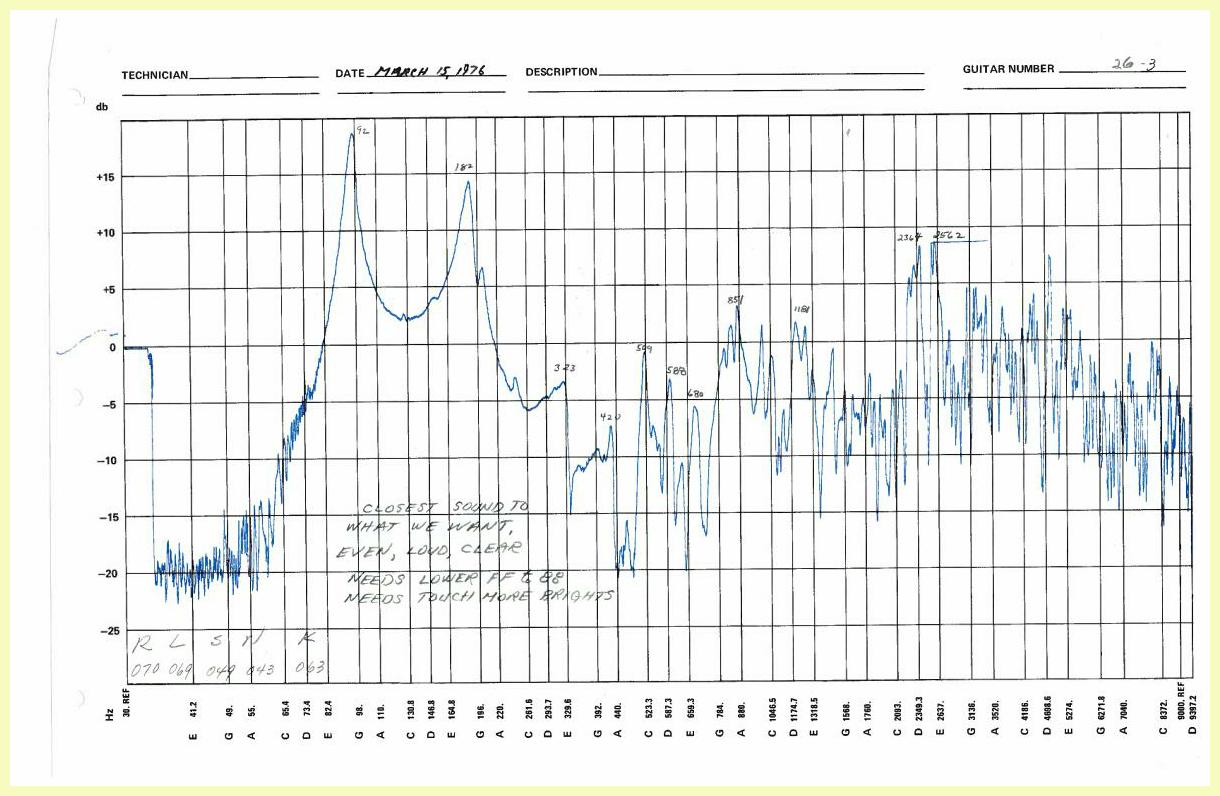
Edited by DanSavage 2017-12-02 7:27 PM
|
|
|
|
Joined: July 2005 Posts: 1609
Location: Colorado | How fun, I have the vibrometer readings from 2005...got dig around to find them. I know Darren was curious to see what had changed. Sent Jerome the pics a decade ago...good memories. |
|
|
|
 Joined: June 2012 Posts: 2333
Location: Pueblo West, CO | I'd like to see them, as well.
It would be cool to put one or two of my torrefied top ovations on the vibrometer and compare them to their non-torrefied counterparts. |
|
|
|
Joined: July 2005 Posts: 1609
Location: Colorado | Dan Savage: I found the plot Darren did in 2005 of OSH #43. I am curious what you say comparing the two plots with 29 years between them.
(43-2005-Vibrometer.jpg)
Attachments ----------------
43-2005-Vibrometer.jpg (29KB - 1 downloads)
|
|
|
|
 Joined: June 2012 Posts: 2333
Location: Pueblo West, CO | Very cool. Thanks for the post.
Unfortunately, the two plots use completely different notation and I don't know how to read the new plot. |
|
|
|
Joined: July 2005 Posts: 1609
Location: Colorado | Yeah - me neither - anyone? Bueller? |
|
|
|
Joined: December 2001 Posts: 10583
Location: NJ | wow that was a fun day!! |
|
|
|
Joined: December 2004 Posts: 574
Location: Denmark | I wonder how these vibrometer plots were made. What is input and what is output? The newest plot says "Swept sine wave" and is probably made by a microphone recording the sound emitted by the guitar at some distance with a vibrator/driver of some kind attached to the bridge. Such vibrator/driver can be a good tool when designing the sound board, but I would guess that the top/bracing/suspension design was done by experiment and judged by ears as normally done and the vibrometer measurements were done afterwards driven by curiosity and in effort to describe the result somehow. At that time frequency analysis of mechanical systems was really hot.
If the two plots were made in identical conditions they might the some of how the guitar soundboard changed over the years. To make such comparison be meaningful require a lot of experience in analysing and comparing these plots. It does seem that the two pronounced peeks at 90 and 183Hz have leveled out. This frequency interval corresponds to the interval of fundamentals from G on 6th string to F# above that. This, I believe, is good since such peaks also might indicate either a local resonance or less damping in that area which would make the guitar resonate differently - maybe less controlled - around these frequencies. Wolfnotes - such are also discussed in the article Dan refers to.
But I know nothing - I am just guessing :-) |
|
|
|
Joined: July 2005 Posts: 1609
Location: Colorado | Al - I agree - it was great day - meeting new...and now lifelong friends, putting our hands on many pre-production slotheads - peeking into the future that never quite unfolded - except for just a few - aka the "Q". Bill being the glue of it all, Frank, Rick, and Darren opening the shop and their hearts, listening to Timm's take on things, and Nick's recollections of how things really were. To the owners of these guitars - it is a eclectic group - and to you AL, the one who probably knows more about the models and selling the things...all a heart-felt great memory. I am also looking forward to what will happen in 2025 on the upcoming celebration of the 50th anniversary of what Nancy Wilson calls "Carbon Tops".
TPA - Darren Wallace wanted to measure the guitar to see what 30 years of playing it did to it...though it cannot be proven, it is likely due to its history, that #43 has had far more playing on it than any other of the originals. I will see if I can get Darren to chime in comparing the plots. |
|
|